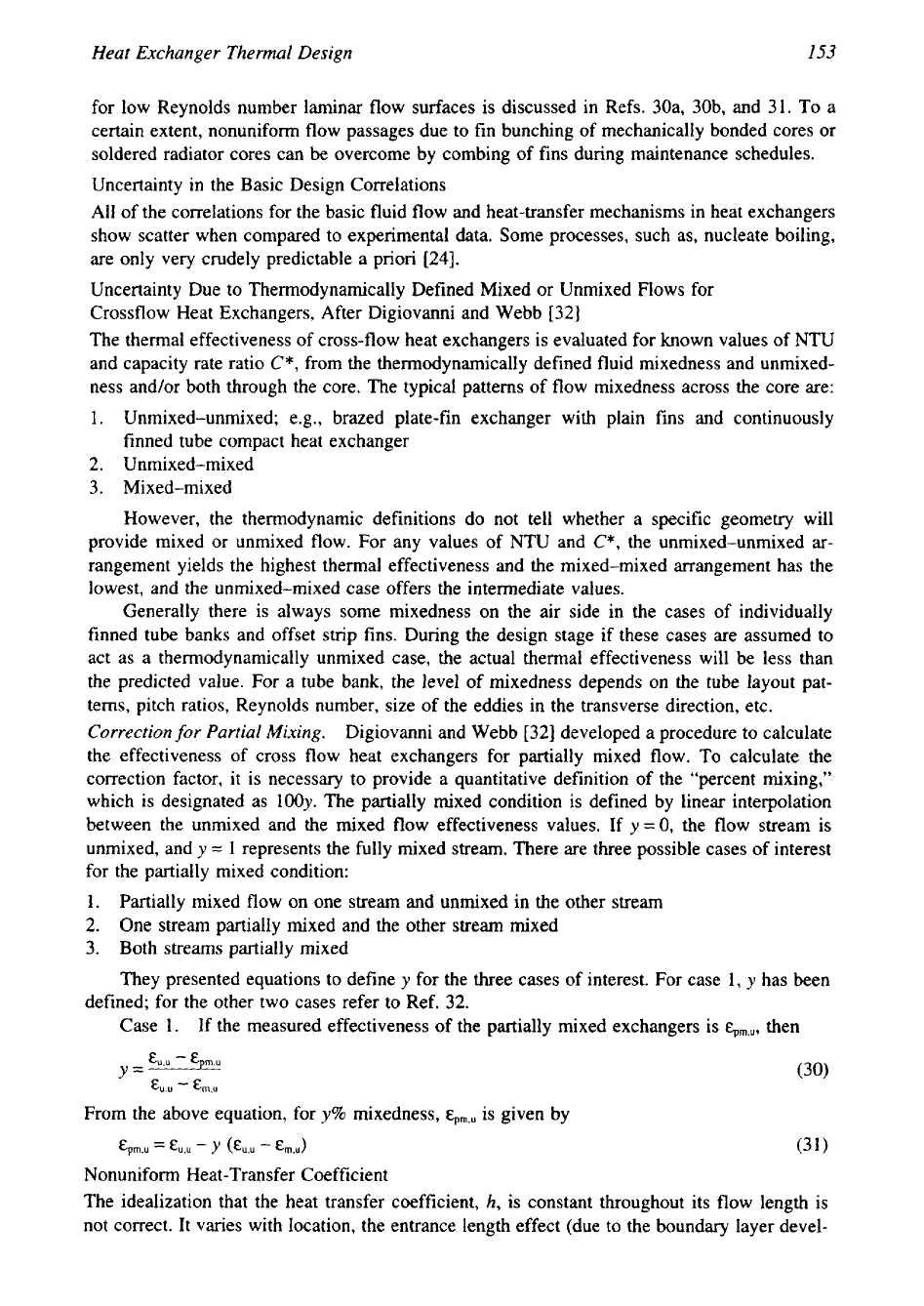
153
Heat Exchanger Thermal Design
for low Reynolds number laminar flow surfaces is discussed in Refs. 30a, 30b, and 31. To a
certain extent, nonuniform flow passages due to fin bunching of mechanically bonded cores or
soldered radiator cores can
be
overcome by combing of fins during maintenance schedules.
Uncertainty in the Basic Design Correlations
All of the correlations for the basic fluid flow and heat-transfer mechanisms in heat exchangers
show scatter when compared to experimental data. Some processes, such as, nucleate boiling,
are only very crudely predictable a priori
[24].
Uncertainty Due to Thermodynamically Defined Mixed or Unmixed Flows for
Crossflow Heat Exchangers, After Digiovanni and Webb
[32]
The thermal effectiveness of cross-flow heat exchangers is evaluated for known values of NTU
and capacity rate ratio
C*,
from the thermodynamically defined fluid mixedness and unmixed-
ness and/or both through the core. The typical patterns of flow mixedness across the core are:
1. Unmixed-unmixed; e.g., brazed plate-fin exchanger with plain fins and continuously
finned tube compact heat exchanger
2.
Unmixed-mixed
3. Mixed-mixed
However, the thermodynamic definitions
do
not tell whether a specific geometry will
provide mixed or unmixed flow. For any values of NTU and
C*,
the unmixed-unmixed ar-
rangement yields the highest thermal effectiveness and the mixed-mixed arrangement has the
lowest, and the unmixed-mixed case offers the intermediate values.
Generally there is always some mixedness on the air side in the cases of individually
finned tube banks and offset strip fins. During the design stage if these cases are assumed to
act
as
a thermodynamically unmixed case, the actual thermal effectiveness will be less than
the predicted value. For a tube bank, the level
of
mixedness depends on the tube layout pat-
terns, pitch ratios, Reynolds number, size of the eddies in the transverse direction, etc.
Correction
for
Partial
Mixing.
Digiovanni and Webb [32] developed a procedure to calculate
the effectiveness of cross flow heat exchangers for partially mixed flow. To calculate the
correction factor, it is necessary to provide a quantitative definition of the “percent mixing,”
which is designated
as
1OOy.
The partially mixed condition is defined by linear interpolation
between the unmixed and the mixed flow effectiveness values. If
y=O,
the flow stream is
unmixed, and
y
=
1
represents the fully mixed stream. There are three possible cases of interest
for the partially mixed condition:
1.
Partially mixed flow on one stream and unmixed in the other stream
2.
One stream partially mixed and the other stream mixed
3.
Both streams partially mixed
They presented equations to define
y
for the three cases of interest. For case
1,
y
has been
defined; for the other two cases refer to Ref. 32.
Case 1.
If the measured effectiveness of the partially mixed exchangers is
then
From the above equation, for
y%
mixedness,
is given by
~pm,u
=
&u,u
-
Y
(~,u
-
ErnJ
(31)
Nonuniform Heat-Transfer Coefficient
The idealization that the heat transfer coefficient,
h,
is constant throughout its flow length is
not correct. It varies with location, the entrance length effect (due to the boundary layer devel-