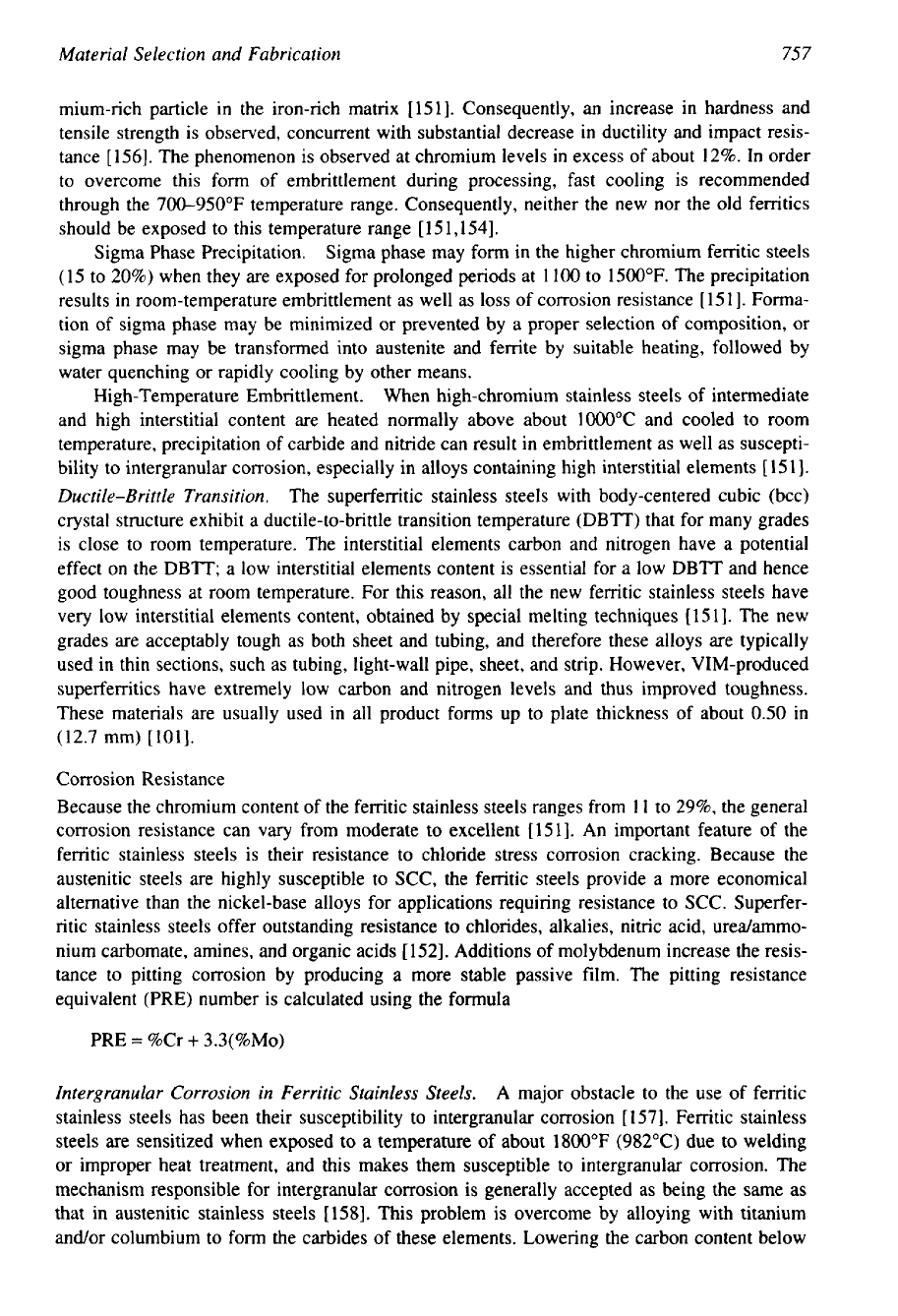
757
Material Selection and Fabrication
mium-rich particle in the iron-rich matrix [151]. Consequently, an increase in hardness and
tensile strength is observed, concurrent with substantial decrease in ductility and impact resis-
tance [156]. The phenomenon is observed at chromium levels
in
excess of about 12%. In order
to overcome this form of embrittlement during processing, fast cooling is recommended
through the 700-950°F temperature range. Consequently, neither the new nor the old ferritics
should be exposed to this temperature range
[
15 1,1541.
Sigma Phase Precipitation.
Sigma phase may
form
in the higher chromium ferritic steels
(15 to 20%) when they are exposed for prolonged periods at
1100
to 1500°F. The precipitation
results in room-temperature embrittlement as well as loss of corrosion resistance
[
15
I]. Forma-
tion of sigma phase may be minimized or prevented by a proper selection of composition, or
sigma phase may be transformed into austenite and ferrite by suitable heating, followed by
water quenching or rapidly cooling by other means.
High-Temperature Embrittlement.
When high-chromium stainless steels of intermediate
and high interstitial content are heated normally above about 1000°C and cooled to room
temperature, precipitation of carbide and nitride can result in embrittlement as well as suscepti-
bility to intergranular corrosion, especially in alloys containing high interstitial elements
[
15 11.
Ductile-Brittle Transition.
The superferritic stainless steels with body-centered cubic (bcc)
crystal structure exhibit a ductile-to-brittle transition temperature (DBTT) that for many grades
is close to room temperature. The interstitial elements carbon and nitrogen have a potential
effect on the DBTT; a low interstitial elements content is essential for a low DBTT and hence
good toughness at room temperature. For this reason, all the new ferritic stainless steels have
very low interstitial elements content, obtained by special melting techniques
[
15 11. The new
grades are acceptably tough as both sheet and tubing, and therefore these alloys are typically
used in thin sections, such as tubing, light-wall pipe, sheet, and strip. However, VIM-produced
superferritics have extremely low carbon and nitrogen levels and thus improved toughness.
These materials are usually used in all product forms up to plate thickness of about
0.50
in
(12.7 mm) [loll.
Corrosion Resistance
Because the chromium content of the ferritic stainless steels ranges from
I1
to
29%,
the general
corrosion resistance can
vary
from moderate to excellent [151]. An important feature of the
ferritic stainless steels is their resistance to chloride stress corrosion cracking. Because the
austenitic steels are highly susceptible to SCC, the ferritic steels provide a more economical
alternative than the nickel-base alloys for applications requiring resistance to SCC. Superfer-
ritic stainless steels offer outstanding resistance to chlorides, alkalies, nitric acid, uredammo-
nium carbomate, amines, and organic acids
[
1521. Additions of molybdenum increase the resis-
tance to pitting corrosion by producing a more stable passive film. The pitting resistance
equivalent (PRE) number
is
calculated using the formula
PRE
=
%Cr
+
3.3(%Mo)
Intergranular Corrosion in Ferritic Stainless Steels.
A major obstacle to the use of ferritic
stainless steels has been their susceptibility to intergranular corrosion
[
1571. Ferritic stainless
steels are sensitized when exposed to a temperature
of
about 1800°F (982°C) due to welding
or improper heat treatment, and this makes them susceptible to intergranular corrosion. The
mechanism responsible for intergranular corrosion is generally accepted as being the same as
that in austenitic stainless steels [158]. This problem is overcome by alloying with titanium
andor columbium to form the carbides of these elements. Lowering the carbon content below