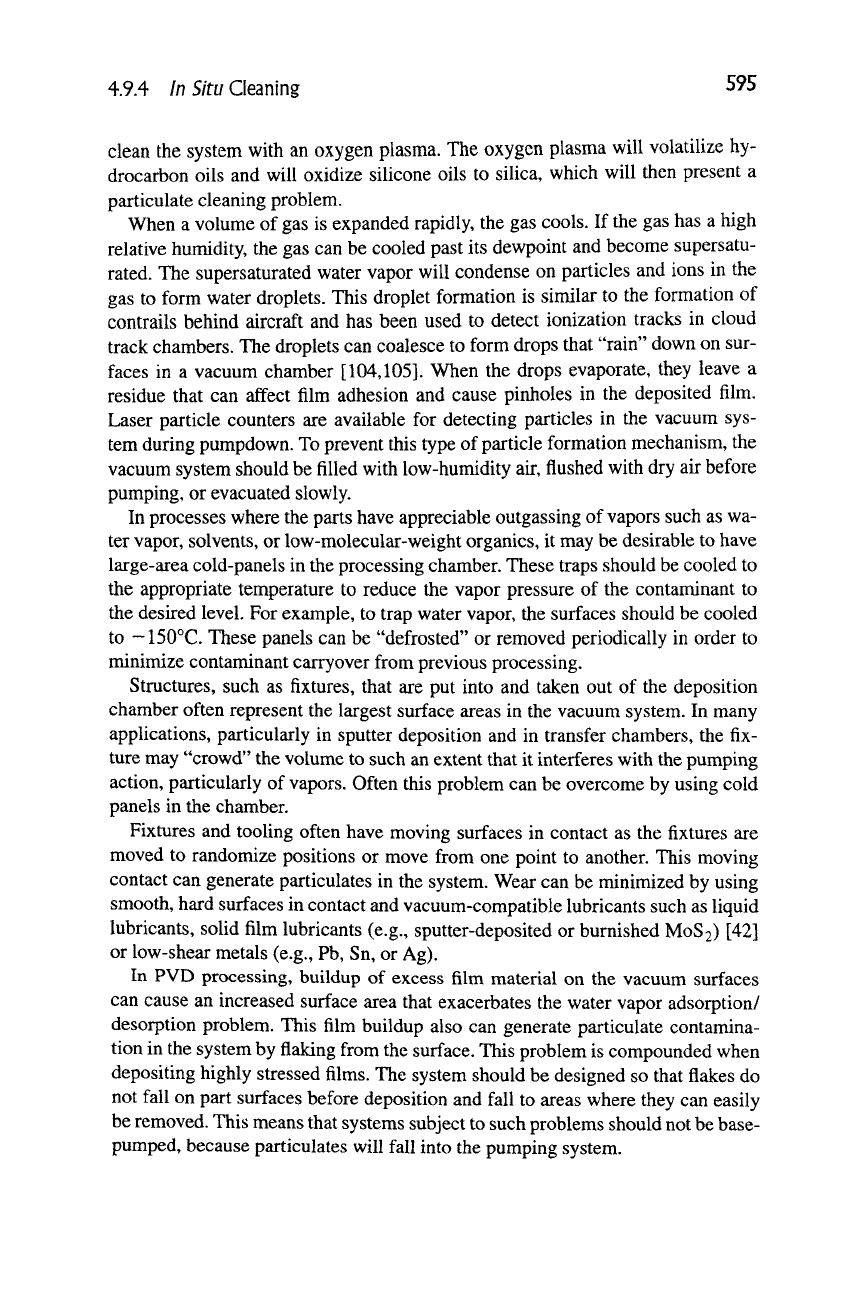
4.9.4 In
Situ
Cleaning 595
clean the system with an oxygen plasma. The oxygen plasma will volatilize hy-
drocarbon oils and will oxidize silicone oils to silica, which will then present a
particulate cleaning problem.
When a volume of gas is expanded rapidly, the gas cools. If the gas has a high
relative humidity, the gas can be cooled past its dewpoint and become supersatu-
rated. The supersaturated water vapor will condense on particles and ions in the
gas to form water droplets. This droplet formation is similar to the formation of
contrails behind aircraft and has been used to detect ionization tracks in cloud
track chambers. The droplets can coalesce to form drops that "rain" down on sur-
faces in a vacuum chamber [104,105]. When the drops evaporate, they leave a
residue that can affect film adhesion and cause pinholes in the deposited film.
Laser particle counters are available for detecting particles in the vacuum sys-
tem during pumpdown. To prevent this type of particle formation mechanism, the
vacuum system should be filled with low-humidity air, flushed with dry air before
pumping, or evacuated slowly.
In processes where the parts have appreciable outgassing of vapors such as wa-
ter vapor, solvents, or low-molecular-weight organics, it may be desirable to have
large-area cold-panels in the processing chamber. These traps should be cooled to
the appropriate temperature to reduce the vapor pressure of the contaminant to
the desired level. For example, to trap water vapor, the surfaces should be cooled
to
—
150°C.
These panels can be "defrosted" or removed periodically in order to
minimize contaminant carryover from previous processing.
Structures, such as fixtures, that are put into and taken out of the deposition
chamber often represent the largest surface areas in the vacuum system. In many
applications, particularly in sputter deposition and in transfer chambers, the fix-
ture may "crowd" the volume to such an extent that it interferes with the pumping
action, particularly of
vapors.
Often this problem can be overcome by using cold
panels in the chamber.
Fixtures and tooling often have moving surfaces in contact as the fixtures are
moved to randomize positions or move from one point to another. This moving
contact can generate particulates in the system. Wear can be minimized by using
smooth, hard surfaces in contact and vacuum-compatible lubricants such as liquid
lubricants, solid film lubricants (e.g., sputter-deposited or burnished M0S2) [42]
or low-shear metals (e.g., Pb, Sn, or Ag).
In PVD processing, buildup of excess film material on the vacuum surfaces
can cause an increased surface area that exacerbates the water vapor adsorption/
desorption problem. This film buildup also can generate particulate contamina-
tion in the system by flaking from the surface. This problem is compounded when
depositing highly stressed films. The system should be designed so that flakes do
not fall on part surfaces before deposition and fall to areas where they can easily
be removed. This means that systems subject to such problems should not be base-
pumped, because particulates will fall into the pumping system.