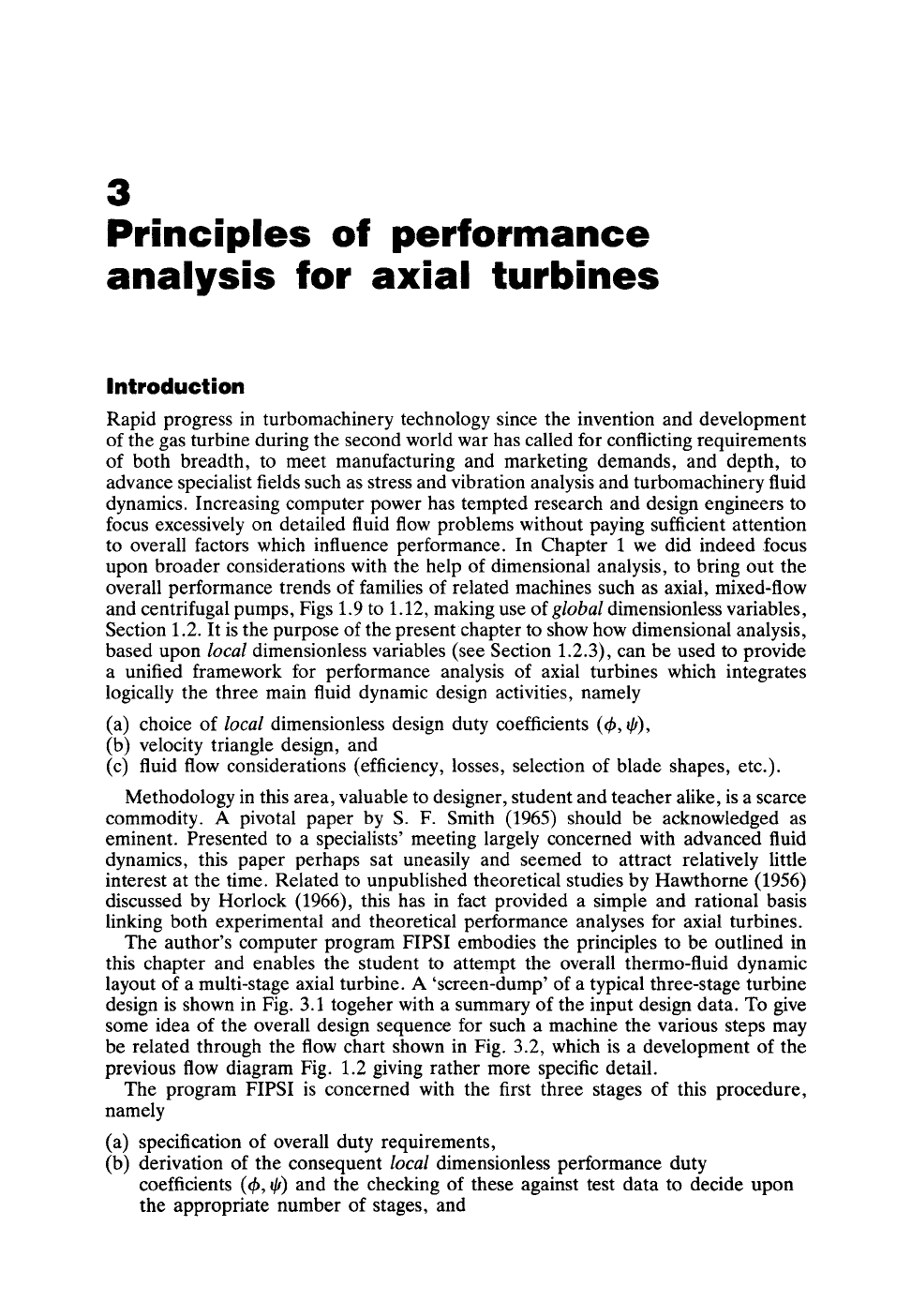
3
Principles of performance
analysis for axial turbines
Introduction
Rapid progress in turbomachinery technology since the invention and development
of the gas turbine during the second world war has called for conflicting requirements
of both breadth, to meet manufacturing and marketing demands, and depth, to
advance specialist fields such as stress and vibration analysis and turbomachinery fluid
dynamics. Increasing computer power has tempted research and design engineers to
focus excessively on detailed fluid flow problems without paying sufficient attention
to overall factors which influence performance. In Chapter 1 we did indeed focus
upon broader considerations with the help of dimensional analysis, to bring out the
overall performance trends of families of related machines such as axial, mixed-flow
and centrifugal pumps, Figs 1.9 to 1.12, making use of global dimensionless variables,
Section 1.2. It is the purpose of the present chapter to show how dimensional analysis,
based upon local dimensionless variables (see Section 1.2.3), can be used to provide
a unified framework for performance analysis of axial turbines which integrates
logically the three main fluid dynamic design activities, namely
(a) choice of local dimensionless design duty coefficients (~b, ~),
(b) velocity triangle design, and
(c) fluid flow considerations (efficiency, losses, selection of blade shapes, etc.).
Methodology in this area, valuable to designer, student and teacher alike, is a scarce
commodity. A pivotal paper by S. F. Smith (1965) should be acknowledged as
eminent. Presented to a specialists' meeting largely concerned with advanced fluid
dynamics, this paper perhaps sat uneasily and seemed to attract relatively little
interest at the time. Related to unpublished theoretical studies by Hawthorne (1956)
discussed by Horlock (1966), this has in fact provided a simple and rational basis
linking both experimental and theoretical performance analyses for axial turbines.
The author's computer program FIPSI embodies the principles to be outlined in
this chapter and enables the student to attempt the overall thermo-fluid dynamic
layout of a multi-stage axial turbine. A 'screen-dump' of a typical three-stage turbine
design is shown in Fig. 3.1 togeher with a summary of the input design data. To give
some idea of the overall design sequence for such a machine the various steps may
be related through the flow chart shown in Fig. 3.2, which is a development of the
previous flow diagram Fig. 1.2 giving rather more specific detail.
The program FIPSI is concerned with the first three stages of this procedure,
namely
(a) specification of overall duty requirements,
(b) derivation of the consequent local dimensionless performance duty
coefficients (~b, ~) and the checking of these against test data to decide upon
the appropriate number of stages, and