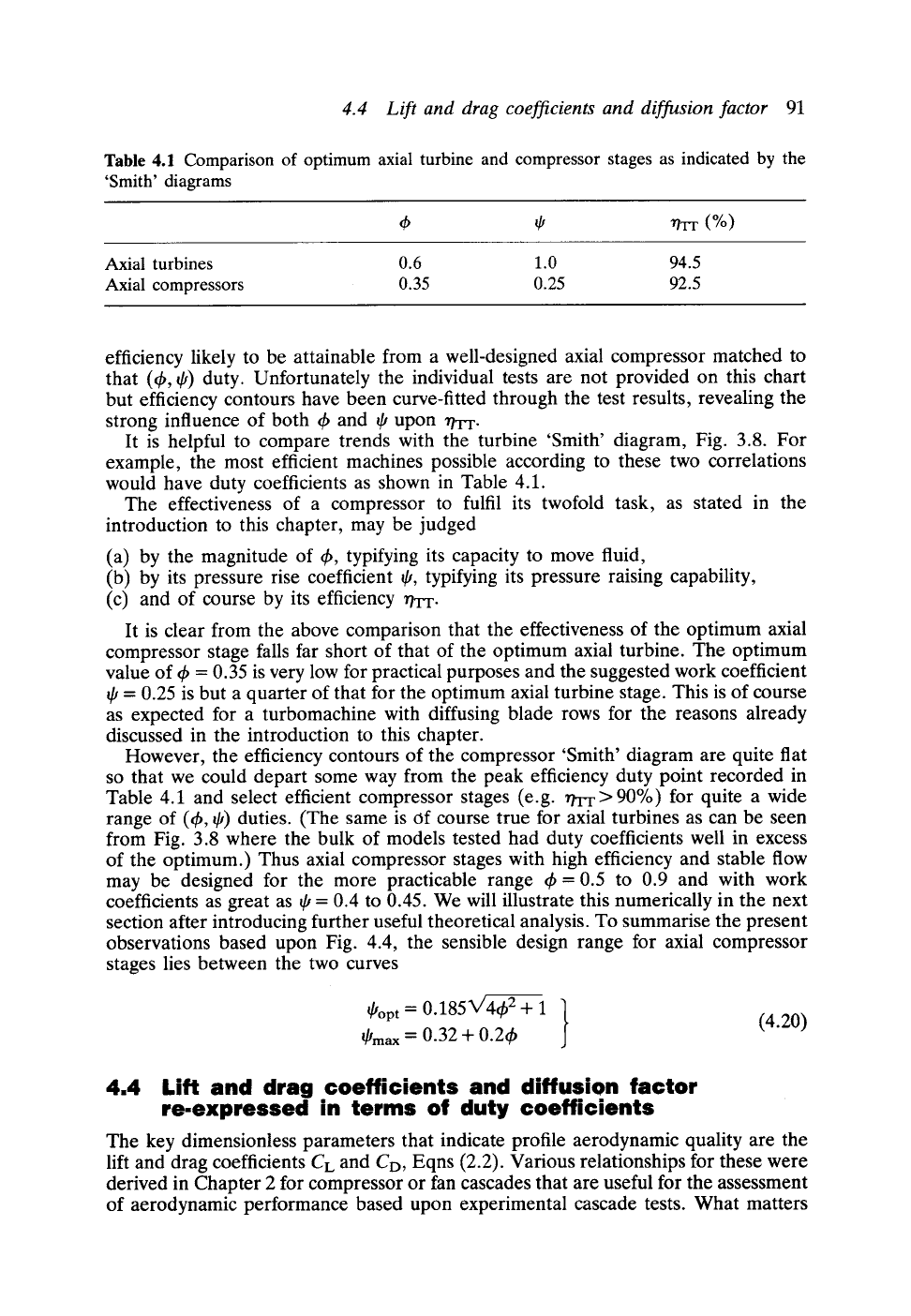
4.4 Lift and drag coefficients and diffusion factor
91
Table 4.1 Comparison of optimum axial turbine and compressor stages as indicated by the
'Smith' diagrams
q, na-r (%)
Axial turbines 0.6 1.0 94.5
Axial compressors 0.35 0.25 92.5
efficiency likely to be attainable from a well-designed axial compressor matched to
that (t h, q,) duty. Unfortunately the individual tests are not provided on this chart
but efficiency contours have been curve-fitted through the test results, revealing the
strong influence of both 4, and q, upon r/an:.
It is helpful to compare trends with the turbine 'Smith' diagram, Fig. 3.8. For
example, the most efficient machines possible according to these two correlations
would have duty coefficients as shown in Table 4.1.
The effectiveness of a compressor to fulfil its twofold task, as stated in the
introduction to this chapter, may be judged
(a) by the magnitude of ~b, typifying its capacity to move fluid,
(b) by its pressure rise coefficient qJ, typifying its pressure raising capability,
(c) and of course by its efficiency r/an:.
It is clear from the above comparison that the effectiveness of the optimum axial
compressor stage falls far short of that of the optimum axial turbine. The optimum
value of 4, = 0.35 is very low for practical purposes and the suggested work coefficient
q, = 0.25 is but a quarter of that for the optimum axial turbine stage. This is of course
as expected for a turbomachine with diffusing blade rows for the reasons already
discussed in the introduction to this chapter.
However, the efficiency contours of the compressor 'Smith' diagram are quite fiat
so that we could depart some way from the peak efficiency duty point recorded in
Table 4.1 and select efficient compressor stages (e.g. rtrr > 90%) for quite a wide
range of (~b, q,) duties. (The same is of course true for axial turbines as can be seen
from Fig. 3.8 where the bulk of models tested had duty coefficients well in excess
of the optimum.) Thus axial compressor stages with high efficiency and stable flow
may be designed for the more practicable range ~b = 0.5 to 0.9 and with work
coefficients as great as q, = 0.4 to 0.45. We will illustrate this numerically in the next
section after introducing further useful theoretical analysis. To summarise the present
observations based upon Fig. 4.4, the sensible design range for axial compressor
stages lies between the two curves
I/top t =
O. 185
V'4q~ 2 +
1
~max
=
0.32 + 0.2~b
J
(4.20)
4,4
Lift and drag coefficients and diffusion factor
re.expressed in terms of duty coefficients
The key dimensionless parameters that indicate profile aerodynamic quality are the
lift and drag coefficients CL and CD, Eqns (2.2). Various relationships for these were
derived in Chapter 2 for compressor or fan cascades that are useful for the assessment
of aerodynamic performance based upon experimental cascade tests. What matters