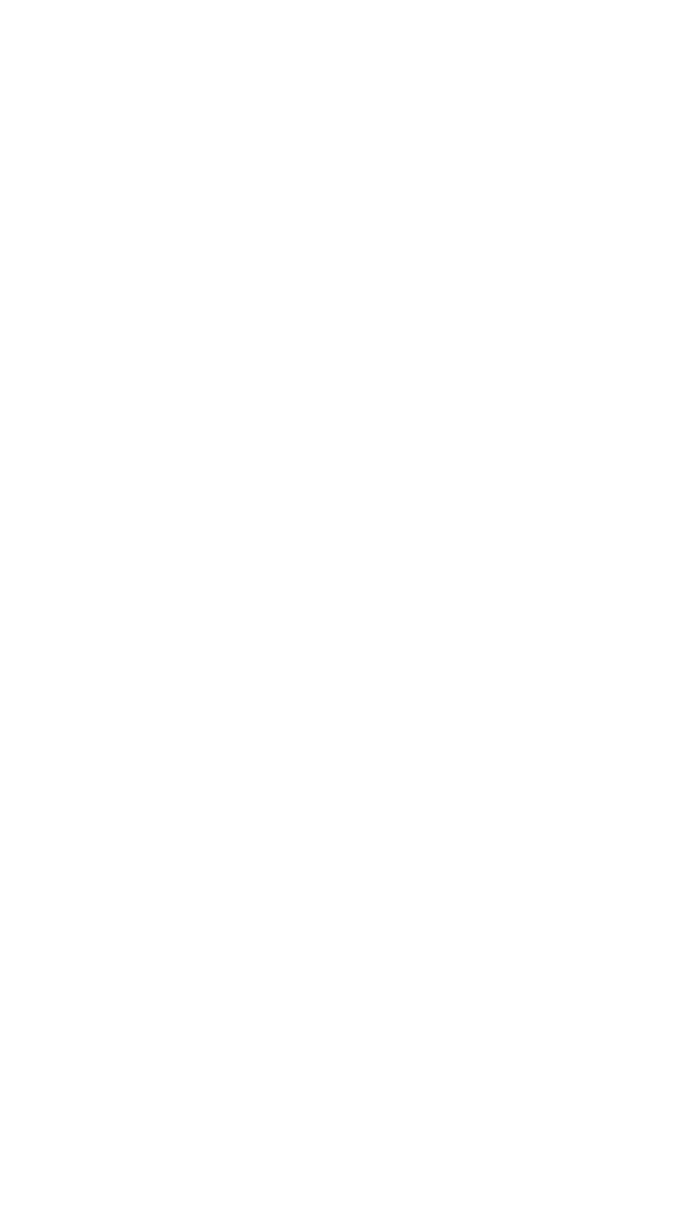
578 PLASTICS TESTING
between them that is distributed through the volume of the specimen. Or, simply
stated, the volume resistance is the resistance to leakage through the body of
the material. Volume resistance generally depends upon the material. The term
most commonly used by designers is volume resistivity. It is defined as the ratio
of the potential gradient parallel to the current in the material to the current
density or, simply stated, the volume resistivity of a material is the electrical
resistance between the opposite faces of a unit cube for a given material and at
a given temperature.
High-volume resistivity materials are desirable in applications requiring su-
perior insulating characteristics.
The surface resistance of a material is defined as the ratio of the direct voltage
applied to the electrodes to that portion of the current between them that is
primarily in a thin layer of moisture or other semiconducting material that may
be deposited on the surface. Simply stated, surface resistance is the resistance
to leakage along the surface of an insulator. The surface resistance of a material
depends upon the quality and cleanliness of the surface of the product. A product
with oil or dirt particles on it gives lower surface resistance values.
The test procedures to determine electrical resistance values are rather com-
plex. ASTM D257 (IEC 93) describes the procedures as well as the complex
electrodes and apparatus required to carry out the test in detail.
Temperature and humidity both seem to affect the insulation resistance ap-
preciably. As a rule, the higher the temperature and humidity, the lower the
insulation resistance of a material.
3.4 Arc Resistance (ASTM D495)
Arc resistance is the ability of a plastic material to resist the action of a high-
voltage electrical arc, usually stated in terms of time required to form material
electrically conductive. Failure is characterized by carbonization of the surface,
tracking, localized heating to incandescence, or burning. In all applications in
which conducting elements are brought into contact, arcing is inevitable.
Switches, circuit breakers, and automotive distributor caps are a few good ex-
amples of applications where arcing is known to cause failure. Another term
that is generally associated with arcing is tracking. Tracking is defined as a
phenomenon where a high-voltage source current creates a leakage or fault path
across the surface of an insulating material by slowly but steadily forming a
carbonized path appearing as a thin, wiry line between the electrodes. Tracking
is accelerated by the presence of surface contaminants such as dirt and oil and
by the presence of moisture. Resistance to arcing or tracking depends upon the
type of plastic materials such as phenolics that tend to carbonize easily and
therefore have relatively poor arc resistance. Plastics such as alkyds, melamines,
and fluorocarbons are excellent arc-resistant materials. The failures due to arcing
are not always because of carbonization or tracking. Many plastics such as acryl-
ics simply do not carbonize. However, they do form ignitable gases that cause
the product to fail in a short time. Arc resistance of plastics can be improved
substantially by the addition of fillers such as glass, mineral, wood flour, asbes-
tos, and other inorganic fillers. Table 3 lists the arc resistance of some common
plastic materials.
The determination of the arc resistance of plastics using a standard test
method has always been a problem because of the numerous ways the test can