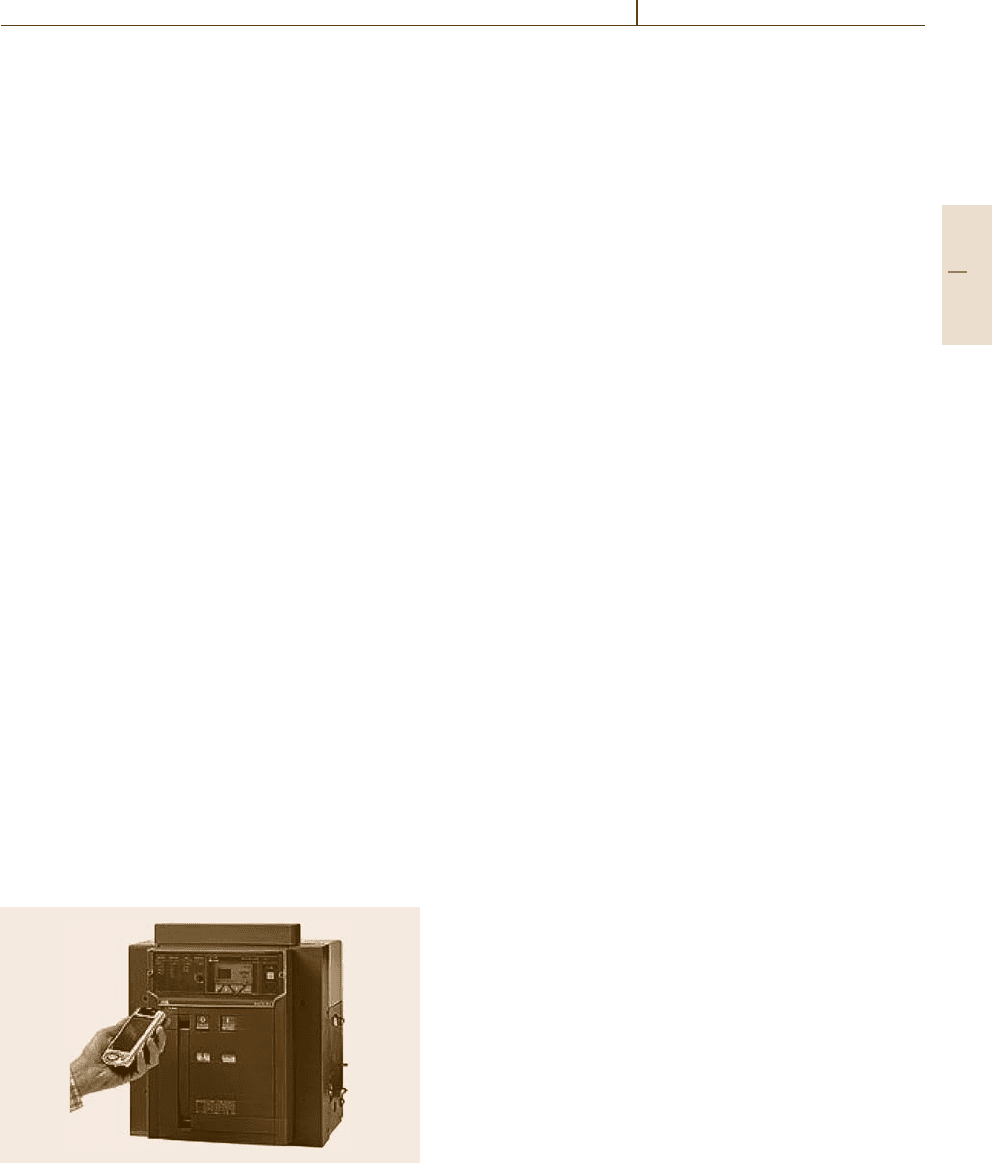
Product Automation 32.9 Elements for Product Automation 551
this information quickly and from anywhere, without
the need to plug a direct physical connections between
the trip unit and the PC or personal digital assistant
(PDA) are also features of modern products.
An important element in any circuit breaker is a cur-
rent sensor. In low-voltage circuit breakers, which are
fitted with electronic trip units, these sensors are not
only used for current measurement, but they must also
provide sufficient energy to power the electronics.
A commonly used sensor is a Rogowsky coil that
provides a signal proportional to the derivative of the
current – this signal needs to be integrated. This is done
digitally with a powerful digital signal processor (DSP),
which is part of the overall multiprocessor architecture,
and essentially theheart ofthe tripunit. Infact, this DSP
is used to carry out other functions, for example, com-
munications, that in previous designs required separate
hardware components.
The elimination of these hardware components
combined with a simplified trip unit input stage means
that a single printed circuit board (PCB) is all that is
required for the unit’s electronics. This is a vast im-
provement on previous designs where four PCBs were
needed to provide the same functionality.
The circuit breaker shown in Fig.32.6 also has
an integrated human–machine interface (HMI) [32.15].
A high-definition, low-power-consuming graphical dis-
play makes data easier to read. And, because of an
energy-storing capacitor, a descriptionof the alarms can
be displayed for up to 48 h without the need for an
auxiliary power supply. Nevertheless, these alarm de-
scriptions are saved and can be viewed long after this
48h periodhas elapsedby simplypoweringthe tripunit.
A wireless link, based on Bluetooth technology,
connects the trip unit to a portable PC, PDA or laptop.
This enables users to operate in a desktop environment
familiar to them. From this environment operators can
Fig. 32.6 HMI of a circuit breaker
use electric network dimensioning support programs to
ensure optimal adjustment of the protection functions.
In addition, users can print reports, save data on differ-
ent media, or send data by e-Mail to other parties from
the comfort of their own desk.
The use of fieldbus plug devices allows a choice of
fieldbus (e.g., DeviceNet or Profibus DP) that best suits
the user’s specific needs when connecting the circuit
breakers to an overall system.
32.9.3 Motors
Motors are the most common devices in produc-
tion automation, being part of production lines or
of robots [32.16]. The need to automate the motors
themselves is therefore very high, but also motors in
stand-alone application have automation features built
in for various reasons.
To avoid negative influence on the electrical supply
system when motors are switched on, the most common
automation device is the soft starter: when a certain
motor power output is required, the optimal solution
(depending on the power network conditions and re-
quirements) becomes a frequency converter start, also
called a soft start. This allows the motor to be started
at high torque without causing any voltage drop on the
power network.
The converter brings the motor up to speed. Upon
reaching nominal speed and after being synchronized to
the network, the circuit breaker between the converter
and the power network is opened. The breaker between
the motor and the network is then closed. Finally, the
breaker between the motor and the converter is opened.
The control systems to manage the motor come in
two basic varieties. Closed-loop control systems have
encoders in the motor to report its status. This is used as
feedback information for the control algorithm. Open-
loop systems are simpler because these encoders are
omitted, but at the price of a lower control accuracy.
With model-based control, however, the accuracy of
a closed-loop is achieved without encoders. ABB’s di-
rect torque control technology is an example for this
modern approach: it uses mathematical functions to
predict the motor status. The accuracy and repeatabil-
ity delivered is comparable to closed-loop systems, but
with the added bonus of a higher responsiveness (up to
ten times as fast).
Direct torque control (DTC) is a control method
that gives electronic variable-speed motor controllers
[alternating-current (AC) drives] an excellent torque
response time. For AC induction machines, it deliv-
Part D 32.9