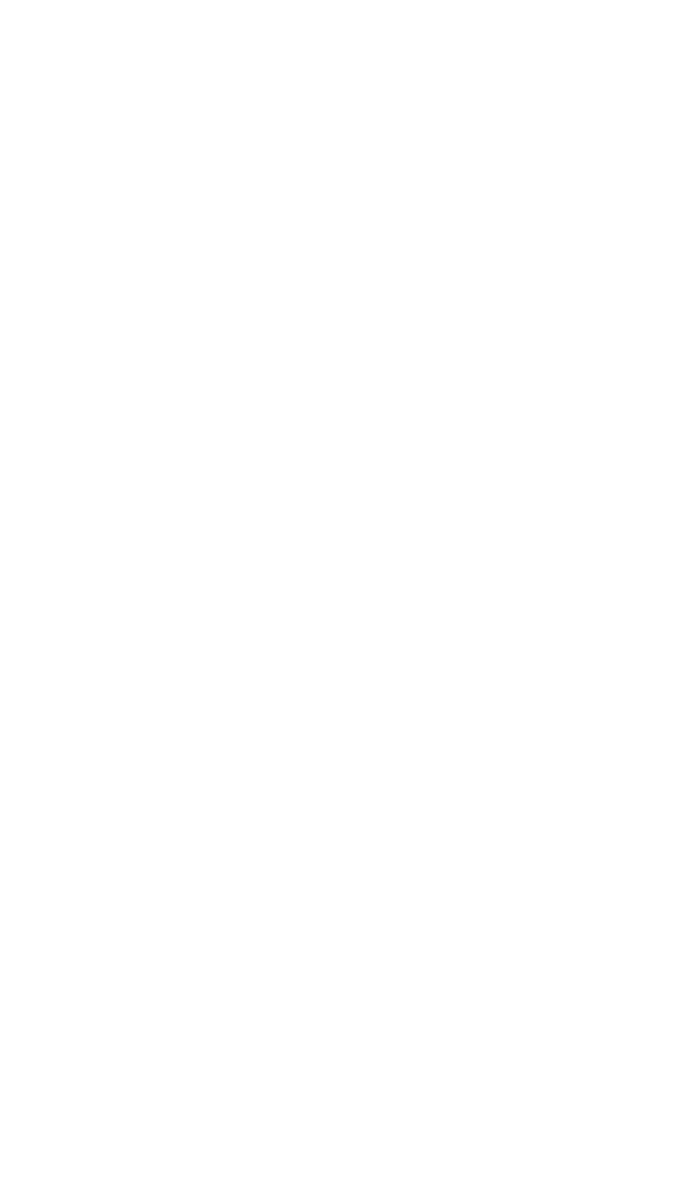
90 ALUMINUM ALLOYS
●
Aluminum Standards & Data (Standard and Metric Editions), The Alu-
minum Association, Inc., Washington, DC, published periodically
●
The Aluminum Design Manual, The Aluminum Association, Inc., Wash-
ington, DC, 2000.
See the list of references at the end of the chapter for a more complete listing.
1.1 Advantages of Wrought Aluminum Alloys
1. Corrosion Resistance. As a result of a naturally occurring tenacious sur-
face oxide film, many aluminum alloys provide exceptional resistance to cor-
rosion in many atmosphere and chemical environments. Alloys of the 1xxx,
3xxx, 5xxx, and 6xxx systems are especially favorable in this respect and are
even used in applications where they are in direct contact with seawater and
antiskid salts. With some electrocoating enhancements (e.g., anodizing), the ox-
ide coating can be thickened for even greater protection.
2. Thermal Conductivity. Aluminum and its alloys are good conductors of
heat, and, while they melt at lower temperatures than steels, about 1000
⬚F (about
535
⬚C), they are slower to reach very high temperatures than steel in fire ex-
posure.
3. Electrical Conductivity. Pure aluminum and some of its alloys have ex-
ceptionally high electric conductivity (i.e., very low electrical resistivity), second
only to copper among common metals as conductors.
4. Strength /Weight Ratio. The combination of relatively high strength with
low density means a high strength efficiency for aluminum alloys and many
opportunities for replacement of heavier metals with no loss (and perhaps a gain)
in load-carrying capacity. This characteristic, combined with the excellent cor-
rosion resistance and recyclability, has led to aluminum’s broad use in contain-
ers, aircraft, and automotive applications.
5. Fracture Toughness and Energy Absorption Capacity. Many aluminum
alloys are exceptionally tough and excellent choices for critical applications
where resistance to brittle fracture and unstable crack growth are imperatives.
Alloys of the 5xxx series, for example, are prime choices for liquified natural
gas (LNG) tankage. And special high-toughness versions of aircraft alloys, such
as 2124, 7050, and 7475, replace the standard versions of these alloys for critical
bulkhead applications.
6. Cryogenic Toughness. Aluminum alloys, especially of the 3xxx, 5xxx,
and 6xxx series, are ideal for very low temperature applications because the
ductility and toughness as well as strength of many alloys at subzero tempera-
tures are as high as or higher than at room temperature, even down to near
absolute zero.
7. Fatigue Strength. On an efficiency basis (strength to density) the fatigue
strengths of many aluminum alloys are comparable to those of steels.
8. Modulus of Elasticity. Aluminum alloys have elastic moduli about one
third those of steels (about 10,000,000 psi vs. about 30,000,000 psi), so they
absorb about three times as much elastic energy upon deformation to the same
stress. They also deflect three times more under load (see Section 1.3).
9. Workability. Aluminum alloys are readily workable by a great variety of
metal-working technologies and especially amenable to extrusion (the process