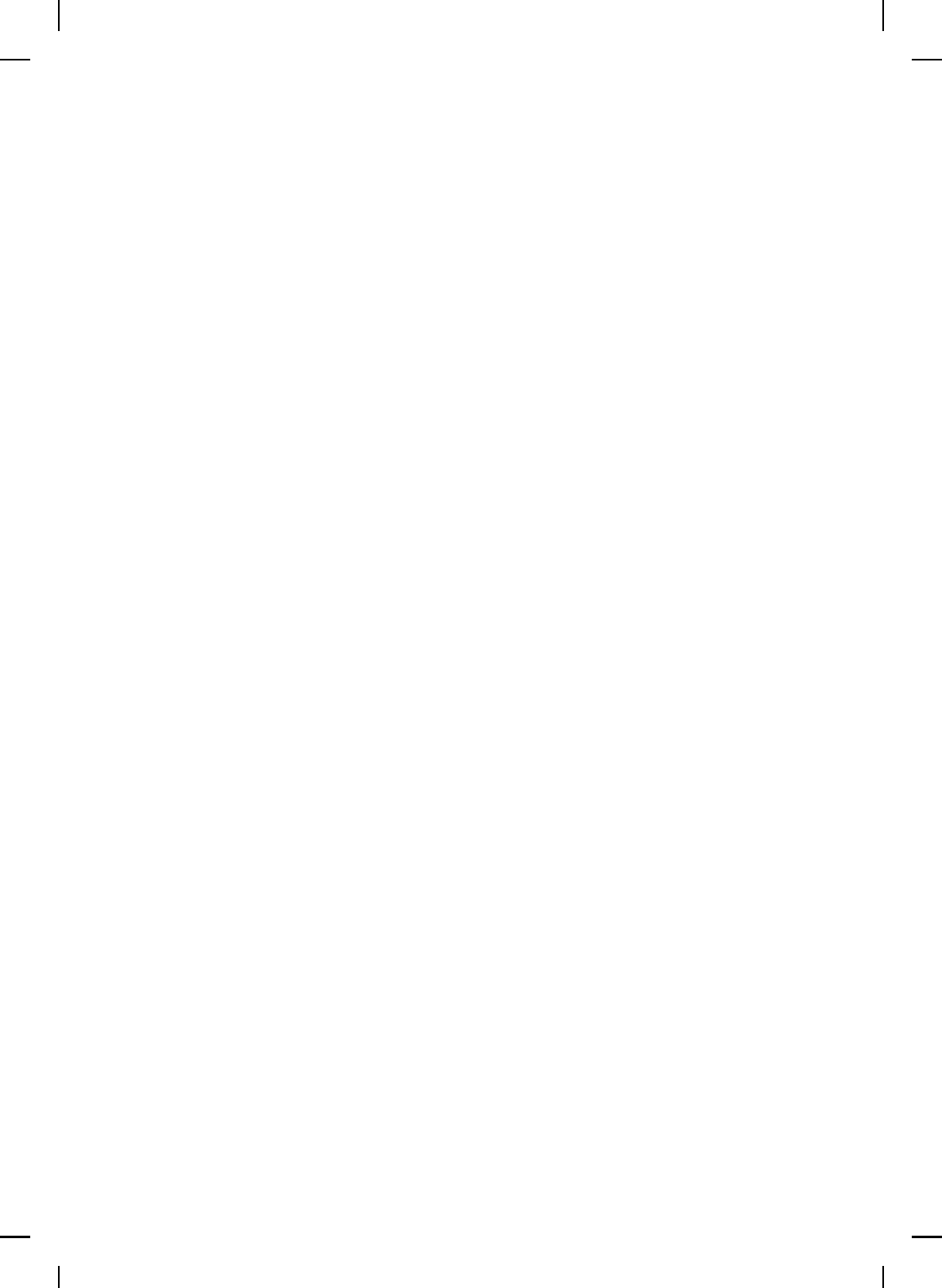
NonlinearBook10pt November 20, 2007
582 CHAPTER 9
abscissa corresponds to the circumferentially averaged mass flow through
the compressor and the ordinate corresponds to the normalized total-
to-static pressure rise in the compressor. For maximum compressor
performance, operating conditions require that the pressure rise in the
compressor correspond to the maximum pressure operating point on the
stable axisymmetric branch for a given throttle opening. Here, we
distinguish between compressor performance (pr essure rise) and compressor
efficiency (specific power consumption) where, depending on how the
compressor is designed, the most efficient operating point may be to the
right of the peak of the compressor characteristic map. In practice, however,
compression system uncertainties and compression system d isturbances can
perturb the operating point into an unstable r egion d riving the system to
a stalled stable equilibrium, a stable limit cycle (surge), or both. In the
case of rotating stall, an attempt to recover to a high pressure operating
point by increasing the flow through the throttle traps the s ystem within a
flow range corresponding to two stable operating conditions involving steady
axisymmetric flow and rotating stall resulting in severe hysteresis.
To avoid rotating stall and surge, trad itionally system designers allow
for a safety margin (rotating stall or surge margin) in compression system
operation. However, to account for compression system uncertainties such
as system modeling errors, in-service changes due to aging, etc., and
compression system disturbances such as compressor speed fluctuations,
combustion noise, etc., operating at or below the rotating stall/surge margin
significantly reduces the efficiency of the compression system. In contrast,
active control can enhance stable compression system operation to achieve
peak compressor performance. However, compression system uncertainty
and compression system disturbances are often significant and the need for
robust disturbance rejection control is severe.
In order to develop control system design methodologies for compres-
sion systems, reliable models capturing th e intricate physical phenomena
of rotating stall and surge are necessary. A fundamental development in
compression system modeling for low speed axial compressors is the Moore-
Greitzer m odel given in [319]. Specifically, utilizing a one-mode expansion of
the disturbance velocity potential in the compression system and assuming
a nonlinear (cubic) characteristic for the compr essor performance map, the
authors in [319] develop a low-order, three-state nonlinear model involving
the mean flow in the compressor, the pressure rise, and the amp litude
of rotating stall. Starting from infi nitesimal perturbations in the flow
field the model captures the development of rotating stall and surge.
In particular, the model pr ed icts the experimentally verified subcritical
pitchfork bifurcation at the onset of rotating stall [311]. Extensions to the
Moore-Greitzer model that include blade row time lags and viscous transport