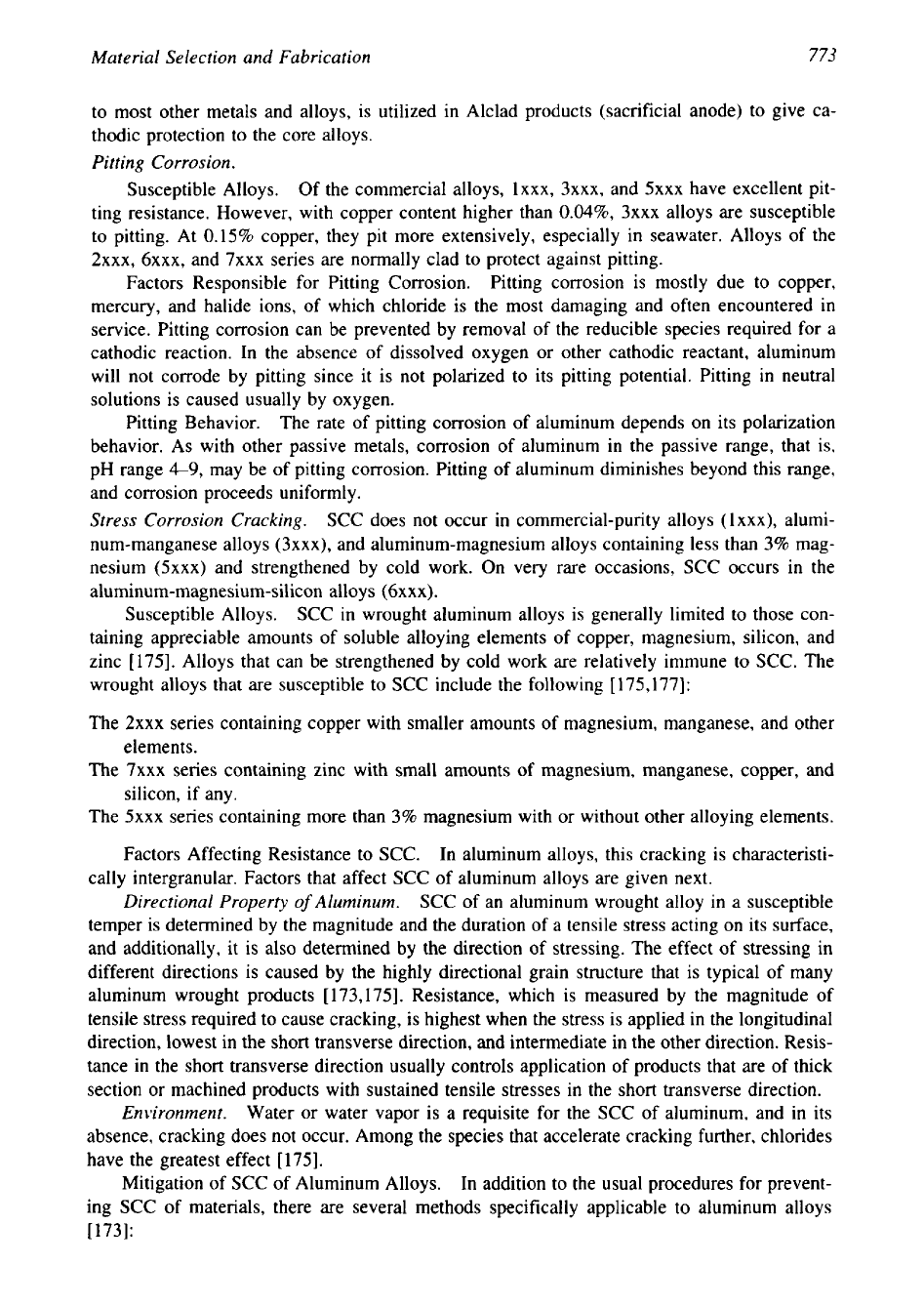
773
Material Selection and Fabrication
to most other metals and alloys, is utilized in Alclad products (sacrificial anode) to give ca-
thodic protection to the core alloys.
Pitting Corrosion.
Susceptible Alloys.
Of the commercial alloys, lxxx,
~XXX,
and Sxxx have excellent pit-
ting resistance. However, with copper content higher than
0.04%,
3xxx alloys are susceptible
to pitting. At 0.15% copper, they pit more extensively, especially in seawater. Alloys of the
~XXX,
~XXX,
and 7xxx series are normally clad to protect against pitting.
Factors Responsible for Pitting Corrosion.
Pitting corrosion is mostly due to copper,
mercury, and halide ions, of which chloride is the most damaging and often encountered in
service. Pitting corrosion can be prevented by removal of the reducible species required for a
cathodic reaction. In the absence of dissolved oxygen or other cathodic reactant, aluminum
will not corrode by pitting since it is not polarized to its pitting potential. Pitting in neutral
solutions is caused usually by oxygen.
Pitting Behavior.
The rate of pitting corrosion of aluminum depends on its polarization
behavior. As with other passive metals, corrosion of aluminum in the passive range, that is,
pH range
4-9,
may be of pitting corrosion. Pitting of aluminum diminishes beyond this range,
and corrosion proceeds uniformly.
Stress Corrosion Cracking.
SCC does not occur in commercial-purity alloys
(
1 xxx), alumi-
num-manganese alloys (~xxx), and aluminum-magnesium alloys containing less than 3% mag-
nesium (5xxx) and strengthened by cold work. On very rare occasions, SCC occurs in the
aluminum-magnesium-silicon
alloys (6xxx).
Susceptible Alloys.
SCC in wrought aluminum alloys is generally limited to those con-
taining appreciable amounts of soluble alloying elements of copper, magnesium, silicon, and
zinc [175]. Alloys that can be strengthened by cold work are relatively immune to SCC. The
wrought alloys that are susceptible to SCC include the following
[
175,1771:
The 2xxx series containing copper with smaller amounts of magnesium, manganese, and other
elements.
The 7xxx series containing zinc with small amounts of magnesium, manganese, copper, and
silicon, if any.
The Sxxx series containing more than
3%
magnesium with or without other alloying elements.
Factors Affecting Resistance to SCC.
In aluminum alloys, this cracking is characteristi-
cally intergranular. Factors that affect SCC of aluminum alloys are given next.
Directional Property
of
Aluminum.
SCC of an aluminum wrought alloy in a susceptible
temper is determined by the magnitude and the duration of a tensile stress acting on its surface,
and additionally, it is also determined by the direction of stressing. The effect of stressing in
different directions
is
caused by the highly directional grain structure that is typical of many
aluminum wrought products
[
173,1751. Resistance, which is measured by the magnitude of
tensile stress required to cause cracking,
is
highest when the stress is applied in the longitudinal
direction, lowest in the short transverse direction, and intermediate in the other direction. Resis-
tance in the short transverse direction usually controls application of products that are of thick
section or machined products with sustained tensile stresses in the short transverse direction.
Environment.
Water or water vapor is a requisite for the SCC of aluminum, and in its
absence, cracking does not occur. Among the species that accelerate cracking further, chlorides
have the greatest effect
[
1751.
Mitigation of SCC of Aluminum Alloys.
In addition to the usual procedures for prevent-
ing SCC of materials, there are several methods specifically applicable to aluminum alloys
[173]: