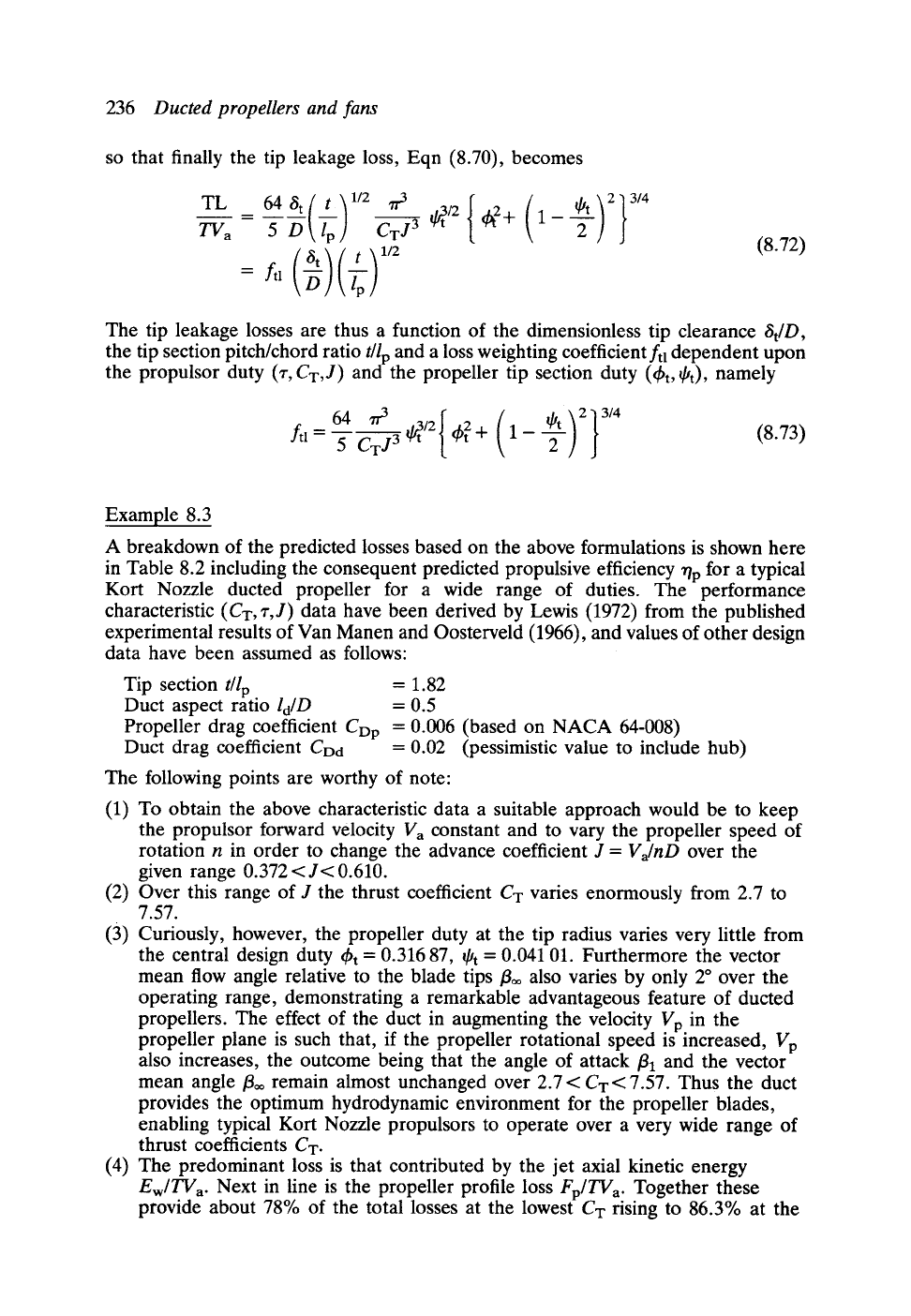
236
Ducted propellers and fans
so that finally the tip leakage loss, Eqn (8.70), becomes
TV a - 5 O CT J'''--'~ -'-2"-
8 t t
1/2
21
3/4
(8.72)
The tip leakage losses are thus a function of the dimensionless tip clearance
~t/D,
the tip section pitch/chord ratio
t/lp
and a loss weighting coefficient
ftl
dependent upon
the propulsor duty
(z, CT,J)
and the propeller tip section duty (~bt, @t), namely
ft1=645
CTJ 3 ~r3
~t/2{th2+ (
_~) 2 } 3/4
1 - (8.73)
Example 8.3
A breakdown of the predicted losses based on the above formulations is shown here
in Table 8.2 including the consequent predicted propulsive efficiency r/p for a typical
Kort Nozzle ducted propeller for a wide range of duties. The performance
characteristic (CT, r,J) data have been derived by Lewis (1972) from the published
experimental results of Van Manen and Oosterveld (1966), and values of other design
data have been assumed as follows:
Tip section
t/lp
= 1.82
Duct aspect ratio
ld/D
= 0.5
Propeller drag coefficient CDp = 0.006 (based on NACA 64-008)
Duct drag coefficient CDd = 0.02 (pessimistic value to include hub)
The following points are worthy of note"
(1) To obtain the above characteristic data a suitable approach would be to keep
the propulsor forward velocity Va constant and to vary the propeller speed of
rotation n in order to change the advance coefficient J =
Va/nD
over the
given range 0.372 <J<0.610.
(2) Over this range of J the thrust coefficient CT varies enormously from 2.7 to
7.57.
(3) Curiously, however, the propeller duty at the tip radius varies very little from
the central design duty ~bt = 0.316 87, @t = 0.041 01. Furthermore the vector
mean flow angle relative to the blade tips/3~ also varies by only 2 ~ over the
operating range, demonstrating a remarkable advantageous feature of ducted
propellers. The effect of the duct in augmenting the velocity Vp in the
propeller plane is such that, if the propeller rotational speed is increased, Vp
also increases, the outcome being that the angle of attack/31 and the vector
mean angle/3~ remain almost unchanged over 2.7 < CT< 7.57. Thus the duct
provides the optimum hydrodynamic environment for the propeller blades,
enabling typical Kort Nozzle propulsors to operate over a very wide range of
thrust coefficients Ca,.
(4) The predominant loss is that contributed by the jet axial kinetic energy
Ew/TVa.
Next in line is the propeller profile loss
Fp/TVa.
Together these
provide about 78% of the total losses at the lowest Ca- rising to 86.3% at the