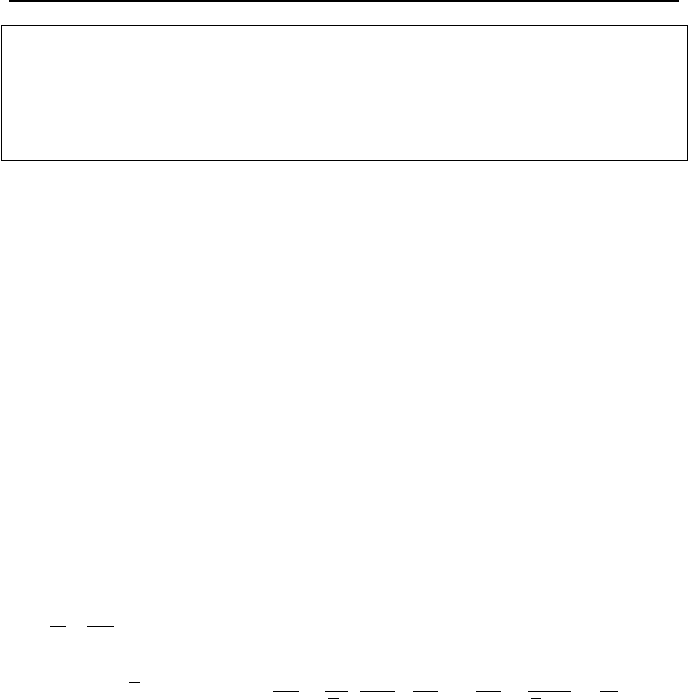
800 VId. Applications: Simulation of Thermofluid Systems
Example VId.3.3. Find the pressure difference due to the buoyancy force in a
flow loop. Data: P = 2250, T
Hot
= 600 F, T
Cold
= 550 F, Z
Heat Sink
= 61 ft, Z
Heat Source
= 31 ft. Working fluid is water.
Solution: We use Equation VId.3.14 to estimate ∆P
gravity
= (47.2 – 43.1) × (61 –
31) = 0.85 psi.
3.5. Natural Circulation in Flow Loops
Natural circulation is the preferred mode of operation when the enhancement of
the passive safety features, such as elimination of any pump failure, is a design re-
quirement. Some high rise buildings use natural circulation for the heating of their
units. This is accomplished by heating water in a boiler located in the basement
resulting in warm water flowing upward inside the riser. As water passes various
floors it deposits energy to heat the space. The colder and heavier water then
flows downward and back to the boiler, pushing the warmer water upward.
Hence, a necessary condition for establishment of natural circulation is that
H
th
> 0.
To estimate the natural circulation flow rate, we start with the single-loop of
Figure VId.3.4 and use Equation VId.2.3. Since this equation is obtained for a
single node, we integrate it over all the nodes comprising the loop. By doing so,
the static pressure difference term cancels out. Integrating Equation VId.2.3 is
equivalent to summing up all the terms of Equation IIIa.3.44 around the loop.
This results in:
()
1
22
1
22 2
11 1
1
11 1 1
K
22
n
k
k
nn n
pump k j j
k
kk k
kj j kk
k
k
Ldm
Adt
mmL
PgZZ f
DAA A
ρ
ρρ
=
+
== =
+
§·
=
¨¸
©¹
§·
§·
∆− −− − − +
¨¸
¨¸
©¹
©¹
¦
¦¦ ¦
VId.3.15
where in the case of Figure VId.3.4, n = 5. Equation VId.3.15 can be simplified
by noting that in a natural circulation loop, the pump head is zero. Note that the
pump head being zero does not necessarily mean that there is no pump in the loop.
Rather, the pump is simply not operating. A loop without a pump has by far less
frictional losses than an identical loop but equipped with a pump that is turned off.
This is because in the latter case, the working liquid must flow through the pump
volute and among the blades of the impeller. The losses due to friction in pumps
depend on the type of the pump and whether the impeller is locked or is free to
spin. For example, for the canned-motor pump of the LOFT (Reeder) experiment,
the loss coefficient for the free spinning impeller with flow in forward direction
(from pump suction to pump discharge) was estimated to be K = 3, for flow in the
reverse direction K = 12, and for flow through the pump with impeller locked
K = 20.