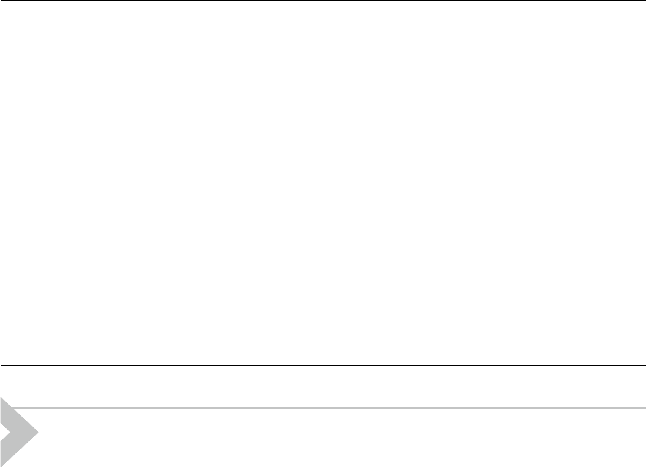
Hypo2000 þ 26O
2
! 22CO
2
þ 8H
2
O ðE8:5:5Þ
Solution:
1) A conversion reactor is used to carry out reactions (E8.5.1) to (E8.5.3) at
900
F and 20 psia. T he product stream is called Dist (Figure E8.5.1).
2) The Dist stream is split into Hypo-2000 as a coke stream and the other
products.
3) Air is injected at 100
F and 20 psia.
4) The mixed stream (reg) is sent to the regenerator reactor where coke is
combusted producing hot flue gases.
5) The product stream is sent to a fractionator.
A summary of the results for all streams is shown in Table E8.5.1.
8.16. New Technology
The major drive for FCC process improvements is the demand for
higher gases (LPG and olefins) and the decline in demand for residual oils.
Replacement of diesel fuels to gasoline will also drive FCC technology to
reduce its production in favour of lighter products. Environmental aspects
are being observed in developing new FCC unit. The following processes
have been developed and some have already been commercialised.
8.16.1. Deep Catalytic Cracking
DCC is a new FCC process using a new catalyst for heavy feed stocks to
give light olefins. The yield of olefins depends greatly on the type of
feedstock. Paraffenic feeds give the lightest propylene yield of 23 wt% and
6.9 wt% isobutylene (Hsu and Robinson, 2006).
8.16.2. Catalytic Pyrolysis Process
The catalytic pyrolysis process (CPP) is an extension of DCC but with
increased ethylene yield. The ratio of C
3
=
/C
2
=
can be adjusted by controlling
the operating conditions. C
3
=
can be produced up to around 20 wt% while
C
2
=
can be adjusted between 10 and 20 wt%. It is suggested to optimise the
use of crude oil as a petrochemical feedstock by using a combination of
steam cracking (SC) and catalytic pyrolysis (CPP) as shown in Figure 8.11
(Hsu and Robinson, 2006).
230 Chapter 8