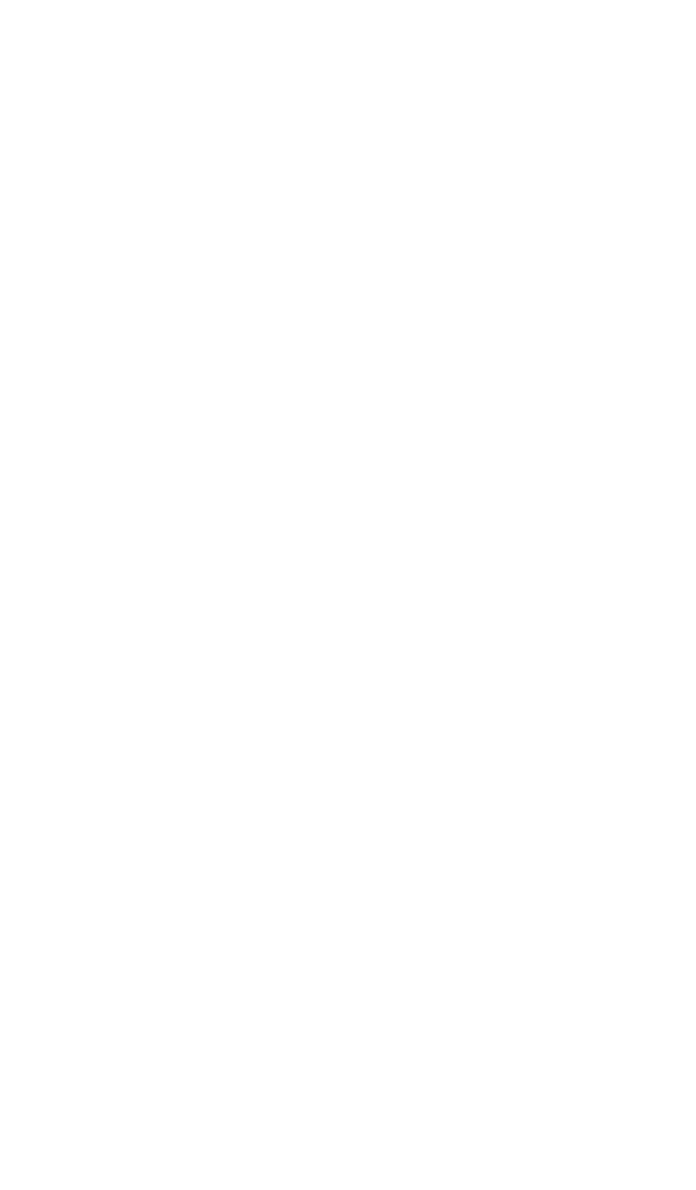
536 TESTING OF METALLIC MATERIALS
section the process of crack nucleation (e.g., crack initiation) and stable propa-
gation (e.g., crack growth) under cyclic loading is addressed. Understanding
crack propagation behavior is critically important since some structures, most
notably the current fleet of commercial airliners, adopt a damage tolerance de-
sign philosophy whereby cracks are assumed in the structure, and a safe struc-
tural life requires detecting and managing these cracks. Quantifying crack
nucleation is also important since much of a crack’s cyclic life is spent initiating
or growing when it is small in size.
The test specimens used for fatigue crack initiation testing are similar geo-
metrically to tensile specimens. The two basic test methods for initiation testing
are ASTM E606 and E466 for strain- and stress-controlled testing, respectively.
With both of these methods, the goal is to cycle a specimen until failure occurs.
Strain control is typically used if (a) the loading is with a constant displacement
or (b) the focus is on the short life regime (estimated to be less than 10
3
to 10
5
cycles although this is fairly controversial) where applied stress levels often
approach the yield strength of the metallic material. Conversely load control
testing is performed for the mid- to high-cycle life regime. Stress (effectively
load) control testing is relatively straightforward since no displacement moni-
toring or measurement is required. The specimen can be gripped, cycling can
commence, and continue unmonitored (provided the servocontrol loop does not
require any attention) until failure occurs.
One of the most critical details when performing this type of fatigue testing
is controlling bending in the specimen. Poor control of bending typically in-
creases the apparent scatter in the fatigue data generated. Commercial alignment
fixtures are available to mitigate bending. These fixtures utilize a strain gauged
specimen and a fixture that allows minute adjustments of the loading train. How-
ever, these fixtures are not always available, which means less high tech and
pragmatic methods are often required to minimize the effect.
Although guidelines on how to measure and verify specimen alignment are
provided in ASTM E1012, minimizing bending practically requires control of
three issues. First, the specimen must be carefully machined with excellent di-
mensional control, parallelism, and axisymmetry. Second, the fixtures used to
connect the specimen to the loading train must not introduce any asymmetry.
Threaded specimen ends, although commonly employed during fatigue testing,
should be avoided as the tolerances required to engage the thread make accurate
alignment problematic (however, it must be stated that it is not always practical
or possible to avoid threaded ends). If the loading cycle is tensile only (e.g., a
positive R ratio where R is the ratio of minimum to maximum load), a spherical
joint, or more commonly known as a U-joint, in the loading train can minimize
bending. Third, the fixtures in the load train should be designed well enough to
grip repeatably in the same manner so that once a load train has been carefully
aligned with an instrumented specimen it does not vary.
Some typical stress–life (S–N) data are shown in Fig. 14 for two materials,
an aluminum and titanium alloy. S–N data are usually generated at a fixed R
ratio with the results represented as a plot with stress amplitude or maximum
stress on the abscissa and cyclic life on the ordinate. Data are sometimes gen-
erated on specimens that have a groove or hole to simulate stress concentrations
typically found in structure. Furthermore, it is often of practical interest to know