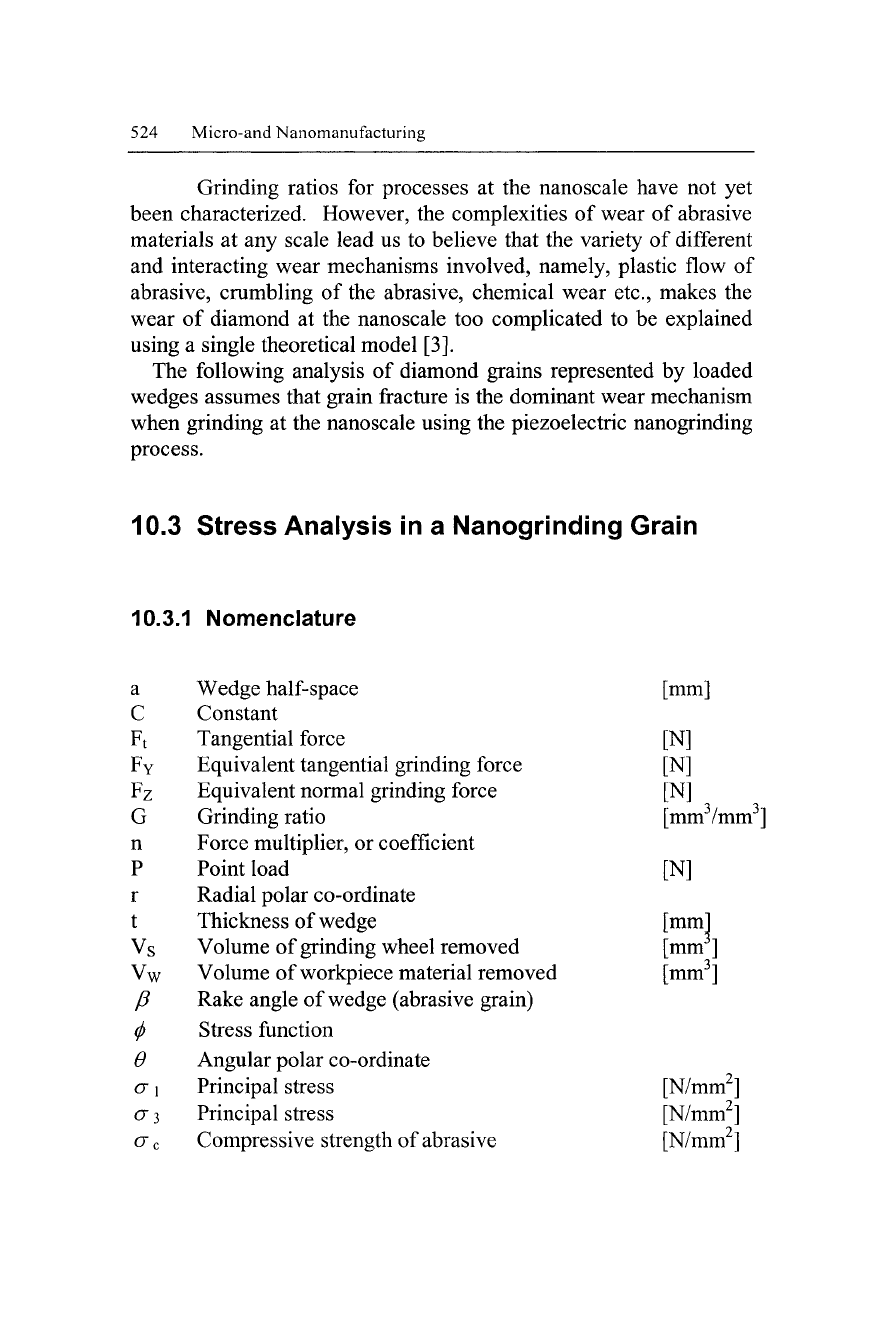
524 Micro-and Nanomanufacturing
Grinding ratios for processes at the nanoscale have not yet
been characterized. However, the complexities of wear of abrasive
materials at any scale lead us to believe that the variety of different
and interacting wear mechanisms involved, namely, plastic flow of
abrasive, crumbling of the abrasive, chemical wear etc., makes the
wear of diamond at the nanoscale too complicated to be explained
using a single theoretical model [3].
The following analysis of diamond grains represented by loaded
wedges assumes that grain fracture is the dominant wear mechanism
when grinding at the nanoscale using the piezoelectric nanogrinding
process.
10.3 Stress Analysis in a Nanogrinding Grain
10.3.1 Nomenclature
a
C
Ft
F
Y
Fz
G
n
P
r
t
V
s
V
w
P
<i>
0
C\
a
3
o-
c
Wedge half-space
Constant
Tangential force
Equivalent tangential grinding force
Equivalent normal grinding force
Grinding ratio
Force multiplier, or coefficient
Point load
Radial polar co-ordinate
Thickness of wedge
Volume of grinding wheel removed
Volume of workpiece material removed
Rake angle of wedge (abrasive grain)
Stress function
Angular polar co-ordinate
Principal stress
Principal stress
Compressive strength of abrasive
[mm]
[N]
[N]
[N]
[mm /mm ]
[N]
[mm]
M
[mm
3
]
[N/mm
2
]
[N/ram
2
]
[N/mm
2
]