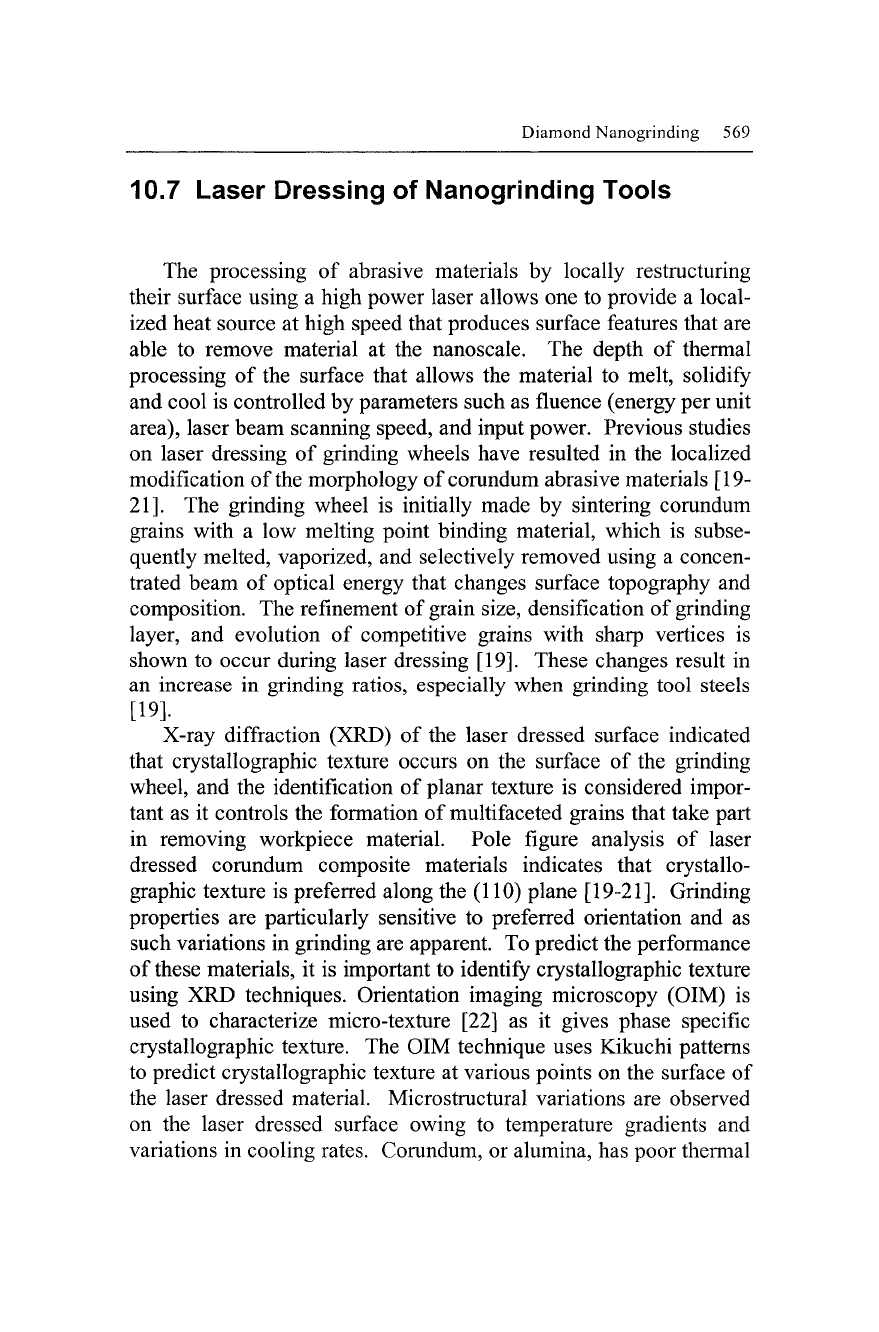
Diamond Nanogrinding 569
10.7 Laser Dressing of Nanogrinding Tools
The processing of abrasive materials by locally restructuring
their surface using a high power laser allows one to provide a local-
ized heat source at high speed that produces surface features that are
able to remove material at the nanoscale. The depth of thermal
processing of the surface that allows the material to melt, solidify
and cool is controlled by parameters such as fluence (energy per unit
area),
laser beam scanning speed, and input power. Previous studies
on laser dressing of grinding wheels have resulted in the localized
modification of the morphology of corundum abrasive materials [19-
21].
The grinding wheel is initially made by sintering corundum
grains with a low melting point binding material, which is subse-
quently melted, vaporized, and selectively removed using a concen-
trated beam of optical energy that changes surface topography and
composition. The refinement of grain size, densification of grinding
layer, and evolution of competitive grains with sharp vertices is
shown to occur during laser dressing [19]. These changes result in
an increase in grinding ratios, especially when grinding tool steels
[19].
X-ray diffraction (XRD) of the laser dressed surface indicated
that crystallographic texture occurs on the surface of the grinding
wheel, and the identification of planar texture is considered impor-
tant as it controls the formation of multifaceted grains that take part
in removing workpiece material. Pole figure analysis of laser
dressed corundum composite materials indicates that crystallo-
graphic texture is preferred along the (110) plane [19-21]. Grinding
properties are particularly sensitive to preferred orientation and as
such variations in grinding are apparent. To predict the performance
of these materials, it is important to identify crystallographic texture
using XRD techniques. Orientation imaging microscopy (OIM) is
used to characterize micro-texture [22] as it gives phase specific
crystallographic texture. The OIM technique uses Kikuchi patterns
to predict crystallographic texture at various points on the surface of
the laser dressed material. Microstructural variations are observed
on the laser dressed surface owing to temperature gradients and
variations in cooling rates. Corundum, or alumina, has poor thermal