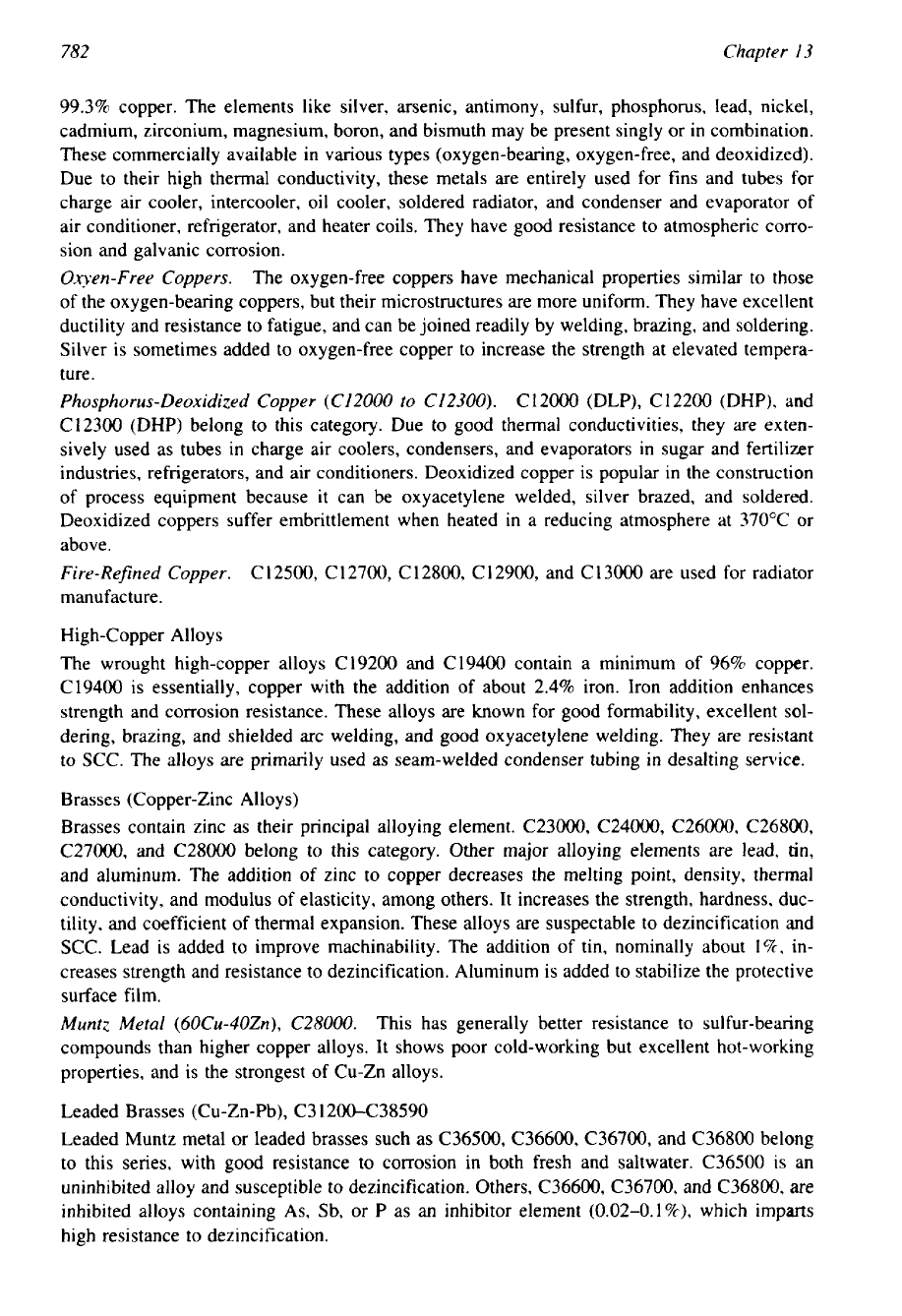
782 Chapter
13
99.3% copper. The elements like silver, arsenic, antimony, sulfur, phosphorus, lead, nickel,
cadmium, zirconium, magnesium, boron, and bismuth may be present singly or in combination.
These commercially available in various types (oxygen-bearing, oxygen-free, and deoxidized).
Due to their high thermal conductivity, these metals are entirely used for fins and tubes for
charge air cooler, intercooler, oil cooler, soldered radiator, and condenser and evaporator of
air conditioner, refrigerator, and heater coils. They have good resistance to atmospheric corro-
sion and galvanic corrosion.
0,xyen-Free Coppers.
The oxygen-free coppers have mechanical properties similar
to
those
of the oxygen-bearing coppers, but their microstructures are more uniform. They have excellent
ductility and resistance to fatigue, and can be joined readily by welding, brazing, and soldering.
Silver is sometimes added to oxygen-free copper to increase the strength at elevated tempera-
ture.
Phosphorus-Deoxidized Copper (C12000
to
CZ2300).
C12000 (DLP), C 12200 (DHP), and
C12300 (DHP) belong to this category. Due to good thermal conductivities, they are exten-
sively used as tubes in charge air coolers, condensers, and evaporators in sugar and fertilizer
industries, refrigerators, and air conditioners. Deoxidized copper is popular in the construction
of process equipment because it can be oxyacetylene welded, silver brazed, and soldered.
Deoxidized coppers suffer embrittlement when heated in a reducing atmosphere at 370°C or
above.
Fire-Refined Copper.
C12500, C12700, C12800, C12900, and C13000 are used for radiator
manufacture.
High-Copper Alloys
The wrought high-copper alloys C19200 and C19400 contain a minimum
of
96% copper.
C19400 is essentially, copper with the addition of about 2.4% iron. Iron addition enhances
strength and corrosion resistance. These alloys are known for good formability, excellent sol-
dering, brazing, and shielded arc welding, and good oxyacetylene welding. They are resistant
to SCC. The alloys are primarily used as seam-welded condenser tubing
in
desalting service.
Brasses (Copper-Zinc Alloys)
Brasses contain zinc as their principal alloying element. C23000, C24000, C26000, C26800,
C27000, and C28000 belong
to
this category. Other major alloying elements are lead, tin,
and aluminum. The addition of zinc to copper decreases the melting point, density, thermal
conductivity, and modulus of elasticity, among others. It increases the strength, hardness, duc-
tility, and coefficient
of
thermal expansion. These alloys are suspectable to dezincification and
SCC. Lead is added to improve machinability. The addition of tin, nominally about
I%,
in-
creases strength and resistance to dezincification. Aluminum is added to stabilize the protective
surface film.
Muntz
Metal
(60Cu-40Zn), C28000.
This has generally better resistance to sulfur-bearing
compounds than higher copper alloys. It shows poor cold-working but excellent hot-working
properties, and is the strongest of Cu-Zn alloys.
Leaded Brasses (Cu-Zn-Pb), C3 120O-C38590
Leaded Muntz metal or leaded brasses such as C36500, C36600, C36700, and C36800 belong
to this series, with good resistance to corrosion in both fresh and saltwater. C36500 is an
uninhibited alloy and susceptible to dezincification. Others, C36600, C36700, and C36800, are
inhibited alloys containing As, Sb, or
P
as an inhibitor element (0.02-0.1%), which imparts
high resistance to dezincification.