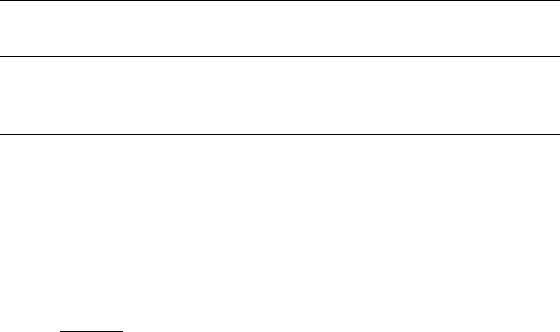
258 CHAPTER 6
Table 6.9. Regenerator parameters (50,000 B/D)
Residence time Regenerator inventory
Regenerator type (Min) Temperature (
◦
F) (tons)
Bubbling bed 5–20 1,100 300–800
Turbulent bed 3–5 1,250–1,350 200
Fast-fluidized bed 1–3 1,275–1,350 120
Shorter contact times and smaller catalyst inventories limit operable regeneration
conditions and need higher internal catalyst recycle rates for increased throughput or
coke burn. Since catalyst is frequently added on a pound per barrel basis each of these
units would use about 5 tons/day of fresh catalyst. Equation (5) relates the catalyst
activity to S, the daily fractional replacement rate or age of the catalyst:
A =
A
O
S
K
D
+ S
. (5)
This equation implies the smaller inventory would give the highest equilibrium or unit
activity. However, K is also a function of the contacting between the spent catalyst
and air, the mix temperature, the catalyst type and activity and the number of cycles
the catalyst makes through the system. This latter fact implies there is an optimum
unit inventory for a given processing capacity.
Commercial regenerator designs are shown in Figure 6.15. These utilize either turbu-
lent beds or fast-fluidized beds. Cocurrent or countercurrent contacting of the catalyst
and air is practiced and care is taken to prevent short-circuiting of the catalyst from
the regenerator inlet to the outlet to ensure an even, low carbon distribution on the
regenerated catalyst.
Resid catalytic cracking
Processing heavier feeds poses challenges to the normal FCC design due to the higher
coke laydown on the catalyst during the cracking reactions. The coke layed down in
the cracking process has been shown to come from four main sources as shown in
Table 6.10.
The catalytic coke comes from the secondary cracking reactions and are caused by
polymerization and condensation of hydrocarbons. Strippable coke are the hydro-
carbons that are entrained with the spent catalyst that enters the regenerator. Heavy
metals that lay down on the catalyst surface promote dehydrogenation and lead to
extra coke and hydrogen. Nickel, vanadium, and Iron are the main contaminates
though occasionally copper, zinc, and lead have been known to cause problems. Feed
coke has been associated with the carbon residue in the feed as measured in the
Conradson Carbon Test (ASTM). This has been also referred to as additive coke.