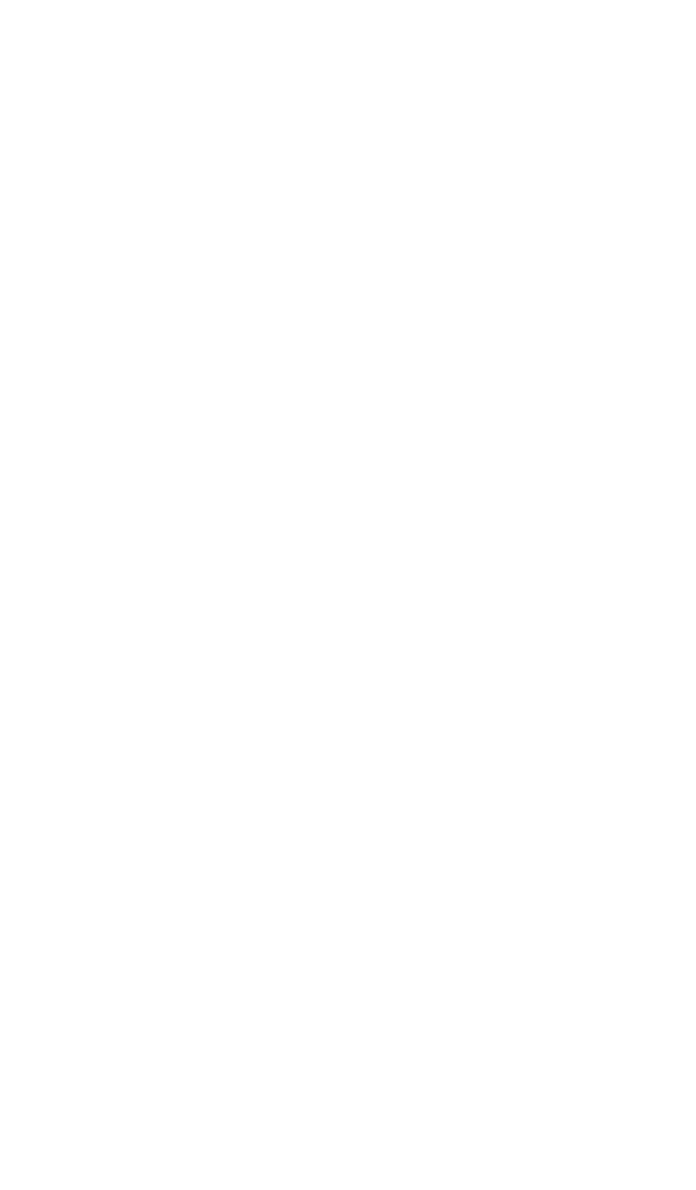
84 STAINLESS STEELS
Pulse-arc welding is usually done with a 75% argon 25% helium mix. Short-
circuiting arc transfer may be done with this 75% Ar–25% He mix but a 90%
helium 7 argon 2 CO
2
‘‘tri-mix’’ is more commonly used.
11
––
%%
22
3. Cold Cracking versus Hot Cracking. Carbon steel weldments may harden,
and crack, as they cool from welding. High hardness, and the resulting cracking,
may occur when the steel contains more than 0.25% carbon. Alloying elements
that increase hardenability, such as manganese, chromium, molybdenum, etc.,
can make steels of lower carbon content also harden. Hydrogen pickup from
moisture in the air causes underbead cracking in steels that harden as they cool
from welding. To prevent such cracking, the steel is usually preheated before
welding. This retards the cooling rate of the weld and avoids martensite for-
mation. Postweld heat treatment, or stress relief, is also applied to some steels,
or for certain applications. The martensitic stainless steels behave in this fashion
and because of their high hardenability are quite difficult to weld.
Austenitic stainless and nickel alloys do NOT harden, no matter how fast they
cool from welding. So, it is not necessary to preheat austenitic stainless, nor to
postweld heat treatment. Indeed preheating austenitic alloys, beyond what may
be necessary to dry the metal, can be positively harmful. Stress relief 1100–
1200
⬚F (600–650⬚C) as applied to carbon steel is ineffective with stainless or
nickel alloys and may damage the corrosion resistance of some grades.
Stainless steel weldments are usually quite resistant to cracking, unless con-
taminated, possibly by zinc or copper, more rarely by aluminum. A small amount
of ferrite in the austenitic weld bead provides this hot cracking resistance.
High-nickel alloys are less forgiving and may be susceptible to cracking in
restrained joints, including heavy sections. This is a hot tearing, not a cold crack.
That is, the weld bead tears rather than stretching, as the bead contracts upon
solidifying.
This hot tearing/hot cracking has nothing to do with hardness. The faster a
nickel alloy weld freezes solid, the less time it spends in the temperature range
where it can tear. For this reason preheating, which slows down the cooling rate,
is actually harmful, as it permits more opportunity for hot tearing to occur.
4. Distortion. Stainless steel has poor thermal conductivity, only about one
fourth that of ASTM A36 structural steel. This means the welding heat tends to
remain concentrated, rather than spread out. Stainless also expands with heat
about half again as much as does carbon steel. The combination of these two
factors means that stainless or nickel alloy fabrications distort significantly more
than similar designs in carbon steel.
Tack welds should be closer than with carbon steel and sequenced in a pattern,
left side, right side, middle, etc. If the tacks are simply done in order from one
end, the plate edges close up. To balance stresses, weld runs should be done
symmetrically about the joint’s center of gravity. Back step welding is helpful.
This subject is well covered in Refs. 9 and 10.
Reducing heat input reduces the stresses and distortions from the welding
operation. Heat into the workpiece is controlled by welding current, arc voltage,
travel speed, and the specific welding process used. For the same amperes, volts
and speed, submerged arc welding (SAW) transfers the most heat; shielded metal
arc (SMAW), and gas–metal arc (GMAW) with argon shielding next and roughly