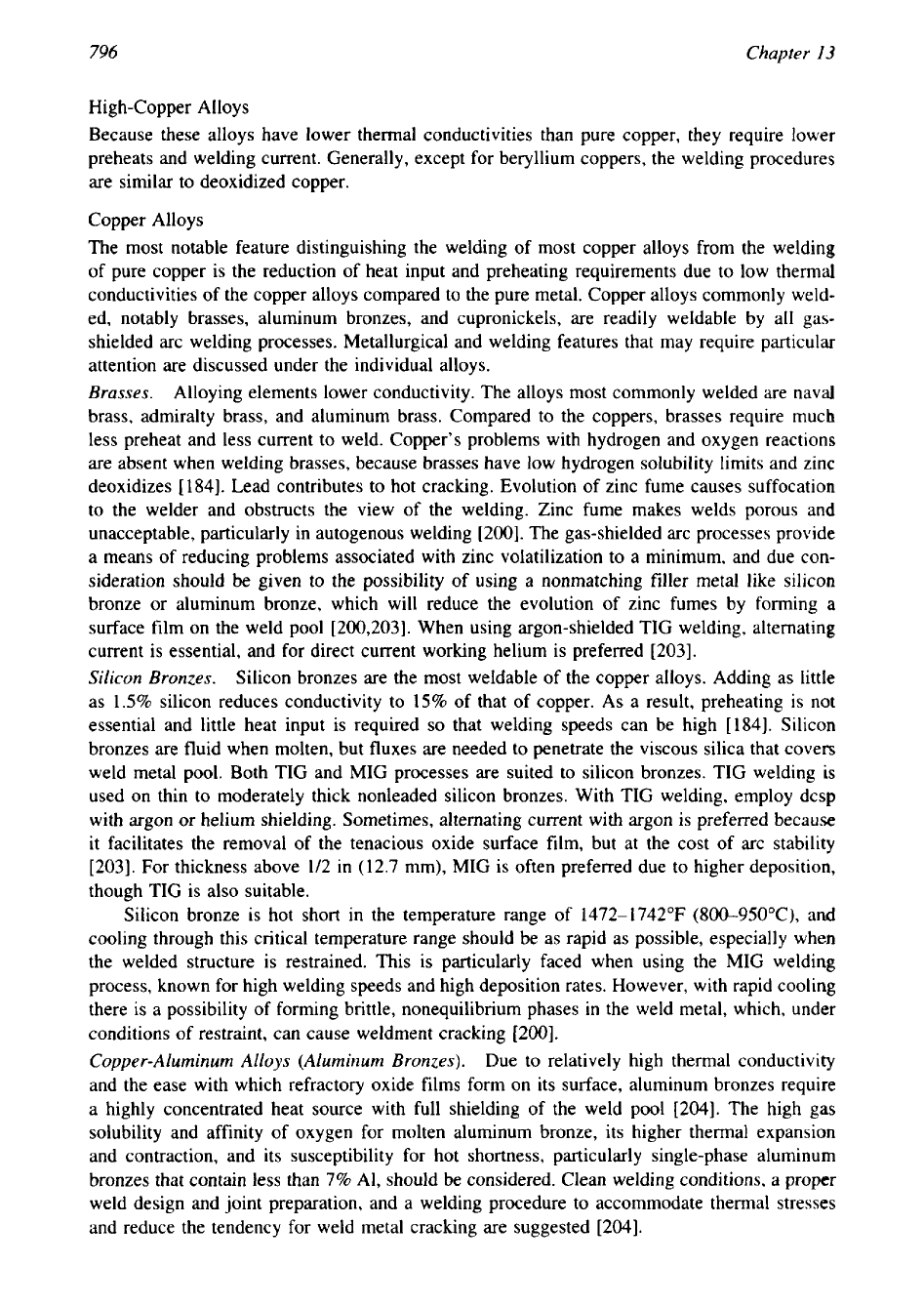
796
Chapter
I3
High-Copper Alloys
Because these alloys have lower thermal conductivities than pure copper, they require lower
preheats and welding current. Generally, except for beryllium coppers, the welding procedures
are similar to deoxidized copper.
Copper Alloys
The most notable feature distinguishing the welding of most copper alloys from the welding
of pure copper is the reduction of heat input and preheating requirements due to low thermal
conductivities of the copper alloys compared to the pure metal. Copper alloys commonly weld-
ed, notably brasses, aluminum bronzes, and cupronickels, are readily weldable by all gas-
shielded arc welding processes. Metallurgical and welding features that may require particular
attention are discussed under the individual alloys.
Brasses.
Alloying elements lower conductivity. The alloys most commonly welded are naval
brass, admiralty brass, and aluminum brass. Compared to the coppers, brasses require much
less preheat and less current to weld. Copper’s problems with hydrogen and oxygen reactions
are absent when welding brasses, because brasses have low hydrogen solubility limits and zinc
deoxidizes
[
1841. Lead contributes to hot cracking. Evolution of zinc fume causes suffocation
to the welder and obstructs the view of the welding. Zinc fume makes welds porous and
unacceptable, particularly in autogenous welding [200]. The gas-shielded arc processes provide
a means of reducing problems associated with zinc volatilization to a minimum, and due con-
sideration should be given to the possibility of using a nonmatching filler metal like silicon
bronze or aluminum bronze, which will reduce the evolution of zinc fumes by forming
a
surface film on the weld pool [200,203]. When using argon-shielded TIG welding, alternating
current is essential, and for direct current working helium is preferred [203].
Silicon
Bronzes.
Silicon bronzes are the most weldable of the copper alloys. Adding as little
as 1.5% silicon reduces conductivity to 15% of that of copper. As a result, preheating is not
essential and little heat input is required
so
that welding speeds can be high
[
1841. Silicon
bronzes are fluid when molten, but fluxes are needed to penetrate the viscous silica that covers
weld metal pool. Both TIG and MIG processes are suited to silicon bronzes. TIG welding
is
used on thin
to
moderately thick nonleaded silicon bronzes. With TIG welding, employ dcsp
with argon or helium shielding. Sometimes, alternating current with argon is preferred because
it facilitates the removal of the tenacious oxide surface film, but at the cost of arc stability
[203]. For thickness above 1/2 in (12.7 nim), MIG is often preferred due to higher deposition,
though TIG is also suitable.
Silicon bronze is hot short in the temperature range
of
1472-1742°F (80O-95O0C), and
cooling through this critical temperature range should be as rapid as possible, especially when
the welded structure is restrained. This is particularly faced when using the MIG welding
process, known for high welding speeds and high deposition rates. However, with rapid cooling
there is a possibility of forming brittle, nonequilibrium phases in the weld metal, which, under
conditions of restraint, can cause weldment cracking [200].
Copper-Aluminum Alloys (Alumirzum
Bronzes).
Due to relatively high thermal conductivity
and the ease with which refractory oxide films form on its surface, aluminum bronzes require
a highly concentrated heat source with full shielding of the weld pool [204]. The high gas
solubility and affinity of oxygen for molten aluminum bronze, its higher thermal expansion
and contraction, and its susceptibility for hot shortness, particularly single-phase aluminum
bronzes that contain less than 7% Al, should be considered. Clean welding conditions, a proper
weld design and joint preparation, and a welding procedure to accommodate thermal stresses
and reduce the tendency for weld metal cracking are suggested [204].