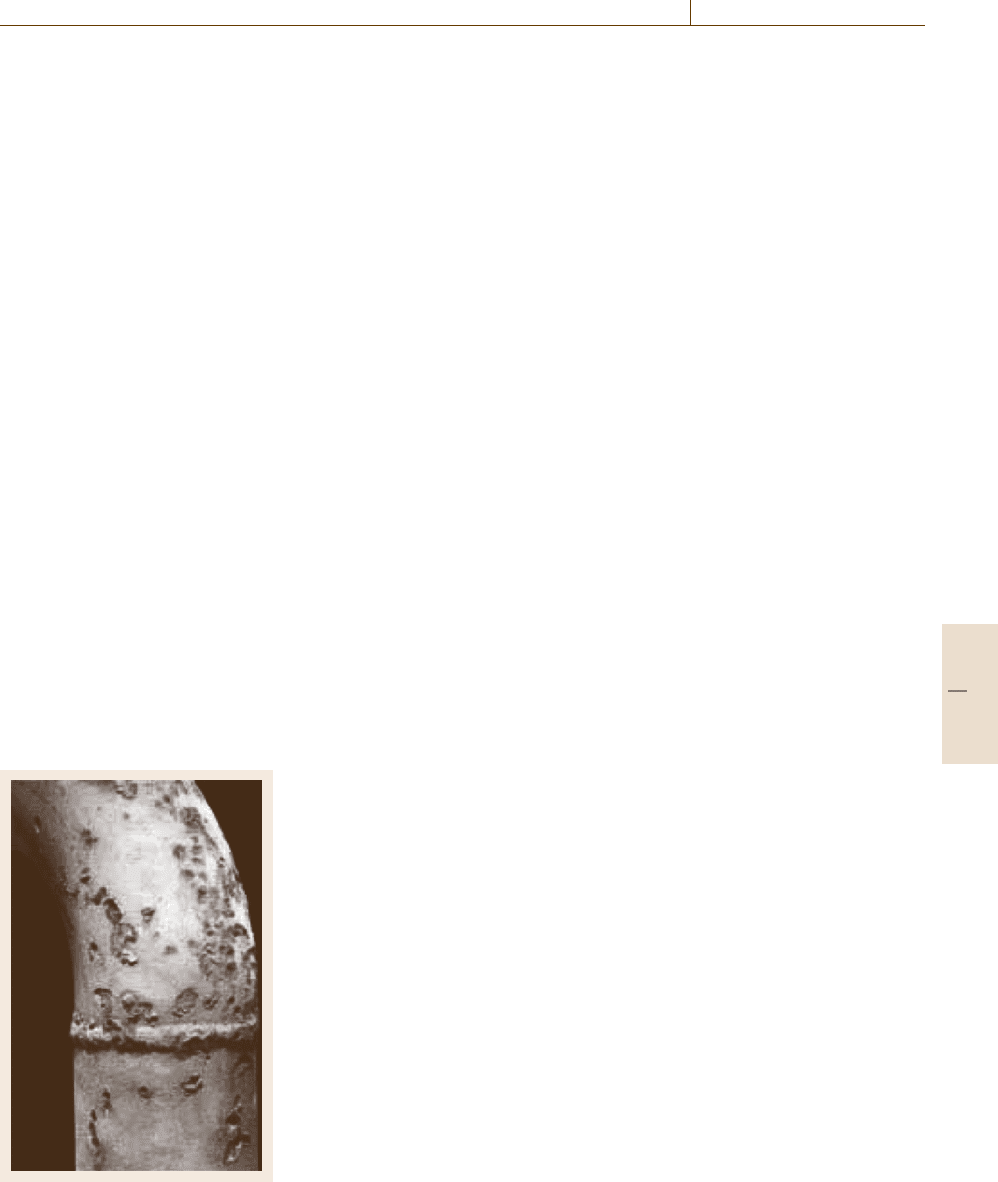
Performance Control 16.1 Nondestructive Evaluation 889
phenomena are of interest, or (ii) detection of cracks or
deformation is included.
The first point (i) can be described as integral vi-
sual inspection and the second point (ii) as specific or
selective visual inspection. If between the eye of the
inspector and the surface of the test object the opti-
cal path is not broken then a direct visual inspection is
performed (Fig. 16.1). Such inspection is either integral
or selective. Direct visual inspection means examina-
tion using eyesight and sometimes simple tools such as
artificial illumination. Selective visual inspection uses
additional equipment including hand lenses, mirrors,
optical microscopes and telescopes and, for the docu-
mentation of the inspection results, storage media such
as photography or cameras in combination with a mon-
itor. If inspection is carried out by the evaluation of
photographs, video films or by robotics an indirect or re-
mote visual inspection is performed (Fig. 16.2). Visual
inspection can be carried out in almost all areas where
preventive maintenance is required. Visual inspection is
the oldest and most common form of corrosion inspec-
tion, applied to surface corrosion, intergranular stress
corrosion, and some kinds of pitting. Several corrosion
phenomena are detectable using direct visual inspection
techniques. An example showing a corroded surface
is presented in Fig. 16.3. Clearly visible is the scarred
surface in the elbow region of the pipe. This exam-
ple illustrates that the visual technique is quick and in
most cases economical. Various types of failure are de-
tectable but the reliability of the inspection is highly
dependent on the skill and training of the examiner.
Fig. 16.3 Cor-
roded pipe
16.1.2 Ultrasonic Examination:
Physical Background
Sound travels in solids, liquids and gases with a velocity
depending on the mechanical properties of the material.
Imperfections such as cracks, pores or inclusions cause
sound-wave interactions which result in reflection, scat-
tering and general dampening of the sound wave [16.3–
6]. This dampening of the sound waves is responsible
for the distance traveled by the sound. In liquids sound
can travel large distances; on the other hand, in coarse-
grained solids the traveling distance may be only a few
centimeters due to scattering. Sound directions and the
estimation of the distance to the source are not easily
obtainable by simple methods. More precise techniques
are necessary to overcome these problems. This requires
the use of narrow sound beams.
In nondestructive evaluation (NDE) narrow sound
beams using short wavelengths can be formed when
the ultrasonic source size is much larger than the
wavelength. Nondestructive testing is carried out using
ultrasonic waves at high frequencies above the audible
range, higher than approximately 20 kHz and up to the
range of some hundred MHz.
Historically, the development of methods for ultra-
sonic materials testing in the industry started at the end
of the Second World War. Although the orientation of
bats using sound waves was an established phenom-
ena, the discovery of the piezoelectric effect by Jacques
and Pierre Currie 1880 and 1881 [16.3] was of critical
importance for the application of ultrasound. The the-
ory of sound propagation in solids was developed by
Lord Rayleigh between 1885 and 1910, as well as the
development of early electronic devices.
Sound-field generation and reception is performed
using special devices, so called ultrasonic transducer
or ultrasonic probes. The active sound-field genera-
tion tool is in the most cases a special ceramic with
piezoelectric properties. A piezoelectric material has the
characteristic that, if it is deformed by an external me-
chanical pressure, electric charges are produced on its
surface (Fig. 16.4). This effect was discovered in 1880
by the brothers Curie. The reverse phenomenon, ac-
cording to which such a material, if placed between
two electrodes, changes its form when an electric po-
tential is applied, was discovered soon afterwards in
1881 (Fig. 16.5). The first effect is referred to as the di-
rect piezoelectric effect, and the second as the inverse
piezoelectric effect. The direct effect is used for mea-
suring and the inverse effect for producing mechanical
pressures, deformations and oscillations.
Part D 16.1