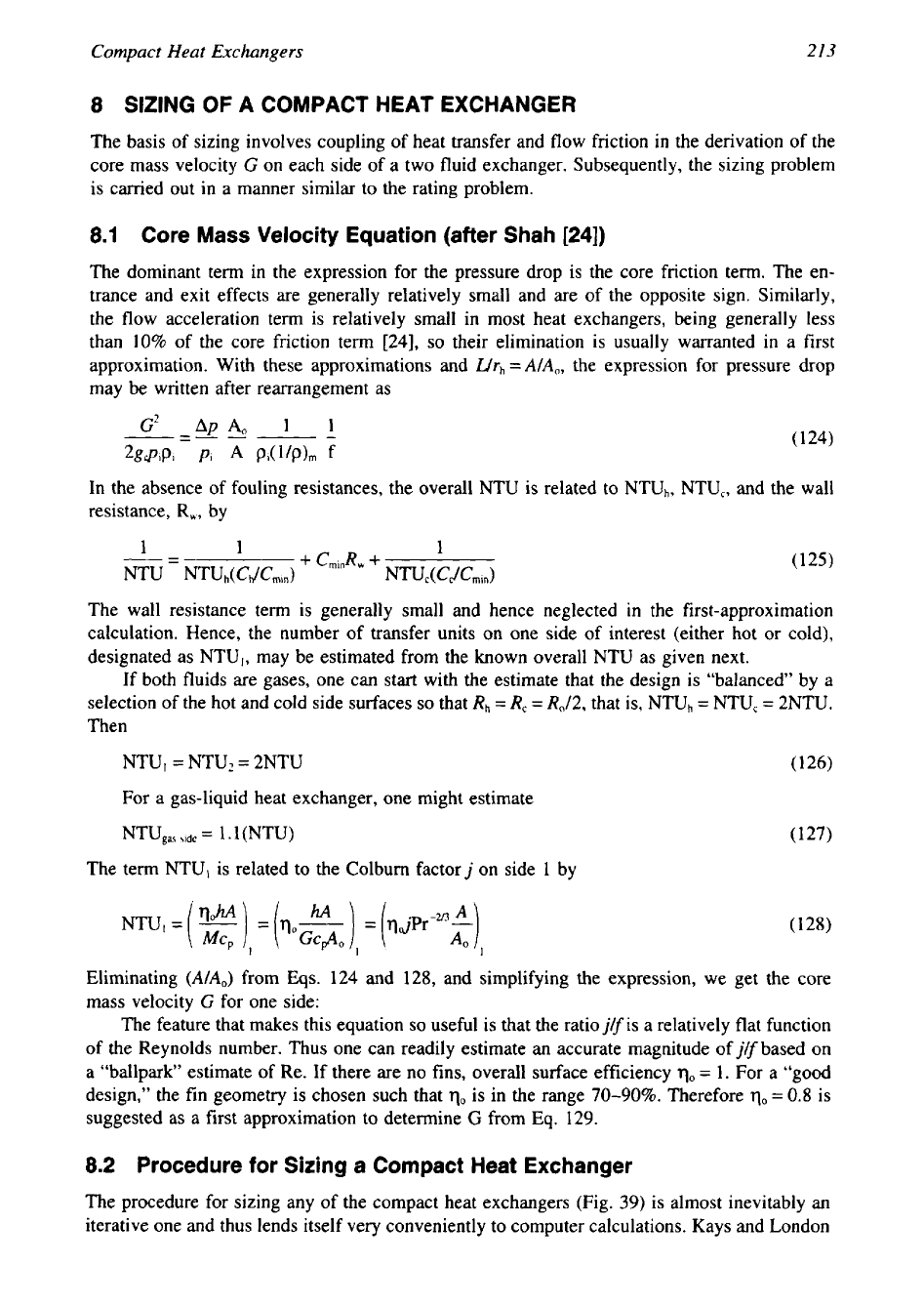
Compact Heat Exchangers
213
8 SIZING
OF
A
COMPACT HEAT EXCHANGER
The basis of sizing involves coupling of heat transfer and flow friction in the derivation of the
core mass velocity
G
on each side of a two fluid exchanger. Subsequently, the sizing problem
is carried out in a manner similar to the rating problem.
8.1
Core Mass Velocity Equation (after Shah
[24])
The dominant term in the expression for the pressure drop is the core friction term. The en-
trance and exit effects are generally relatively small and are of the opposite sign. Similarly,
the flow acceleration term is relatively small in most heat exchangers, being generally less
than
10%
of the core friction term [24],
so
their elimination is usually warranted in a first
approximation. With these approximations and Ldrh
=
AIA,,
the expression for pressure drop
may be written after rearrangement as
In the absence of fouling resistances, the overall NTU is related to NTUh, NTU,, and the wall
resistance, R,, by
The wall resistance term is generally small and hence neglected in the first-approximation
calculation. Hence, the number of transfer units
on
one side of interest (either hot or cold),
designated as NTUI, may be estimated from the known overall NTU as given next.
If both fluids are gases, one can start with the estimate that the design is “balanced” by a
selection of the hot and cold side surfaces
so
that Rh
=
R,
=
RJ2,
that
is,
NTUh
=
NTU,
=
2NTU.
Then
NTUI
=
NTU2
=
2NTU
(
126)
For a gas-liquid heat exchanger, one might estimate
NTUgas
side
=
1
-
1
(m)
(127)
The term NTU, is related to the Colburn factor
j
on side
1
by
Eliminating
(AIA,)
from
Eqs.
124 and
128,
and simplifying the expression, we get the core
mass velocity G for one side:
The feature that makes this equation
so
useful is that the ratiojlfis a relatively flat function
of the Reynolds number. Thus one can readily estimate an accurate magnitude of
jlf
based on
a “ballpark” estimate of
Re.
If there are no fins, overall surface efficiency
q,
=
1.
For a “good
design,” the fin geometry is chosen such that
qo
is in the range
70-90%.
Therefore
qo
=
0.8
is
suggested as a first approximation to determine
G
from Eq.
129.
8.2
Procedure for Sizing
a
Compact Heat Exchanger
The procedure for sizing any of the compact heat exchangers (Fig.
39)
is almost inevitably an
iterative one and thus lends itself very conveniently to computer calculations. Kays and London