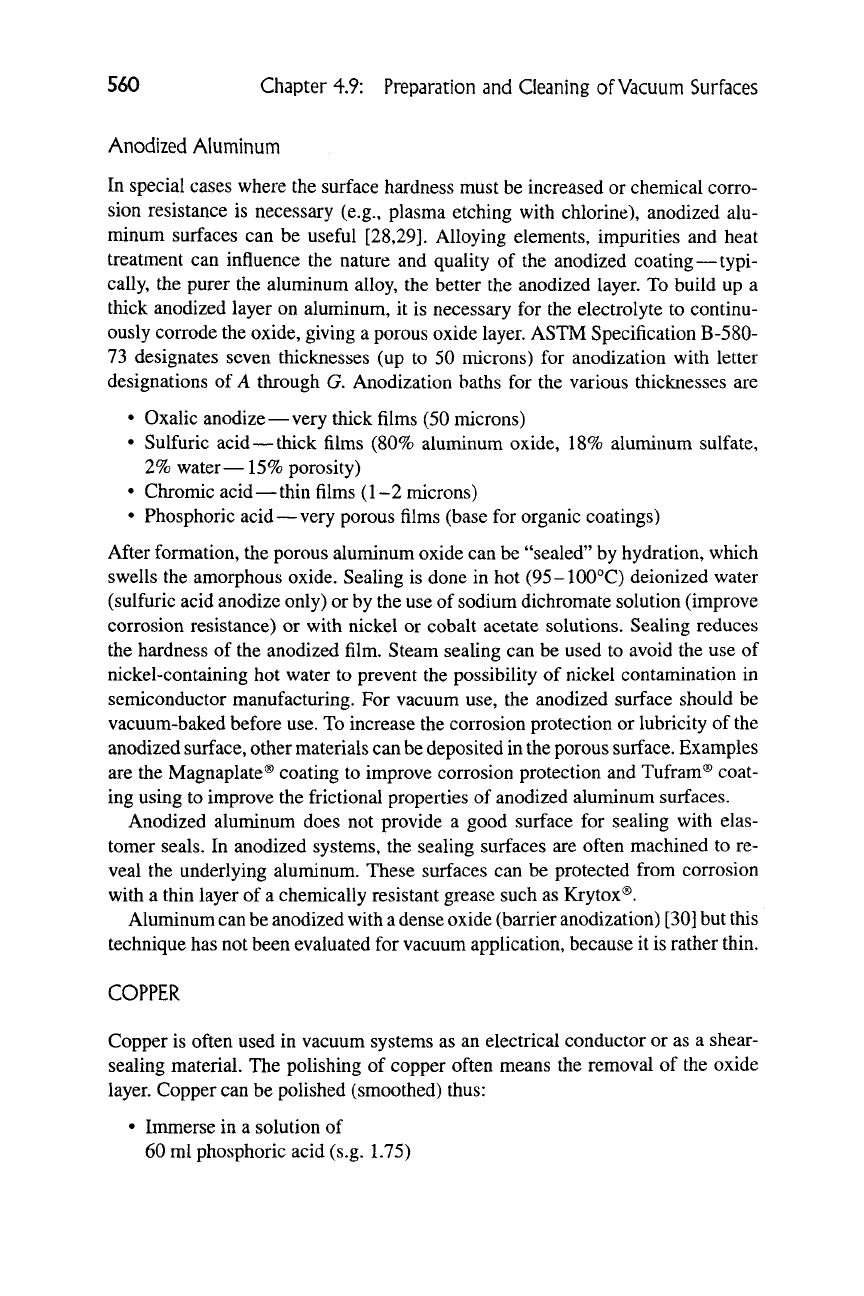
560 Chapter 4.9: Preparation and Cleaning of Vacuum Surfaces
Anodized Aluminum
In special cases where the surface hardness must be increased or chemical corro-
sion resistance is necessary (e.g., plasma etching with chlorine), anodized alu-
minum surfaces can be useful [28,29]. Alloying elements, impurities and heat
treatment can influence the nature and quality of the anodized coating — typi-
cally, the purer the aluminum alloy, the better the anodized layer. To build up a
thick anodized layer on aluminum, it is necessary for the electrolyte to continu-
ously corrode the oxide, giving a porous oxide layer. ASTM Specification B-580-
73 designates seven thicknesses (up to 50 microns) for anodization with letter
designations of A through G. Anodization baths for the various thicknesses are
• Oxalic anodize — very thick films (50 microns)
• Sulfuric acid — thick films (80% aluminum oxide, 18% aluminum sulfate,
2%
water—15% porosity)
• Chromic acid—thin films (1-2 microns)
• Phosphoric acid—very porous films (base for organic coatings)
After formation, the porous aluminum oxide can be "sealed" by hydration, which
swells the amorphous oxide. Sealing is done in hot (95-100°C) deionized water
(sulfuric acid anodize only) or by the use of sodium dichromate solution (improve
corrosion resistance) or with nickel or cobalt acetate solutions. Sealing reduces
the hardness of the anodized film. Steam sealing can be used to avoid the use of
nickel-containing hot water to prevent the possibility of nickel contamination in
semiconductor manufacturing. For vacuum use, the anodized surface should be
vacuum-baked before use. To increase the corrosion protection or lubricity of the
anodized surface, other materials can be deposited in the porous surface. Examples
are the Magnaplate® coating to improve corrosion protection and Tufram® coat-
ing using to improve the frictional properties of anodized aluminum surfaces.
Anodized aluminum does not provide a good surface for sealing with elas-
tomer seals. In anodized systems, the sealing surfaces are often machined to re-
veal the underlying aluminum. These surfaces can be protected from corrosion
with a thin layer of a chemically resistant grease such as Krytox®.
Aluminum can be anodized with
a
dense oxide (barrier anodization) [30] but this
technique has not been evaluated for vacuum application, because it is rather thin.
COPPER
Copper is often used in vacuum systems as an electrical conductor or as a shear-
sealing material. The polishing of copper often means the removal of the oxide
layer. Copper can be polished (smoothed) thus:
• Inmierse in a solution of
60 ml phosphoric acid (s.g. 1.75)