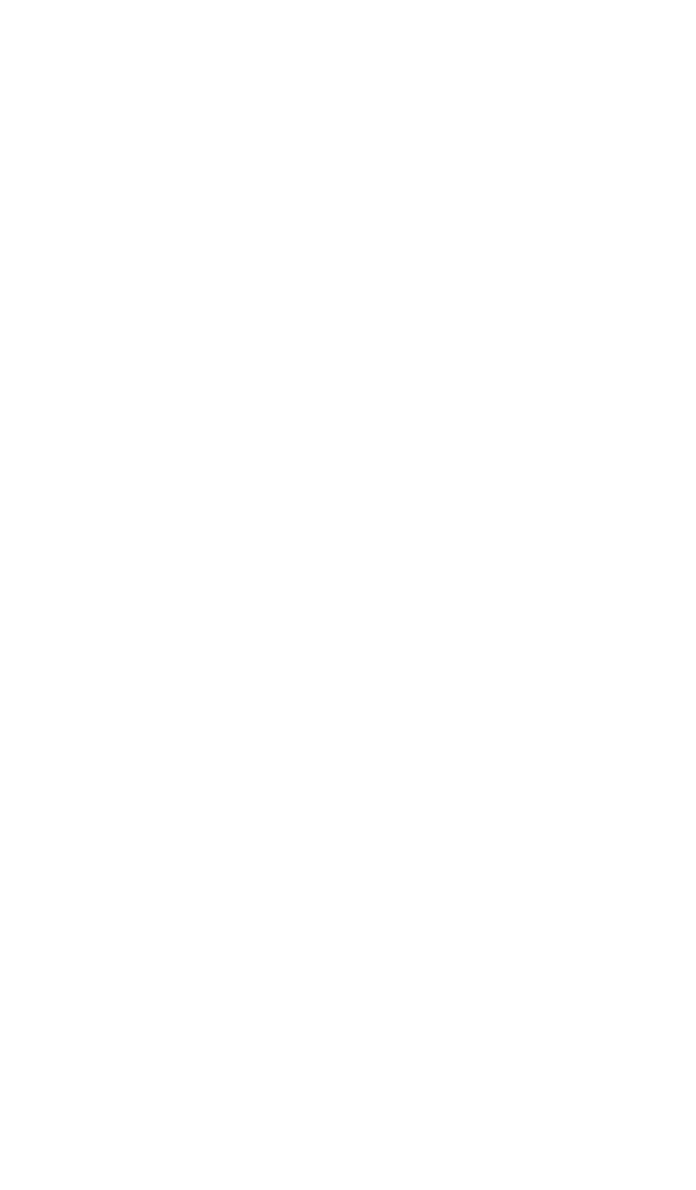
560 PLASTICS TESTING
support, and a sample platform. The sample platform is used to position a sheet
of desired thickness for impact testing. The die is removable from the base in
order that the actual parts of complex shapes can be placed onto the base and
impact tested.
The test is carried out by raising the weight to a desired height manually or
automatically with the use of a motor-driven mechanism and allowing it to fall
freely onto the other side of the striker. The striker transfers the impact energy
to the flat test specimen positioned on a cylindrical die or a part lying on the
base of the machine. The kinetic energy possessed by the falling weight at the
instant of impact is equal to the energy used to raise the weight to the height
of the drop and is the potential energy possessed by the weight as it is released.
Since the potential energy is expressed as the product of weight and height, the
guide tube can be marked with a linear scale representing the impact range of
the instrument in in.-lb. Thus, the toughness or the impact resistance of a spec-
imen or a part can be read directly off the calibrated scale in in.-lb. The energy
loss due to the friction in the tube or due to the momentary acceleration of the
punch is negligible.
An alternate method for achieving the same result utilizes an instrument that
employs a free-falling dart dropped from a specified height onto a test specimen.
The dart with a hemispherical head is constructed of smooth, polished aluminum
or stainless steel. An electromagnetic, air-operated or other mechanical release
mechanism with a centering device is used for releasing the dart. The dart is
also fitted with a shaft long enough to accommodate removable incremental
weights. A two-piece annular specimen clamp is used to hold the specimen.
Instrumented Impact Testing. One of the biggest drawbacks of the conven-
tional impact test methods is that it provides only one value—the total impact
energy—and nothing else. The conventional tests cannot provide additional in-
formation on the ductility, dynamic toughness, fracture, and yield loads or the
behavior of the specimen during the entire impact event.
This effectively limits the application of noninstrumented impact test methods
to quality control and material ranking. Instrumented impact testers are generally
suited for research and development as well as advance quality control.
Instrumented impact testers measure force continuously while the specimen
is penetrated. The resulting data can be used to determine type of failure and
maximum load, in addition to the amount of energy required to fracture the
specimen. One of the most common type of failures occurring from ductile to
brittle transition at low temperatures can only be observed by studying the load–
energy–time curve. The fracture mode of a plastic is sensitive to the changes in
temperature, and can change abruptly at or near the materials transition temper-
ature. Manufacturers of plastic automotive components routinely test materials
at low temperatures (
⫺20 to ⫺40⬚F) to assure that they will not become brittle
in cold weather. By studying the shape of the load–time or load–deflection
curve, the type of failure can be analyzed, and important information about its
performance in service can be gathered. The new piezoelectric-equipped strikers
offer increased sensitivity, opening the doors for testing a whole new range of
materials. Applications involving light-weight products such as foam containers
for eggs and ultra-thin films used in packaging industry can now be meaningfully
tested.