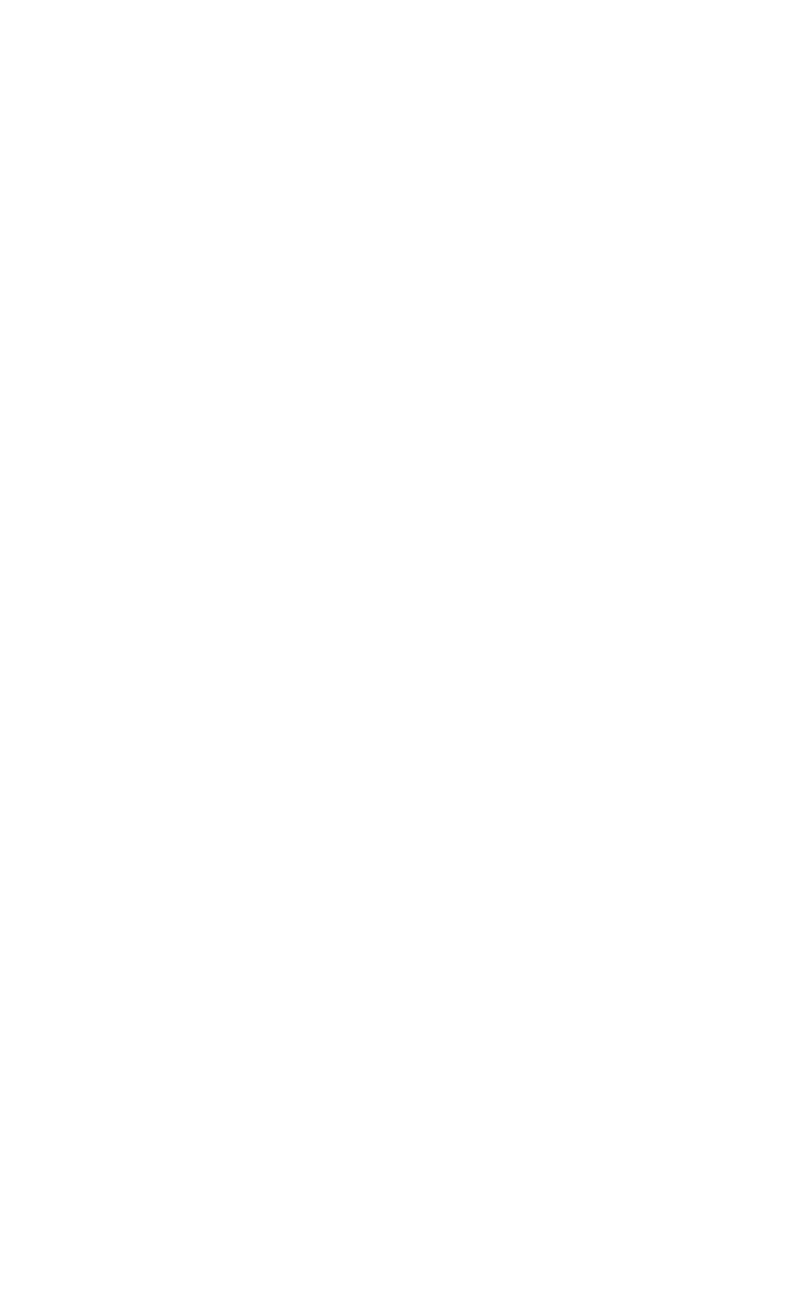
Near-Net Shape Forging and New Developments / 323
23.2.4 Process Variables in Forging
Figure 23.4 shows the various stages in forg-
ing, with the parameters affecting part attributes
and tolerances [Ishinaga, 1996]. The variable
factors (enclosed in square brackets) affect each
other and cause variations in the dimensions of
the forged part. The entire forging process is di-
vided into three stages:
●
The preprocessing stage addresses the vari-
ables related to the billet. One way to control
the part quality is to ensure minimum devi-
ation in each of the billet factors, such as
dimensions, flow stress, formability, etc.
●
The forging process, which encompasses all
the variables related to the forming process
(temperature, lubrication, etc.), tooling, and
equipment. Variations in the forging pressure
would affect the thickness of the forging due
to elastic deflection of the press and tools.
Off-center loading not only affects the ac-
curacy of the process but is also detrimental
to tool life.
●
The postprocessing stage deals with machin-
ing, surface finishing, or heat treatment of
the forged parts and affects the material
properties, surface conditions, or chemical
composition of the part.
The growing demands for precision cold-
forged products in the automotive industry led
to the development of economical means to
manufacture these parts. Apart from improve-
ments in forging processes, there has been con-
siderable progress in tooling and equipment de-
sign, materials engineering, and lubrication
techniques in order to produce precise compo-
nents. Some of these developments and future
trends are discussed in the subsequent sections.
23.3 Advances in Tool Design
In order to produce precision-forged parts,
factors related to the tooling, namely, elastic de-
flection, eccentricity, thermal expansion, etc.,
have to be considered during the process design
stage. This is especially true in the case of cold
forging, where precision die manufacturing is
necessary to ensure the production of parts to
close tolerances. The following factors have to
be considered in die manufacturing [Yoshimura
et al., 1997]:
●
Proper equipment and process to ensure high
accuracy
●
Proper design of die structure to achieve high
stiffness
●
Proper heat and surface treatments to elimi-
nate the heterogeneity of the die material
●
Proper control of heating conditions to main-
tain constant temperature at the die
Tool life is also a major factor to be consid-
ered while quoting a part. Since the cost of
manufacturing a die is considerable, simultane-
ous process design involving process planning
and die design are essential to ensure that con-
ditions such as loading pressure, stress concen-
tration, etc. remain within the allowable limits
of die performance. Thus, tool wear, tool frac-
ture, and process failure have to be considered
for cost reduction.
23.3.1 Enclosed- or Trapped-Die Forging
Enclosed-die forging uses multiple-action
tooling as punches press the material in a pre-
enclosed die to fill in the die space (Fig. 23.5).
By controlling the motion of rams, metal flow
can be controlled to obtain the optimum defor-
mation. The ram motions for upper and lower
punches can be set as synchronous, asynchro-
nous, or with back pressure to reduce forming
load or to improve the filling of material. Some
of the advantages of enclosed-die forging are:
●
The ability to form complex shapes in one
process
●
Elimination of flash, thus resulting in mate-
rial savings. Since parts are formed to close
dimensional tolerances, subsequent machin-
ing operations are either reduced or, in some
cases, eliminated.
●
Low forming load is available where the area
penetrated by the punch is relatively small.
A Japanese tool supplier has recently devel-
oped a special die set for forging radially ex-
truded parts and a family of bevel gears (Fig.
23.6 and 23.7) [Yamanaka et al., 2002]. The ad-
vantages obtained from this die set were high
productivity, easy installation in nearly all
presses, the requirement of only compressed air,
and low initial cost.
A similar concept in die design, developed
earlier, incorporates a pantograph, as shown in
the schematic in Fig. 23.8 [Yoshimura et al.,
1997 and 2000]. Hydraulic pressure generated
by an external hydraulic unit and an accumulator
is used for closing the upper and lower die to
form the die cavity. The die-closing pressure is
adjustable. However, if this pressure is too low,