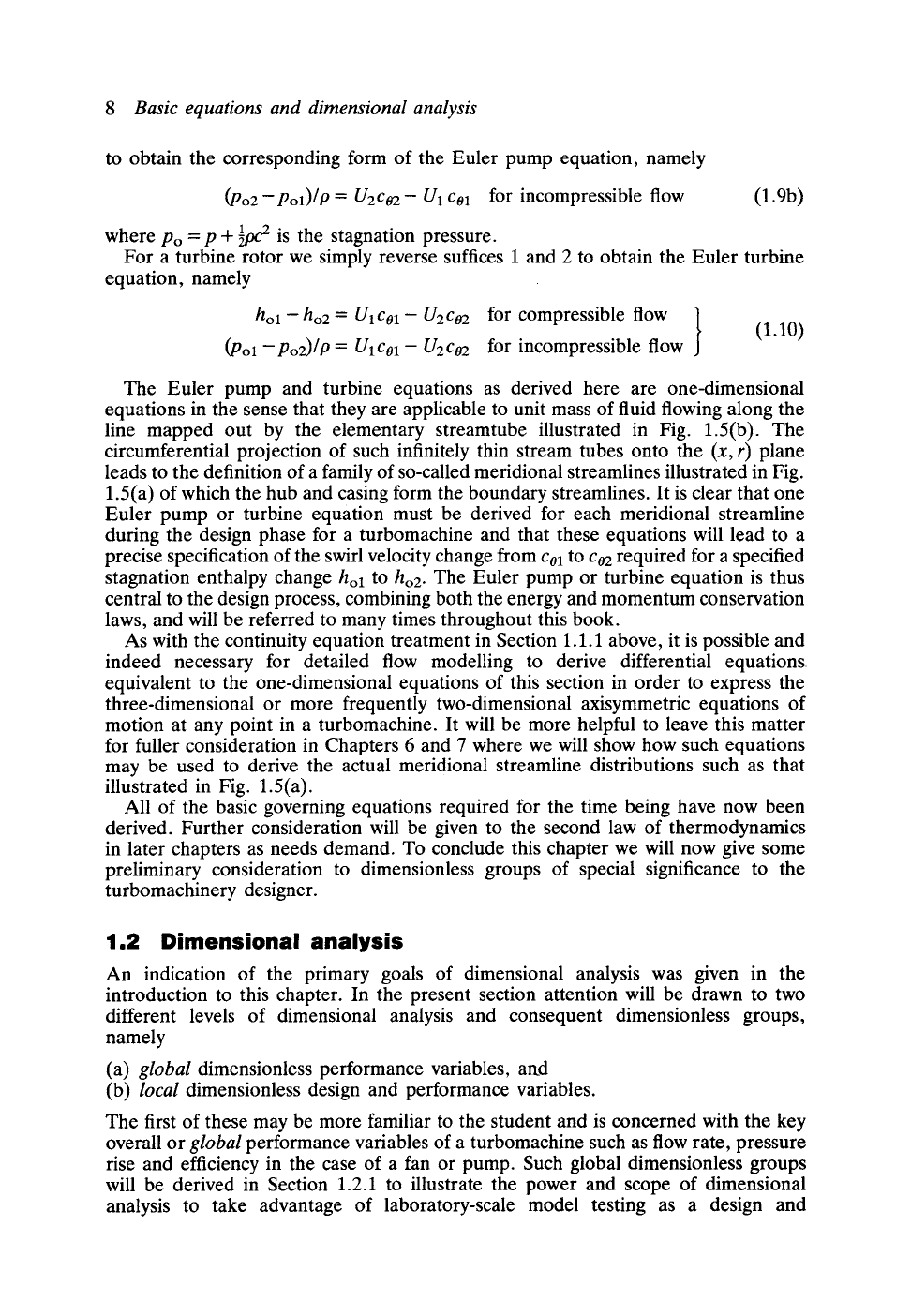
8 Basic equations and dimensional analysis
to obtain the corresponding form of the Euler pump equation, namely
(Po2-Pol)/P = U2co2- U1 col for incompressible flow (1.9b)
where Po = P + -~ is the stagnation pressure.
For a turbine rotor we simply reverse suffices 1 and 2 to obtain the Euler turbine
equation, namely
hol - ho2 = UlCol - U2co2 for compressible flow } (1.10)
(Pol-Po2)/P = UlCol- U2co2 for incompressible flow
The Euler pump and turbine equations as derived here are one-dimensional
equations in the sense that they are applicable to unit mass of fluid flowing along the
line mapped out by the elementary streamtube illustrated in Fig. 1.5(b). The
circumferential projection of such infinitely thin stream tubes onto the (x, r) plane
leads to the definition of a family of so-called meridional streamlines illustrated in Fig.
1.5(a) of which the hub and casing form the boundary streamlines. It is clear that one
Euler pump or turbine equation must be derived for each meridional streamline
during the design phase for a turbomachine and that these equations will lead to a
precise specification of the swirl velocity change from col to c02 required for a specified
stagnation enthalpy change
hol to ho2.
The Euler pump or turbine equation is thus
central to the design process, combining both the energy and momentum conservation
laws, and will be referred to many times throughout this book.
As with the continuity equation treatment in Section 1.1.1 above, it is possible and
indeed necessary for detailed flow modelling to derive differential equations
equivalent to the one-dimensional equations of this section in order to express the
three-dimensional or more frequently two-dimensional axisymmetric equations of
motion at any point in a turbomachine. It will be more helpful to leave this matter
for fuller consideration in Chapters 6 and 7 where we will show how such equations
may be used to derive the actual meridional streamline distributions such as that
illustrated in Fig. 1.5(a).
All of the basic governing equations required for the time being have now been
derived. Further consideration will be given to the second law of thermodynamics
in later chapters as needs demand. To conclude this chapter we will now give some
preliminary consideration to dimensionless groups of special significance to the
turbomachinery designer.
1.2 Dimensional analysis
An indication of the primary goals of dimensional analysis was given in the
introduction to this chapter. In the present section attention will be drawn to two
different levels of dimensional analysis and consequent dimensionless groups,
namely
(a) global dimensionless performance variables, artd
(b) local dimensionless design and performance variables.
The first of these may be more familiar to the student and is concerned with the key
overall or global performance variables of a turbomachine such as flow rate, pressure
rise and efficiency in the case of a fan or pump. Such global dimensionless groups
will be derived in Section 1.2.1 to illustrate the power and scope of dimensional
analysis to take advantage of laboratory-scale model testing as a design and