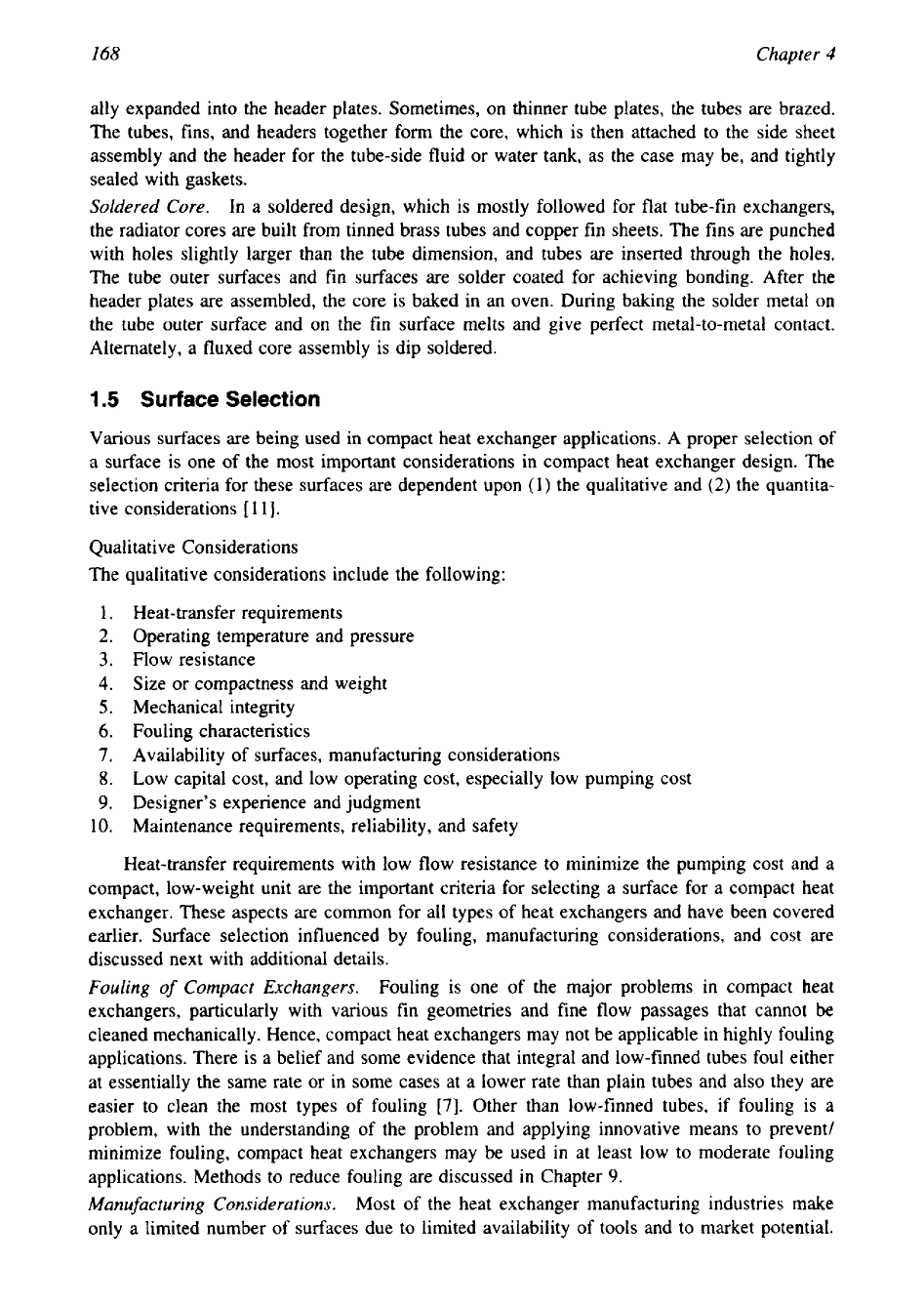
I68
Chapter
4
ally expanded into the header plates. Sometimes, on thinner tube plates, the tubes are brazed.
The tubes, fins, and headers together form the core, which is then attached to the side sheet
assembly and the header for the tube-side fluid or water tank, as the case may be, and tightly
sealed with gaskets.
Soldered Core.
In a soldered design, which is mostly followed for flat tube-fin exchangers,
the radiator cores are built from tinned brass tubes and copper fin sheets. The fins are punched
with holes slightly larger than the tube dimension, and tubes are inserted through the holes.
The tube outer surfaces and
fin
surfaces are solder coated for achieving bonding. After the
header plates are assembled, the core is baked in an oven. During baking the solder metal
on
the tube outer surface and on the fin surface melts and give perfect metal-to-metal contact.
Alternately, a fluxed core assembly is dip soldered.
1.5
Surface Selection
Various surfaces are being used in compact heat exchanger applications.
A
proper selection of
a surface is one of the most important considerations in compact heat exchanger design. The
selection criteria for these surfaces are dependent upon
(1)
the qualitative and
(2)
the quantita-
tive considerations
[
1
11.
Qualitative Considerations
The qualitative considerations include the following:
1.
Heat-transfer requirements
2.
Operating temperature and pressure
3.
Flow resistance
4.
Size or compactness and weight
5.
Mechanical integrity
6.
Fouling characteristics
7.
Availability of surfaces, manufacturing considerations
8.
Low capital cost, and low operating cost, especially low pumping cost
9.
Designer’s experience and judgment
10.
Maintenance requirements, reliability, and safety
Heat-transfer requirements with low flow resistance to minimize the pumping cost and a
compact, low-weight unit are the important criteria for selecting a surface for a compact heat
exchanger. These aspects are common for all types of heat exchangers and have been covered
earlier. Surface selection influenced by fouling, manufacturing considerations, and cost are
discussed next with additional details.
Fouling
of
Compact Exchangers.
Fouling is one of the major problems in compact heat
exchangers, particularly with various fin geometries and fine flow passages that cannot
be
cleaned mechanically. Hence, compact heat exchangers may not be applicable in highly fouling
applications. There is a belief and some evidence that integral and low-finned tubes foul either
at essentially the same rate or in some cases at a lower rate than plain tubes and also they are
easier to clean the most types of fouling
[7].
Other than low-finned tubes,
if
fouling is a
problem, with the understanding of the problem and applying innovative means to prevent/
minimize fouling, compact heat exchangers may be used in at least low to moderate fouling
applications. Methods to reduce fouling are discussed in Chapter
9.
Manufacturing Considerations.
Most of the heat exchanger manufacturing industries make
only a limited number of surfaces due to limited availability of tools and
to
market potential.