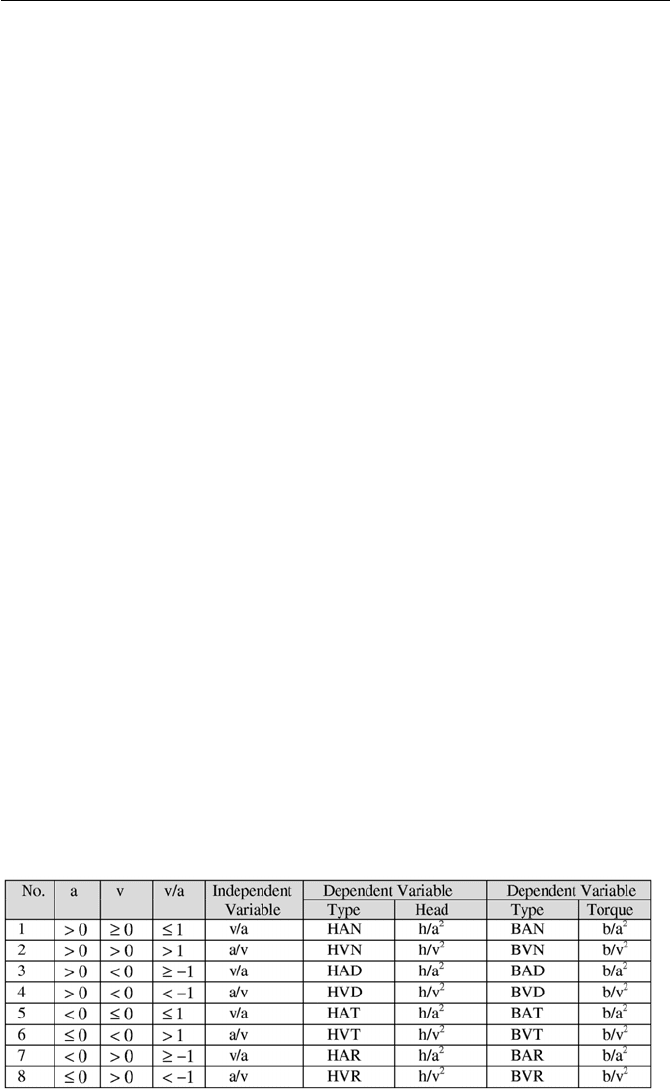
766 VIc. Applications: Fundamentals of Turbomachines
in computer analysis is impractical. Therefore, we resort to the non-dimensional
homologous curves to represent the pump characteristic curves. This, in turn, re-
quires the definition of some additional non-dimensional groups.
For a given pump, we use the rated data, which correspond to the point of best
efficiency, to normalize variables. Hence, we obtain speed ratio (a =
ω/ω
o
=
N/N
o
), flow ratio (v =
o
V/V
), head ratio (h = H/H
o
) and torque ratio (b = T/T
o
).
The flow, head, and torque coefficients now take the form of
V
C = b/v, C
H
= h/a
2
,
and C
T
= b/a
2
, respectively. We then can find C
H
and C
T
as functions of
V
C .
During analysis of pump response to a transient flow rate and impeller speed trav-
erse positive and negative values. As such, both variables may encounter zero. In
the case of the impeller speed, the values of the above coefficients would be unde-
termined. To avoid such conditions, we update our definition of the above coeffi-
cients and produce
2'
H
h/b=C and
2'
v/b=
T
C .
Generally, the head or torque coefficients (C
H
and C
T
or
'
H
C and
'
T
C ) as inde-
pendent variables are expressed in terms of flow and speed ratios (a and v). Since
there are also four quadrants where these independent variables should be deter-
mined, it has become customary to use shorthand (a three-letter notation) to iden-
tify various variables in various quadrants. The first letter identifies the dependent
variables (i.e., whether we are dealing with head or torque (h or b)). Hence, H
designates head and T designates torque ratios. The second letter, as a representa-
tive of the independent variable, is such that A designates division by a for the in-
dependent variable, and division by a
2
for the dependent variable. Similarly, V
designates division by v for the independent variable and division by v
2
for the
dependent variable. Finally, the third letter indicates the mode in which the pump
is operating, as shown in Figure VIc.4.3(b). These modes are N, R, T, and D for
Normal pump, Reverse pump, normal Turbine, and energy Dissipation, respec-
tively. These conventions are summarized in Table VIc.4.1, which defines 16
curves: 8 for head and 8 for torque. We now group similar curves of Ta-
ble VIc.4.1 to obtain only four curves as summarized in Table VIc.4.2. These four
homologous curves are shown for a typical centrifugal pump in Figure VIc.4.4(a)
for homologous head and in Figure VIc.4.4(b) for homologous torque.
Table VIc.4.1. Summary of homologous curve notations