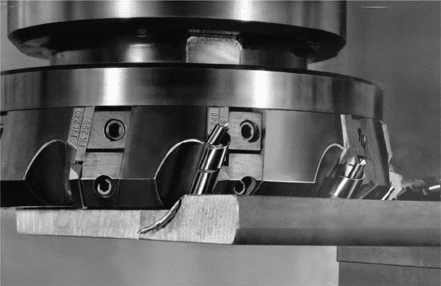
394 9 Processes with Rotational Primary Movement
avoided by varying the cutting edge geometry and feed rate accordingly. The most
favourable type of contact is “U-contact”, in which the cutting edge point that is
furthest removed from the minor and major cutting edges is the first to make contact
with the workpiece. All other types of point or line contact are regarded as inter-
mediate stages between S-contact and U-contact with respect to impact sensitivity
[Kron54, Beck69, Damm82].
“Helical chip milling” (γ
f
< 0, γ
p
> 0) has become established as a method
for improving chip removal, which is often problematic in the case of rotating tools
(Fig. 9.17).
In comparison to the entry conditions, greater importance is attached to the exit
conditions with respect to wear caused by fractures [Kron54, Okus63, Hosh65,
Beck69, Lola75, Peke78, Peke79, Köll86]. In the case of tool exit with finite unde-
formed chip thickness (e.g. in up milling), tensile stresses can arise in the cutting
edge in the unencumbered state because of resilience, which lead to cutting edge
fracture.
This phenomenon must be taken into account when determining milling strate-
gies. The use of tougher cemented carbides may increase the length of tool life until
failure, but that alone cannot prevent premature failure in the case of unfavourable
exit conditions. In order to improve cutting edge stability, additionally stabilizing
protective chamfers are fitted near the corner and on the cutting edge.
Cutting interruptions mean thermal and dynamic alternate stresses for the cutting
tool material, which can cause comb and parallel cracks and thus lead to cutting edge
fracture. The cutting tool materials used must therefore be very tough, temperature-
resistant and have high edge strength [Vier70].
For steel-working, high-speed steel and tough cemented carbides of machining
application groups P15 to P40 are used; for machining cast iron, NE metals, plastic
and hardened steels types K10 to K30 are used. The cutting tool materials used for
milling were developed with an eye to increased thermal and mechanical alternate
stress and are thus usually not directly comparable with the cutting tool material
types used for turning.
Fig. 9.17 Helical chip milling cutter in use (Source: Walter)