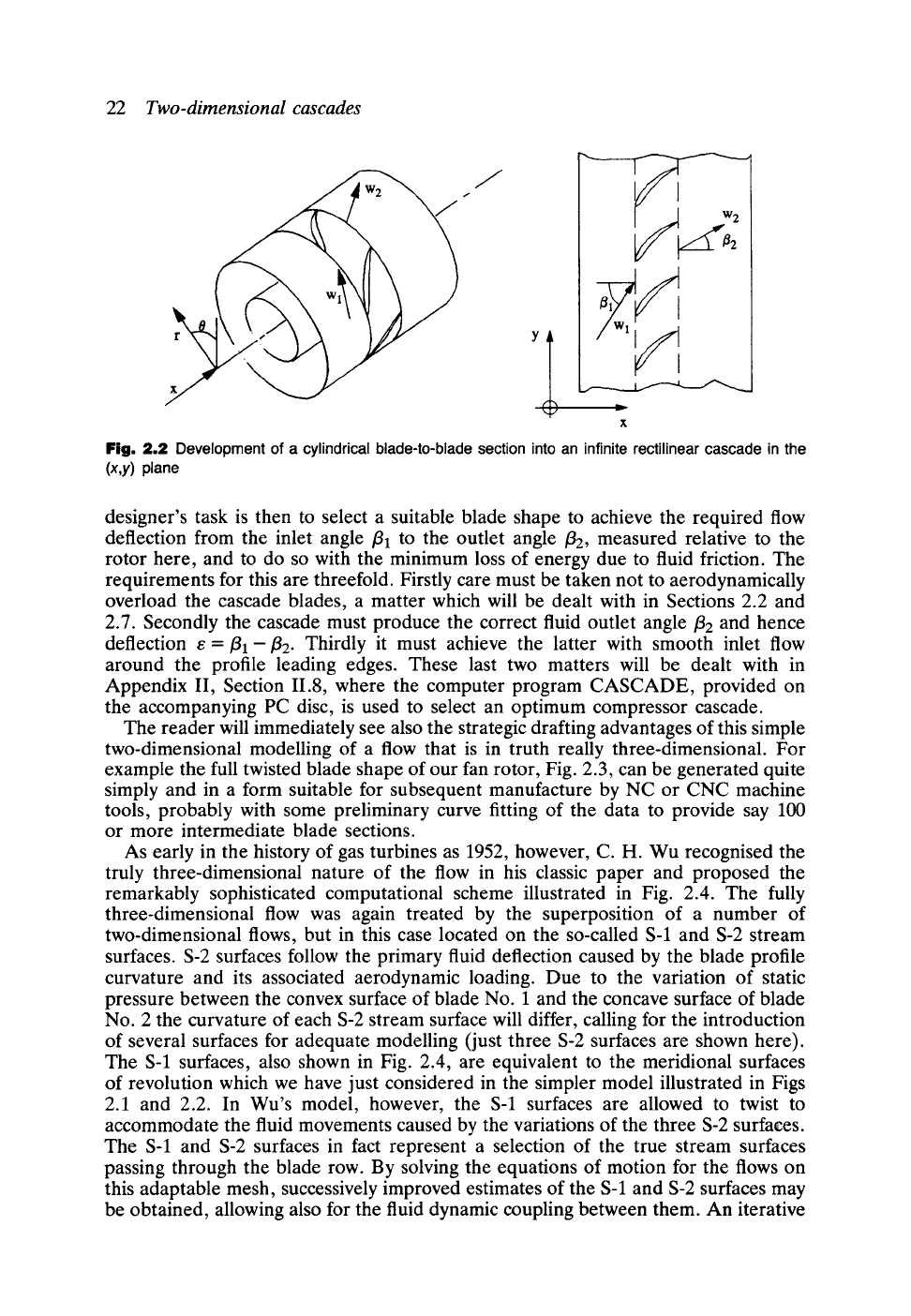
22
Two-dimensional cascades
t I
YI
X
Fig. 2.2 Development of a cylindrical blade-to-blade section
into an infinite
rectilinear cascade
in the
(x,y) plane
designer's task is then to select a suitable blade shape to achieve the required flow
deflection from the inlet angle/31 to the outlet angle/32, measured relative to the
rotor here, and to do so with the minimum loss of energy due to fluid friction. The
requirements for this are threefold. Firstly care must be taken not to aerodynamically
overload the cascade blades, a matter which will be dealt with in Sections 2.2 and
2.7. Secondly the cascade must produce the correct fluid outlet angle/32 and hence
deflection e =/31-/32. Thirdly it must achieve the latter with smooth inlet flow
around the profile leading edges. These last two matters will be dealt with in
Appendix II, Section 11.8, where the computer program CASCADE, provided on
the accompanying PC disc, is used to select an optimum compressor cascade.
The reader will immediately see also the strategic drafting advantages of this simple
two-dimensional modelling of a flow that is in truth really three-dimensional. For
example the full twisted blade shape of our fan rotor, Fig. 2.3, can be generated quite
simply and in a form suitable for subsequent manufacture by NC or CNC machine
tools, probably with some preliminary curve fitting of the data to provide say 100
or more intermediate blade sections.
As early in the history of gas turbines as 1952, however, C. H. Wu recognised the
truly three-dimensional nature of the flow in his classic paper and proposed the
remarkably sophisticated computational scheme illustrated in Fig. 2.4. The fully
three-dimensional flow was again treated by the superposition of a number of
two-dimensional flows, but in this case located on the so-called S-1 and S-2 stream
surfaces. S-2 surfaces follow the primary fluid deflection caused by the blade profile
curvature and its associated aerodynamic loading. Due to the variation of static
pressure between the convex surface of blade No. 1 and the concave surface of blade
No. 2 the curvature of each S-2 stream surface will differ, calling for the introduction
of several surfaces for adequate modelling (just three S-2 surfaces are shown here).
The S-1 surfaces, also shown in Fig. 2.4, are equivalent to the meridional surfaces
of revolution which we have just considered in the simpler model illustrated in Figs
2.1 and 2.2. In Wu's model, however, the S-1 surfaces are allowed to twist to
accommodate the fluid movements caused by the variations of the three S-2 surfaces.
The S-1 and S-2 surfaces in fact represent a selection of the true stream surfaces
passing through the blade row. By solving the equations of motion for the flows on
this adaptable mesh, successively improved estimates of the S-1 and S-2 surfaces may
be obtained, allowing also for the fluid dynamic coupling between them. An iterative