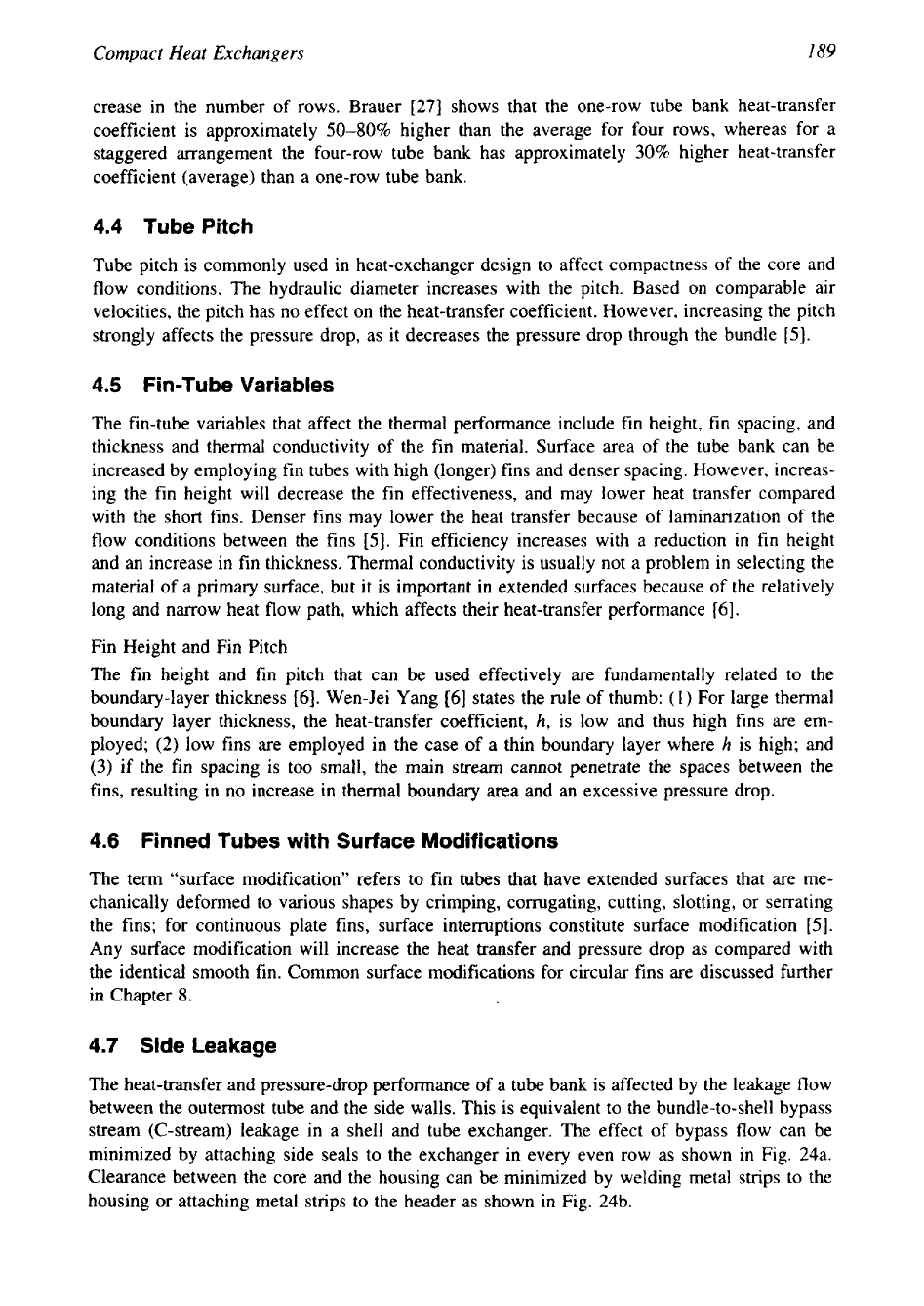
Compact
Heat Exchangers
189
crease in the number of rows. Brauer
[27]
shows that the one-row tube bank heat-transfer
coefficient is approximately
50430%
higher than the average for four rows, whereas for a
staggered arrangement the four-row tube bank has approximately
30%
higher heat-transfer
coefficient (average) than a one-row tube bank.
4.4 Tube Pitch
Tube pitch is commonly used in heat-exchanger design to affect compactness of the core and
flow conditions. The hydraulic diameter increases with the pitch. Based on comparable air
velocities, the pitch has no effect on the heat-transfer coefficient. However, increasing the pitch
strongly affects the pressure drop, as it decreases the pressure drop through the bundle
[5].
4.5 Fin-Tube Variables
The fin-tube variables that affect the thermal performance include fin height, fin spacing, and
thickness and thermal conductivity of the
fin
material. Surface area of the tube bank can be
increased by employing fin tubes with high (longer) fins and denser spacing. However, increas-
ing the fin height will decrease the fin effectiveness, and may lower heat transfer compared
with the short fins. Denser fins may lower the heat transfer because of laminarization of the
flow conditions between the fins
[5].
Fin efficiency increases with a reduction in
fin
height
and an increase in fin thickness. Thermal conductivity is usually not a problem in selecting the
material of a primary surface, but it is important in extended surfaces because of the relatively
long and narrow heat flow path, which affects their heat-transfer performance
[6].
Fin Height and Fin Pitch
The fin height and fin pitch that can be used effectively are fundamentally related to the
boundary-layer thickness
[6].
Wen-Jei Yang
[6]
states the rule of thumb:
(I)
For large thermal
boundary layer thickness, the heat-transfer coefficient,
h,
is low and thus high fins are em-
ployed;
(2)
low fins are employed in the case of a thin boundary layer where
h
is high; and
(3)
if the fin spacing is too small, the main stream cannot penetrate the spaces between the
fins, resulting in no increase in thermal boundary area and an excessive pressure drop.
4.6
Finned Tubes with Surface Modifications
The term “surface modification” refers to fin
tubes
that have extended surfaces that are me-
chanically deformed to various shapes by crimping, corrugating, cutting, slotting, or serrating
the fins; for continuous plate fins, surface interruptions constitute surface modification
[5].
Any surface modification will increase the heat transfer and pressure drop as compared with
the identical smooth fin. Common surface modifications for circular fins are discussed further
in Chapter
8.
4.7 Side Leakage
The heat-transfer and pressure-drop performance of a tube bank is affected by the leakage flow
between the outermost tube and the side walls. This is equivalent
to
the bundle-to-shell bypass
stream (C-stream) leakage in a shell and tube exchanger. The effect of bypass flow can be
minimized by attaching side seals to the exchanger in every even row as shown in Fig. 24a.
Clearance between the core and the housing can be minimized by welding metal strips to the
housing or attaching metal strips to the header as shown in Fig. 24b.