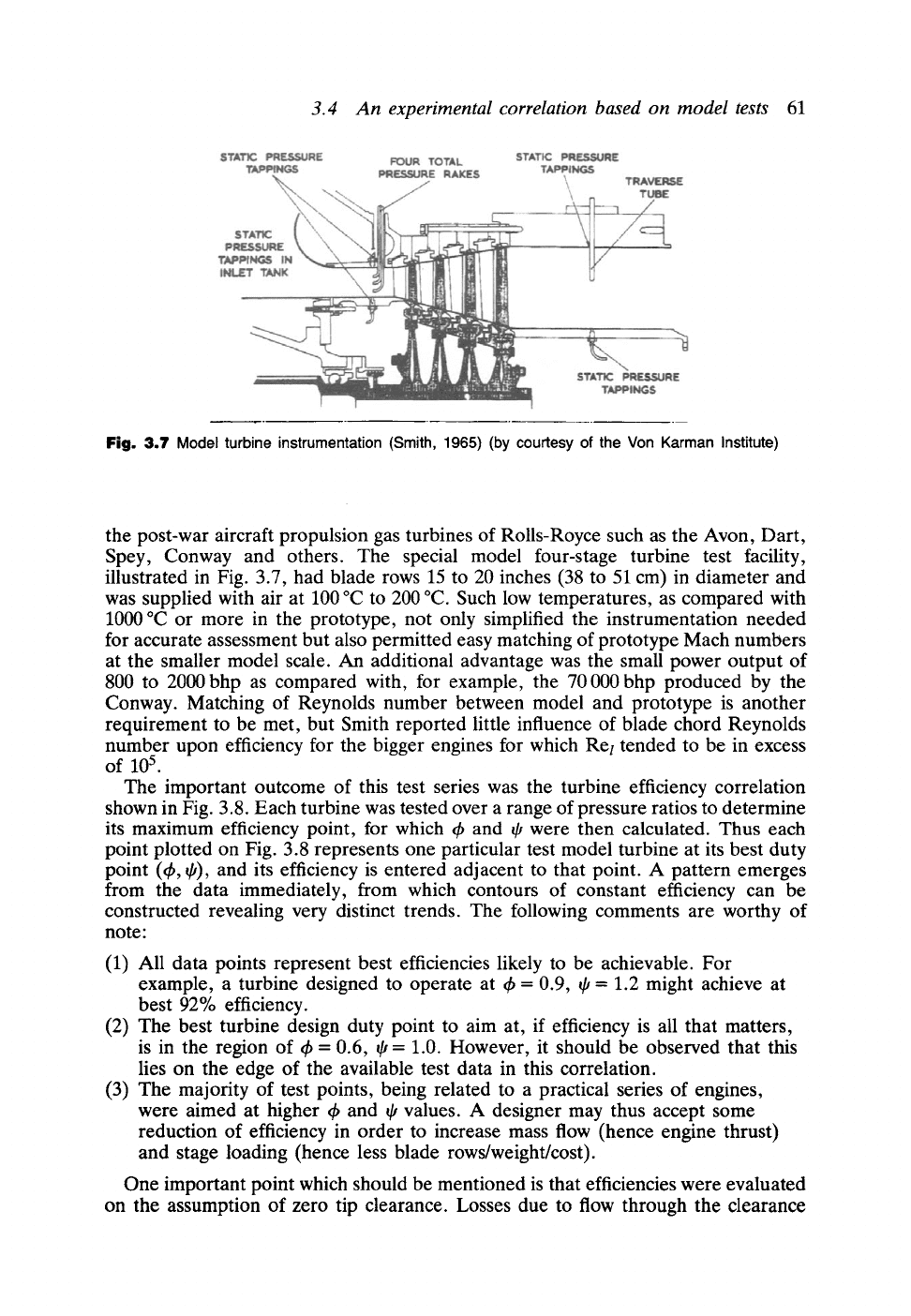
3.4 An experimental correlation based on model tests
61
Fig. 3.7
Model turbine instrumentation (Smith, 1965) (by courtesy of the Von Karman Institute)
the post-war aircraft propulsion gas turbines of Rolls-Royce such as the Avon, Dart,
Spey, Conway and others. The special model four-stage turbine test facility,
illustrated in Fig. 3.7, had blade rows 15 to 20 inches (38 to 51 cm) in diameter and
was supplied with air at 100 ~ to 200 ~ Such low temperatures, as compared with
1000 ~ or more in the prototype, not only simplified the instrumentation needed
for accurate assessment but also permitted easy matching of prototype Mach numbers
at the smaller model scale. An additional advantage was the small power output of
800 to 2000 bhp as compared with, for example, the 70000 bhp produced by the
Conway. Matching of Reynolds number between model and prototype is another
requirement to be met, but Smith reported little influence of blade chord Reynolds
number upon efficiency for the bigger engines for which Ret tended to be in excess
of 105 .
The important outcome of this test series was the turbine efficiency correlation
shown in Fig. 3.8. Each turbine was tested over a range of pressure ratios to determine
its maximum efficiency point, for which ~b and q~ were then calculated. Thus each
point plotted on Fig. 3.8 represents one particular test model turbine at its best duty
point (~b, qJ), and its efficiency is entered adjacent to that point. A pattern emerges
from the data immediately, from which contours of constant efficiency can be
constructed revealing very distinct trends. The following comments are worthy of
note:
(1) All data points represent best efficiencies likely to be achievable. For
example, a turbine designed to operate at ~b = 0.9, q~ = 1.2 might achieve at
best 92% efficiency.
(2) The best turbine design duty point to aim at, if efficiency is all that matters,
is in the region of ~b = 0.6, q~ = 1.0. However, it should be observed that this
lies on the edge of the available test data in this correlation.
(3) The majority of test points, being related to a practical series of engines,
were aimed at higher ~b and qJ values. A designer may thus accept some
reduction of efficiency in order to increase mass flow (hence engine thrust)
and stage loading (hence less blade rows/weight/cost).
One important point which should be mentioned is that efficiencies were evaluated
on the assumption of zero tip clearance. Losses due to flow through the clearance