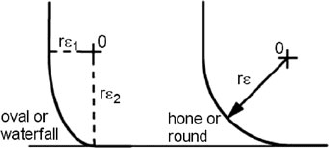
88 W. Grzesik
angles but cutting-edge configuration and its preparation also play a dominant role
in a machining success.
In general, the cutting-edge geometry is critical in hard machining because
tools with superior edge strength are required to withstand the large tool stresses
produced. As a result, tool cutting edges which are designed to cut hardened steels
are often equipped with a chamfer (sometimes double chamfer) between the rake
and clearance faces, termed by ISO the T-land and K-land respectively. The cham-
fer angle of –20° and the chamfer width of 0.1 (0.2) mm are typically selected. In
order to protect the cutting edges from microchipping, additional hones are made
as shown in Figure 3.1.
Because uniform edge micro-geometry along the corner radius causes exces-
sive ploughing at the minor cutting edge (a very low edge radius to uncut chip
thickness as shown in Figure 3.2 (a)) the PCBN tools with variable honed cutting
edges are implemented [3, 4]. As can be seen in the CAD model of variable
shaped cutting edge, the edge radius at points A, B and C decreases uniformly
from the major to minor cutting edges, i.e. r
ß A
>
r
ß B
>
r
ß C
. This causes a constant
uncut chip thickness to edge radius ratio to be maintained along the active part of
the corner.
Recently, wiper inserts, which combine the high feed capability and high-
quality surface finish produced by large round inserts, have gained popularity in
hard-machining applications. As shown in Figure 3.3 (a), multi-radii tool corner
contains a small smoothing part of the radius of r
bo
which is parallel to the feed
direction. Additionally, Figure 3.3 (b) shows a more universal design of a wiper
corner with both left- and right-handed wiper segments. By the application of such
a solid wiper insert (the Crossbill™ by Seco Tools [6]), it is possible to machine a
perfect radius with no deviation from a normal radius along with axial turning,
which utilizes the full wiper effect.
Figure 3.4 shows a unique new design of solid CBN inserts with a straight part
of the cutting edge blending into a wiper. As a result, the smaller approach angle
κ
r
reduces the depth of cut and provides constant chip thickness, so higher feed
rates up to 0.4
mm/rev can be applied. Figure 3.5 illustrates the micro-geometry of
a few of the inserts at a magnification of 50 times obtained by using field emission
scanning electron microscopy.
Figure 3.1 Profiles of honed cutting
edges for hard-machining applications [3]