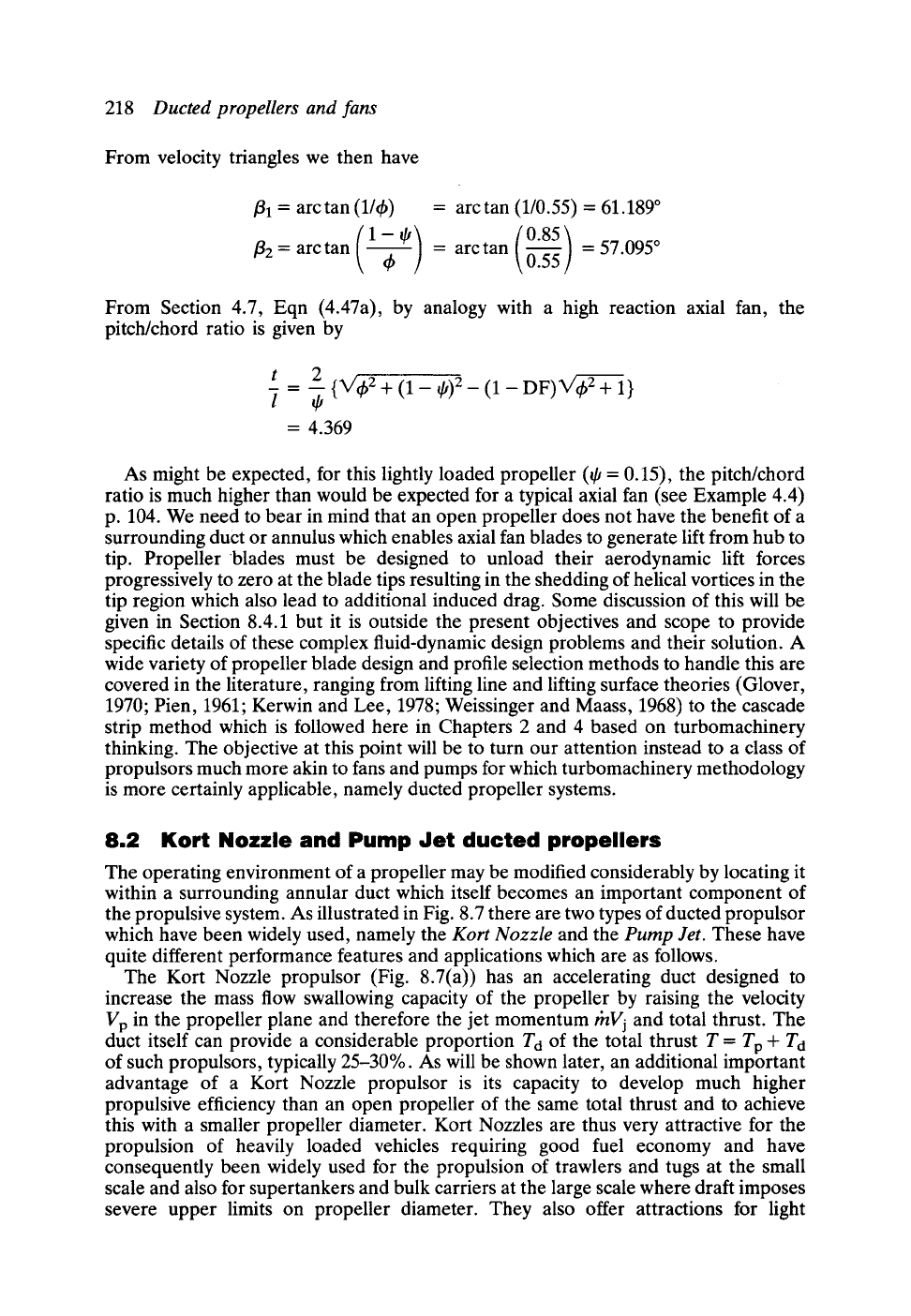
218 Ducted propellers and fans
From velocity triangles we then have
fll --
arc tan (1/4)) = arc tan (1/0.55) = 61.189 ~
o8,)
/32 = arc tan 4) = arc tan \~ = 57.095 ~
From Section 4.7, Eqn (4.47a), by analogy with a high reaction axial fan, the
pitch/chord ratio is given by
_t = 2 {V,b 2 + (1 - @)2_ (1 - DF)V'4~ 2 + 1}
= 4.369
As might be expected, for this lightly loaded propeller (~, = 0.15), the pitch/chord
ratio is much higher than would be expected for a typical axial fan (see Example 4.4)
p. 104. We need to bear in mind that an open propeller does not have the benefit of a
surrounding duct or annulus which enables axial fan blades to generate lift from hub to
tip. Propeller blades must be designed to unload their aerodynamic lift forces
progressively to zero at the blade tips resulting in the shedding of helical vortices in the
tip region which also lead to additional induced drag. Some discussion of this will be
given in Section 8.4.1 but it is outside the present objectives and scope to provide
specific details of these complex fluid-dynamic design problems and their solution. A
wide variety of propeller blade design and profile selection methods to handle this are
covered in the literature, ranging from lifting line and lifting surface theories (Glover,
1970; Pien, 1961; Kerwin and Lee, 1978; Weissinger and Maass, 1968) to the cascade
strip method which is followed here in Chapters 2 and 4 based on turbomachinery
thinking. The objective at this point will be to turn our attention instead to a class of
propulsors much more akin to fans and pumps for which turbomachinery methodology
is more certainly applicable, namely ducted propeller systems.
8.2 Kort Nozzle and Pump Jet ducted propellers
The operating environment of a propeller may be modified considerably by locating it
within a surrounding annular duct which itself becomes an important component of
the propulsive system. As illustrated in Fig. 8.7 there are two types of ducted propulsor
which have been widely used, namely the Kort Nozzle and the Pump Jet. These have
quite different performance features and applications which are as follows.
The Kort Nozzle propulsor (Fig. 8.7(a)) has an accelerating duct designed to
increase the mass flow swallowing capacity of the propeller by raising the velocity
~p
in the propeller plane and therefore the jet momentum rhVj and total thrust. The
uct itself can provide a considerable proportion Td of the total thrust T = Tp + Td
of such propulsors, typically 25-30%. As will be shown later, an additional important
advantage of a Kort Nozzle propulsor is its capacity to develop much higher
propulsive efficiency than an open propeller of the same total thrust and to achieve
this with a smaller propeller diameter. Kort Nozzles are thus very attractive for the
propulsion of heavily loaded vehicles requiring good fuel economy and have
consequently been widely used for the propulsion of trawlers and tugs at the small
scale and also for supertankers and bulk carriers at the large scale where draft imposes
severe upper limits on propeller diameter. They also offer attractions for light