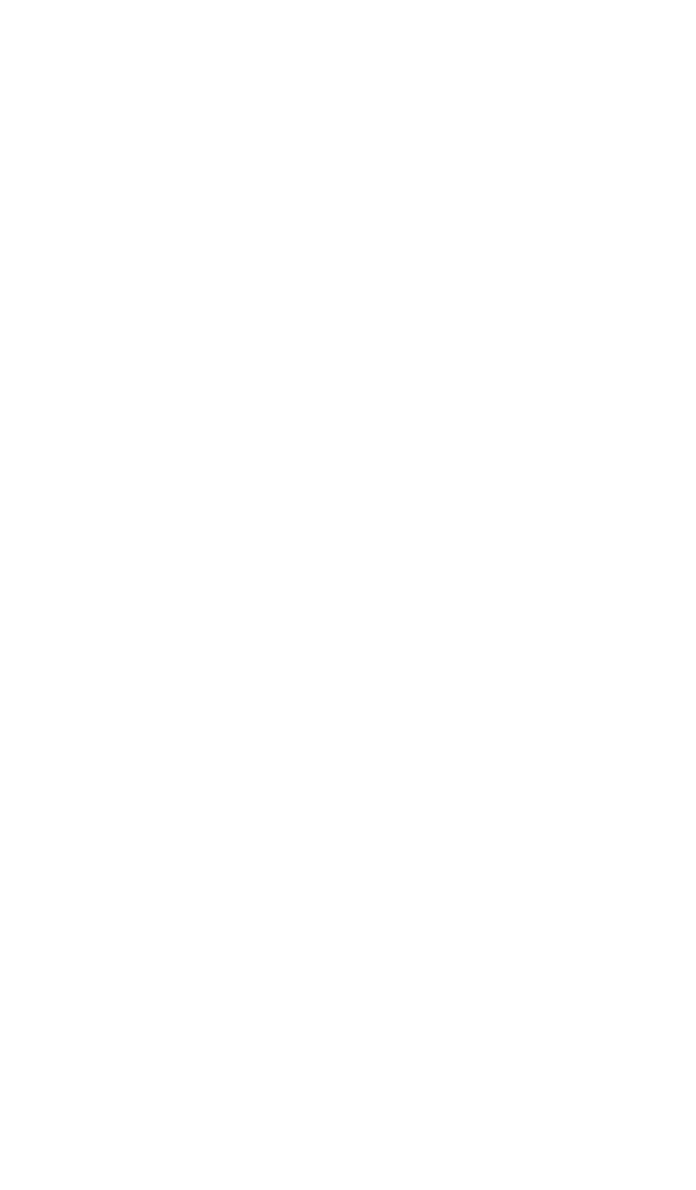
2 THERMAL PROPERTIES 571
oil at which the bar has deflected 0.010 in. is recorded as the heat deflection
temperature at the specified fiber stress.
Long-Term Effects
The long-term effects of elevated temperature on properties of plastics are ex-
tremely important, especially when one considers the fact that the majority of
applications involving high heat are long-term applications. During long-term
exposure to heat, plastic materials may encounter many physical and chemical
changes. A plastic material that shows little or no effect at elevated temperature
for a short time may show a drastic reduction in physical properties, a complete
loss of rigidity, and severe thermal degradation when exposed to elevated tem-
perature for a long time. Along with time and temperature, many other factors
such as ozone, oxygen, sunlight, and pollution combine to accelerate the attack
on plastics. At elevated temperatures, many plastics tend to lose important ad-
ditives such as plasticizers and stabilizers, causing plastics to become brittle or
soft and sticky.
Three basic tests have been developed and accepted by the plastics industry.
If the application does not require the product to be exposed to elevated tem-
perature for a long period under continuous load, a simple heat resistance test
is adequate. The applications requiring the product to be under continuous sig-
nificant load must be looked at from creep modulus and creep rupture strength
test data. Another one of the most widely accepted methods of measuring max-
imum continuous use temperature has been developed by Underwriters Labo-
ratories. The UL temperature index, established for a variety of plastic materials
to be used in electrical applications, is the maximum temperature that the ma-
terial may be subjected to without fear of premature thermal degradation.
Long-Term Heat Resistance Test (ASTM D794). The long-term heat resis-
tance test was developed to determine the permanent effect of heat on any prop-
erty by selection of an appropriate test method and specimen. In ASTM
recommended practice, only the procedure for heat exposure is specified and not
the test method or specimen.
Any specimen, including sheet, laminate, test bar, or molded part may be
used. If a specific property, such as tensile strength loss is to be determined, a
standard tensile test bar specimen and procedures must be used for comparison
of test results before and after the test. The test requires the use of a mechanical
convection oven with a specimen rack of suitable design to allow air circulation
around the specimens. The test is carried out by simply placing the specimen in
the oven at a desired exposure temperature for a predetermined length of time.
The subsequent exposure to temperatures may be increased or decreased in steps
of 25
⬚C until a failure is observed. Failure due to heat is defined as a change in
appearance, weight, dimension, or other properties that alter plastic material to
a degree that it is no longer acceptable for the service in question. Failure may
result from blistering, cracking, loss of plasticizer, or other volatile material that
may cause embrittlement, shrinkage, or change in desirable electrical or me-
chanical properties.
Many factors that affect the reproducibility of the data. The degree of tem-
perature control in the oven, the type of molding, cure, air velocity over the