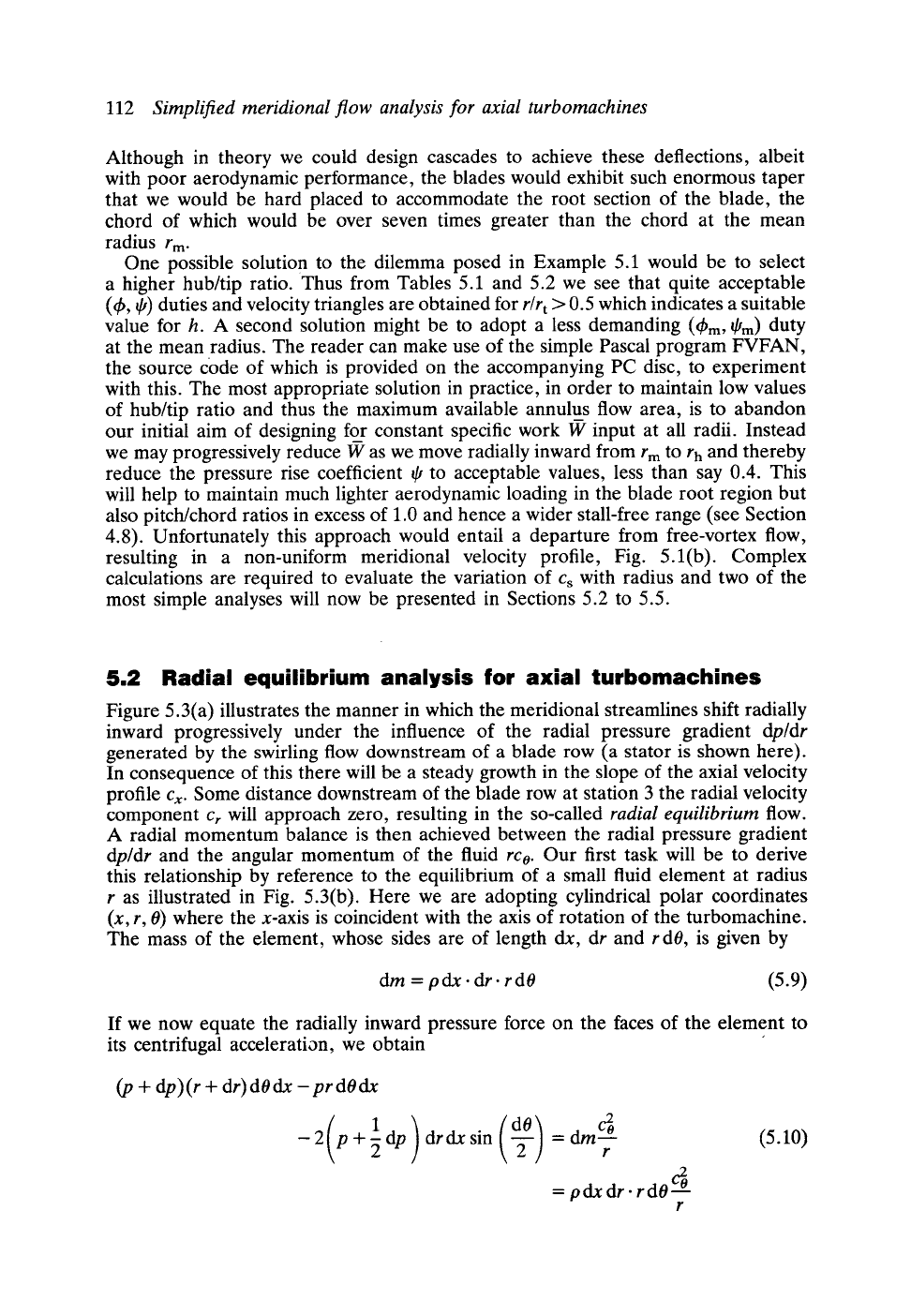
112 Simplified meridional flow analysis for axial turbomachines
Although in theory we could design cascades to achieve these deflections, albeit
with poor aerodynamic performance, the blades would exhibit such enormous taper
that we would be hard placed to accommodate the root section of the blade, the
chord of which would be over seven times greater than the chord at the mean
radius r m.
One possible solution to the dilemma posed in Example 5.1 would be to select
a higher hub/tip ratio. Thus from Tables 5.1 and 5.2 we see that quite acceptable
(~b, ~,) duties and velocity triangles are obtained for
r/r t
>
0.5 which indicates a suitable
value for h. A second solution might be to adopt a less demanding (thm, ~'m) duty
at the mean radius. The reader can make use of the simple Pascal program FVFAN,
the source code of which is provided on the accompanying PC disc, to experiment
with this. The most appropriate solution in practice, in order to maintain low values
of hub/tip ratio and thus the maximum available annulus flow area, is to abandon
our initial aim of designing for constant specific work W input at all radii. Instead
we may progressively reduce W as we move radially inward from r m
to
rh and thereby
reduce the pressure rise coefficient ~, to acceptable values, less than say 0.4. This
will help to maintain much lighter aerodynamic loading in the blade root region but
also pitch/chord ratios in excess of 1.0 and hence a wider stall-free range (see Section
4.8). Unfortunately this approach would entail a departure from free-vortex flow,
resulting in a non-uniform meridional velocity profile, Fig. 5.1(b). Complex
calculations are required to evaluate the variation of Cs with radius and two of the
most simple analyses will now be presented in Sections 5.2 to 5.5.
5.2 Radial equilibrium analysis for axial turbomachines
Figure 5.3(a) illustrates the manner in which the meridional streamlines shift radially
inward progressively under the influence of the radial pressure gradient dp/dr
generated by the swirling flow downstream of a blade row (a stator is shown here).
In consequence of this there will be a steady growth in the slope of the axial velocity
profile Cx. Some distance downstream of the blade row at station 3 the radial velocity
component Cr will approach zero, resulting in the so-called radial equilibrium flow.
A radial momentum balance is then achieved between the radial pressure gradient
dp/dr and the angular momentum of the fluid rco. Our first task will be to derive
this relationship by reference to the equilibrium of a small fluid element at radius
r as illustrated in Fig. 5.3(b). Here we are adopting cylindrical polar coordinates
(x, r, 0) where the x-axis is coincident with the axis of rotation of the turbomachine.
The mass of the element, whose sides are of length dx, dr and r dO, is given by
dm = pdx. dr- r dO (5.9)
If we now equate the radially inward pressure force on the faces of the element to
its centrifugal acceleration, we obtain
(p + dp)(r + dr)dOdx-prdOdx
( 1
-2
p+gdp
) 2
drdx sin ~ = dm c'b (5.10)
r
= pdx dr. rdO c2~
r