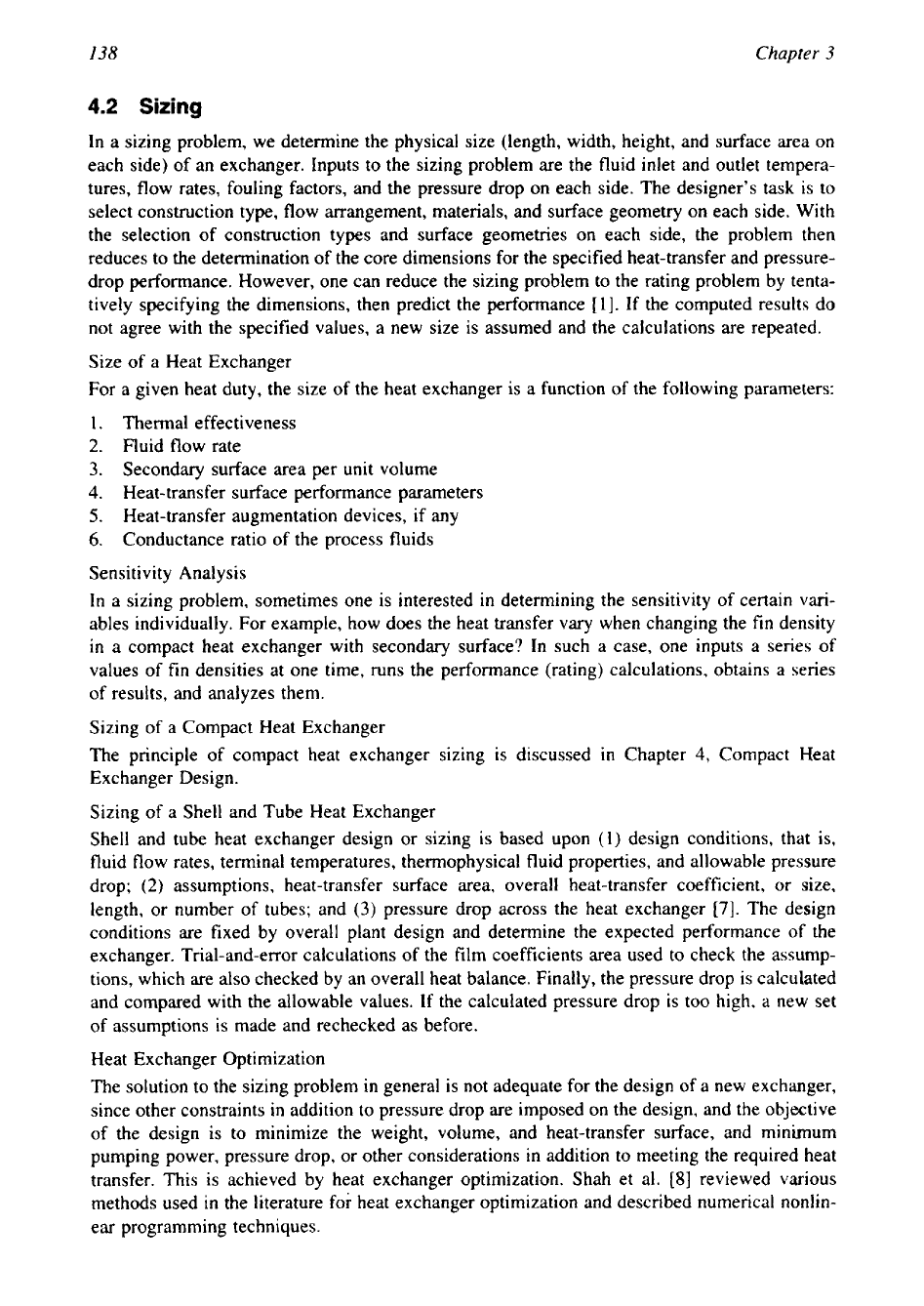
I38
Chapter
3
4.2
Sizing
In a sizing problem, we determine the physical size (length, width, height, and surface area on
each side) of an exchanger. Inputs to the sizing problem are the fluid inlet and outlet tempera-
tures, flow rates, fouling factors, and the pressure drop on each side. The designer’s task is to
select construction type, flow arrangement, materials, and surface geometry on each side. With
the selection of construction types and surface geometries on each side, the problem then
reduces to the determination of the core dimensions for the specified heat-transfer and pressure-
drop performance. However, one can reduce the sizing problem to the rating problem by tenta-
tively specifying the dimensions, then predict the performance
[
11.
If the computed results do
not agree with the specified values, a new size
is
assumed and the calculations are repeated.
Size
of
a Heat Exchanger
For a given heat duty, the size of the heat exchanger is a function of the following parameters:
1.
Thermal effectiveness
2.
Fluid flow rate
3.
Secondary surface area per unit volume
4. Heat-transfer surface performance parameters
5.
Heat-transfer augmentation devices, if any
6,
Conductance ratio of the process fluids
Sensitivity Analysis
In a sizing problem, sometimes one is interested
in
determining the sensitivity of certain vari-
ables individually. For example, how does the heat transfer
vary
when changing the fin density
in
a compact heat exchanger with secondary surface? In such a case, one inputs a series of
values of fin densities at one time, runs the performance (rating) calculations, obtains a series
of results, and analyzes them.
Sizing of a Compact Heat Exchanger
The principle of compact heat exchanger sizing is discussed in Chapter
4,
Compact Heat
Exchanger Design.
Sizing of a Shell and Tube Heat Exchanger
Shell and tube heat exchanger design or sizing is based upon
(1)
design conditions, that is,
fluid flow rates, terminal temperatures, thermophysical fluid properties, and allowable pressure
drop;
(2)
assumptions, heat-transfer surface area, overall heat-transfer coefficient, or size,
length, or number of tubes; and
(3)
pressure
drop
across the heat exchanger
[7].
The design
conditions are fixed by overall plant design and determine the expected performance
of
the
exchanger, Trial-and-error calculations of the film coefficients area used to check the assump-
tions, which are also checked by an overall heat balance. Finally, the pressure drop is calculated
and compared with the allowable values. If the calculated pressure drop is too high, a new set
of assumptions
is
made and rechecked as before.
Heat Exchanger Optimization
The solution to the sizing problem in general is not adequate for the design of a new exchanger,
since other constraints in addition to pressure drop are imposed on the design, and the objective
of the design is to minimize the weight, volume, and heat-transfer surface, and minimum
pumping power, pressure drop, or other considerations in addition to meeting the required heat
transfer. This is achieved by heat exchanger optimization. Shah et al.
[8]
reviewed various
methods used in the literature for heat exchanger optimization and described numerical nonlin-
ear programming techniques.