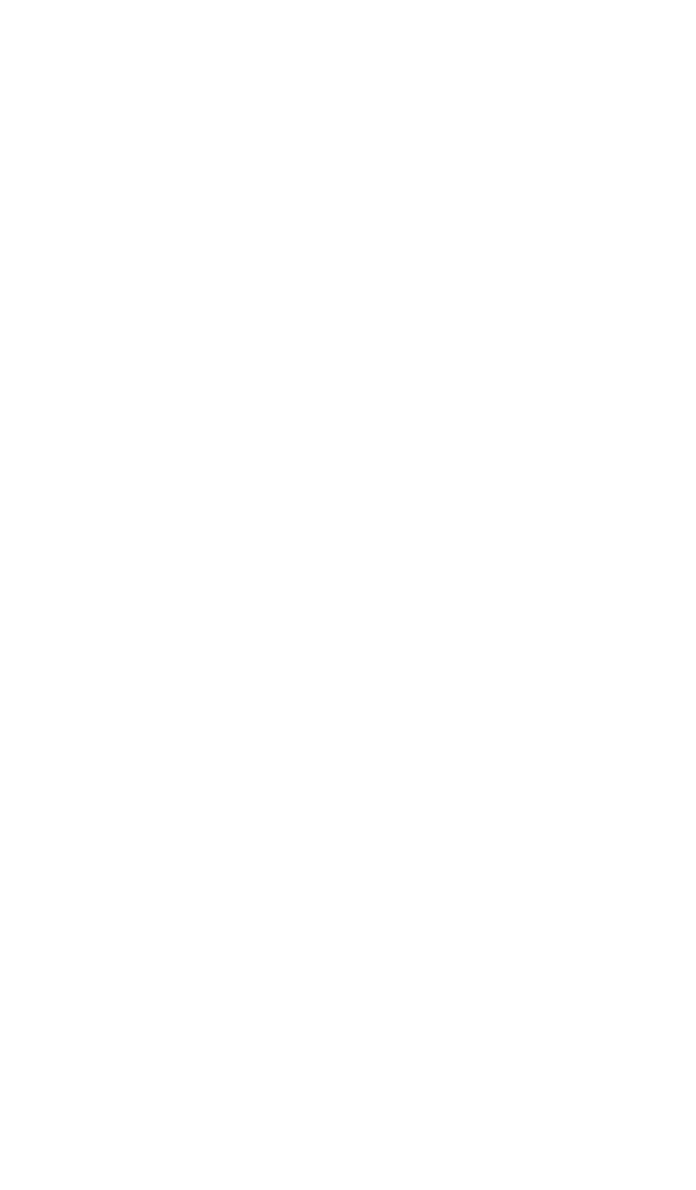
70 STAINLESS STEELS
ranging from oxidizing to reducing. This includes seawater, organic and many
inorganic acids, though not halogen acids. Lack of strength and ductility limit
the cast iron’s range of use.
When one speaks about the effect of this or that pure chemical on an alloy,
one must emphasize that real industrial environments are complex mixtures of
chemicals. These mixtures may behave in surprising ways; quite unlike what
one might expect from the behavior of alloys in pure, laboratory-controlled en-
vironments. Corrosion rates depend not only upon the concentrations of various
chemicals but also on the temperature. The temperature of liquid inside a vessel
is one point that can be measured, but the temperature at the surface of sub-
merged heating coils in that vessel is another, and higher value. Likewise the
concentration of, say an acid, in the vessel is not the same as the concentration
at the point where that acid is introduced to the mixture.
The most commonly used corrosion-resistant alloys are the stainless steels
304 (18% Cr 8% Ni, commonly known as 18–8 stainless) and 316 (17% chro-
mium 11% nickel 2% molybdenum). The more corrosion-resistant nickel alloys,
such as C-276, have much higher levels of nickel, 57%, and molybdenum,
15.5%. Commercially pure nickel, and nickel–copper alloys are used for special
environments.
Oxidizing and reducing environments are defined chemically with respect to
whether hydrogen is oxidized or reduced under the environment in question. In
an oxidizing environment, hydrogen will only be present chemically combined
with some other element, for example, with oxygen to form H
2
O. In a reducing
environment, that H
⫹
will be reduced to hydrogen gas, H
2
.
Common oxidizing chemicals are nitric acid, HNO
3
, and certain salts such as
ferric chloride, FeCl
3
, and cupric chloride, CuCl
2
. The ferric and cupric ions are
at a relatively high valences,
⫹3 and ⫹2, respectively, and readily accept elec-
trons, or oxidize, other materials, to get their own valences reduced to a more
stable level. Sulfuric acid, H
2
SO
4
, is normally a reducing acid. At high concen-
trations, above about 95%, sulfuric acid changes its character and becomes an
oxidizing acid. Of course, dissolved oxygen contributes to the oxidizing char-
acter of an environment. To some extent so does dissolved elemental sulfur.
To resist oxidizing conditions an alloy must contain some amount of chro-
mium. For oxidizing acid service simple materials such as 304 (18% Cr 8% Ni)
or 310 (25% Cr 20% Ni) are often used. An unusually high level of chromium,
33%, is present in a newly developed alloy, UNS R20033, meant to resist very
oxidizing acids. In any of these alloys the nickel content is necessary to make
a stable austenitic alloy, but it does not contribute specifically to oxidizing acid
resistance. Small additions of molybdenum or copper may be tolerated in these
alloys to enhance resistance to chlorides or sulfuric acid. But neither Mo nor
Cu themselves are helpful in resisting strongly oxidizing chemicals.
A common, and severe, test for resistance to oxidizing acids is boiling 65%
nitric acid. The test is run for five periods of 48 h each, specimens being weighed
after each test period, and the results averaged. This test is a good measure of
resistance to intergranular corrosion in a sensitized alloy, as well as to general
corrosion in nitric acid. Test results
2
show 2205 0.13–0.20 mm/yr, which is
good, 304 0.23 mm/yr, and RA333
威, which has been stabilize annealed 1700⬚F,
at 0.29 mm/yr. In the case of RA333 it is the high chromium that helps, in spite