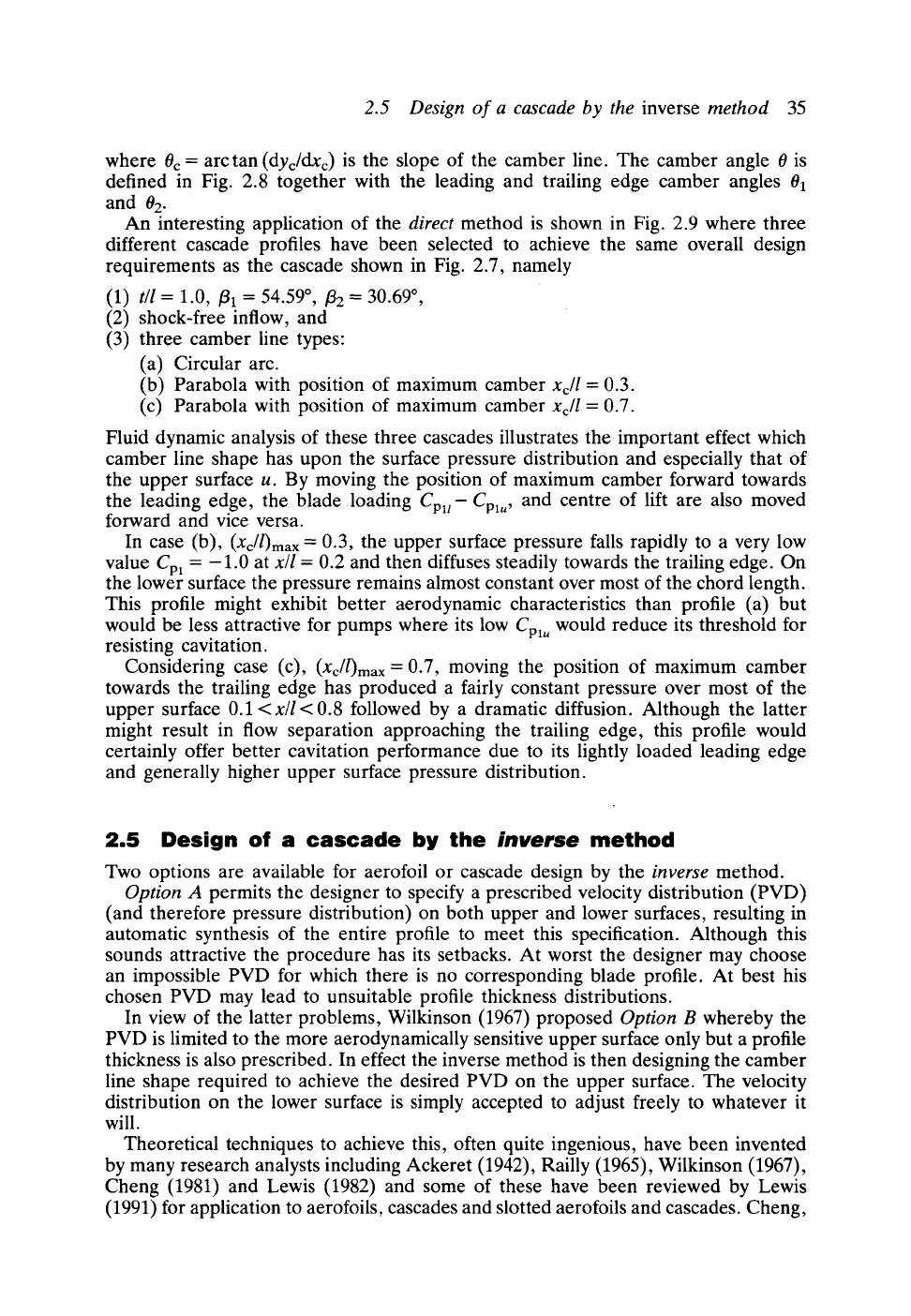
2.5 Design of a cascade by the inverse method 35
where 0~ = arc tan (dyc/dxc) is the slope of the camber line. The camber angle 0 is
defined in Fig. 2.8 together with the leading and trailing edge camber angles 01
and 02.
An interesting application of the direct method is shown in Fig. 2.9 where three
different cascade profiles have been selected to achieve the same overall design
requirements as the cascade shown in Fig. 2.7, namely
(1) t/l = 1.0,
fll :
54.59~ 132 = 30.69 ~
(2) shock-free inflow, and
(3) three camber line types:
(a) Circular arc.
(b) Parabola with position of maximum camber xc/l- 0.3.
(c) Parabola with position of maximum camber xc/l- 0.7.
Fluid dynamic analysis of these three cascades illustrates the important effect which
camber line shape has upon the surface pressure distribution and especially that of
the upper surface u. By moving the position of maximum camber forward towards
the leading edge, the blade loading Cp~-Cp~, and centre of lift are also moved
forward and vice versa.
In case (b),
(Xc/l)max--0.3,
the upper surface pressure falls rapidly to avery low
value Cp~ = -1.0 at x/l = 0.2 and then diffuses steadily towards the trailing edge. On
the lower surface the pressure remains almost constant over most of the chord length.
This profile might exhibit better aerodynamic characteristics than profile (a) but
would be less attractive for pumps where its low Cp~ u would reduce its threshold for
resisting cavitation.
Considering case (c),
(Xc/l)max
= 0.7,
moving the position of maximum camber
towards the trailing edge has produced a fairly constant pressure over most of the
upper surface 0.1 <x/l < 0.8 followed by a dramatic diffusion. Although the latter
might result in flow separation approaching the trailing edge, this profile would
certainly offer better cavitation performance due to its lightly loaded leading edge
and generally higher upper surface pressure distribution.
2.5 Design of a cascade by the
inverse
method
Two options are available for aerofoil or cascade design by the inverse method.
Option A permits the designer to specify a prescribed velocity distribution (PVD)
(and therefore pressure distribution) on both upper and lower surfaces, resulting in
automatic synthesis of the entire profile to meet this specification. Although this
sounds attractive the procedure has its setbacks. At worst the designer may choose
an impossible PVD for which there is no corresponding blade profile. At best his
chosen PVD may lead to unsuitable profile thickness distributions.
In view of the latter problems, Wilkinson (1967) proposed Option B whereby the
PVD is limited to the more aerodynamically sensitive upper surface only but a profile
thickness is also prescribed. In effect the inverse method is then designing the camber
line shape required to achieve the desired PVD on the upper surface. The velocity
distribution on the lower surface is simply accepted to adjust freely to whatever it
will.
Theoretical techniques to achieve this, often quite ingenious, have been invented
by many research analysts including Ackeret (1942), Railly (1965), Wilkinson (1967),
Cheng (1981) and Lewis (1982) and some of these have been reviewed by Lewis
(1991) for application to aerofoils, cascades and slotted aerofoils and cascades. Cheng,