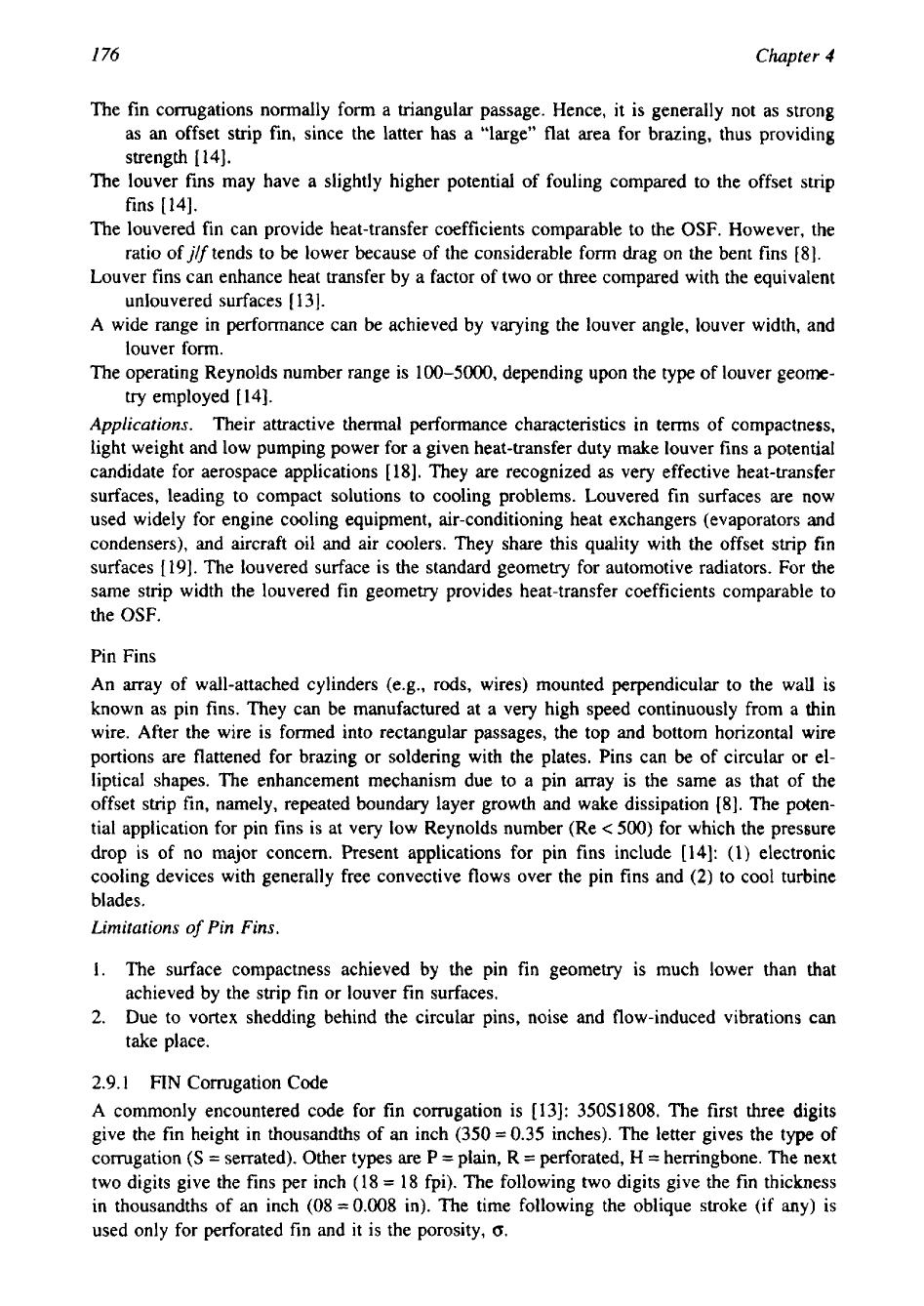
176
Chapter
4
The
fin
corrugations normally form a triangular passage. Hence, it is generally not as strong
as
an
offset strip
fin,
since the latter has a “large” flat area for brazing, thus providing
strength
[
141.
The louver fins may have a slightly higher potential of fouling compared to the offset strip
fins [14].
The louvered fin can provide heat-transfer coefficients comparable to the
OSF.
However, the
ratio of
j/f
tends to
be
lower because of the considerable form drag on the
bent
fins
[S].
Louver fins can enhance heat transfer by a factor
of
two or three compared with the equivalent
unlouvered surfaces
[
131.
A wide range in performance can be achieved by varying the louver angle, louver width, and
louver form.
The operating Reynolds number range is 100-5000, depending upon the type of louver geome-
try
employed
[
141.
Applications.
Their attractive thermal performance characteristics in terms
of
compactness,
light weight and low pumping power for a given heat-transfer duty make louver fins a potential
candidate for aerospace applications
[
181. They are recognized as very effective heat-transfer
surfaces, leading to compact solutions to cooling problems. Louvered fin surfaces are now
used widely
for
engine cooling equipment, air-conditioning heat exchangers (evaporators and
condensers), and aircraft oil and air coolers. They share this quality with the offset strip fin
surfaces
[
191. The louvered surface is the standard geometry for automotive radiators. For the
same strip width the louvered
fin
geometry provides heat-transfer coefficients comparable to
the OSF.
Pin Fins
An array of wall-attached cylinders (e.g., rods, wires) mounted perpendicular to the wall
is
known as pin fins. They can be manufactured at a very high speed continuously from a thin
wire. After the wire is formed into rectangular passages, the top and bottom horizontal wire
portions are flattened for brazing or soldering with the plates. Pins can be of circular or el-
liptical shapes. The enhancement mechanism due to a pin array is the same as that
of
the
offset strip
fin,
namely, repeated boundary layer growth and wake dissipation
[8].
The poten-
tial application for pin fins is at very low Reynolds number (Re
<
500)
for which the pressure
drop is of no major concern. Present applications for pin fins include [14]:
(1)
electronic
cooling devices with generally free convective flows over the pin fins and
(2)
to cool turbine
blades.
Limitations
of
Pin Fins.
1.
The surface compactness achieved by the pin
fin
geometry is much lower than that
achieved by the strip fin or louver
fin
surfaces.
2.
Due
to
vortex shedding behind the circular pins, noise and flow-induced vibrations can
take place.
2.9.1
FIN
Corrugation Code
A
commonly encountered code for fin corrugation is [13]: 350S1808. The first three digits
give the
fin
height
in
thousandths
of
an inch
(350=0.35
inches). The letter gives the
type
of
corrugation
(S
=
serrated). Other types are
P
=
plain, R
=
perforated,
H
=
herringbone. The next
two digits give the fins per inch (18
=
18 fpi). The following two digits give the
fin
thickness
in
thousandths of an inch
(08
=
0.008 in). The time following the oblique stroke
(if
any) is
used only for perforated fin and
it
is the porosity,
0.