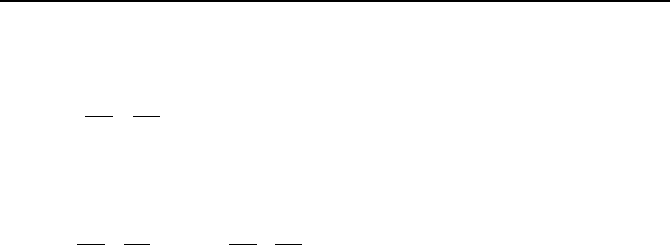
752 VIc. Applications: Fundamentals of Turbomachines
Total dynamic discharge head is the static discharge head plus the velocity
head plus the discharge friction head.
2
hh
2
ee
dePdf
PV
ZZ
gg
ρ
§·
=++−+
¨¸
©¹
Total dynamic head is the difference between total dynamic discharge and to-
tal dynamic suction head:
22
Hhh
22
ee ii
eifs
PV PV
ZZ
gg gg
ρρ
§·§·
=++−+++=
¨¸¨¸
©¹©¹
where hhh
fdfsf
=+
Vapor pressure of a liquid is the absolute pressure at which liquid vaporizes
and is in equilibrium with its vapor phase. If the liquid pressure drops below the
vapor pressure, the liquid boils. If liquid pressure is greater than the vapor pres-
sure, then the liquid vaporizes at the interface between the two phases. The vapor
pressure of water at 80 F (27 C), for example, is P
V
= 0.50683 psia (3.5 kPa).
Similar definition is given in Section IIa.1.4. If pressure at the eye of the pump
drops below the vapor pressure then the pump begins to cavitate.
Cavitation is the major cause of damage to pumps and valves where liquid ex-
periences a large and sudden pressure drop. Cavitation is defined as formation,
via vaporization, and subsequent collapse, via condensation, of vapor bubbles in a
liquid. A pressure drop to or below the liquid vapor pressure coupled with exist-
ing nuclei (tiny voids containing vapor or gas) results in liquid vaporization.
These voids appear as tiny bubbles that will grow if the surrounding pressure re-
mains at or below the vapor pressure of the liquid or they will collapse at higher
pressures. Pressure drop occurs at such locations as tip of a propeller, edges of a
thin-plate orifice, or seats of a valve. These unrecoverable pressure losses in these
places are associated with dissipation of energy, which constitutes the loss coeffi-
cient of valves and fittings. Collapse of bubbles in higher-pressure regions is as-
sociated with rapid pressure fluctuations that will eventually result in erosion and
pitting of the hydraulic structure.
There are various means of preventing cavitation, primarily depending on the
type of the hydraulic system. Prevention of cavitation in a pump is discussed in
Section 3. In some hydraulics systems, it may be possible to introduce a gradual
pressure drop to the flow. Cavitation control valves may use a tortuous flow path,
cascaded orifices, or a combination of both to cause high velocity hence, large lo-
cal frictional losses. Another means of preventing material erosion due to cavita-
tion is to use erosion resistant materials at locations prone to cavitation, such as
the use of stainless steel for a turbine blade, valve seat, or pump impeller. As
shown in Figure VIc.2.2, during operation we must ensure that P
eye
> P
vapor
.
Best efficiency point (BEP) is an operation mode at which the pump efficiency
is a maximum. While pumps should be operated at their BEP, it is especially im-