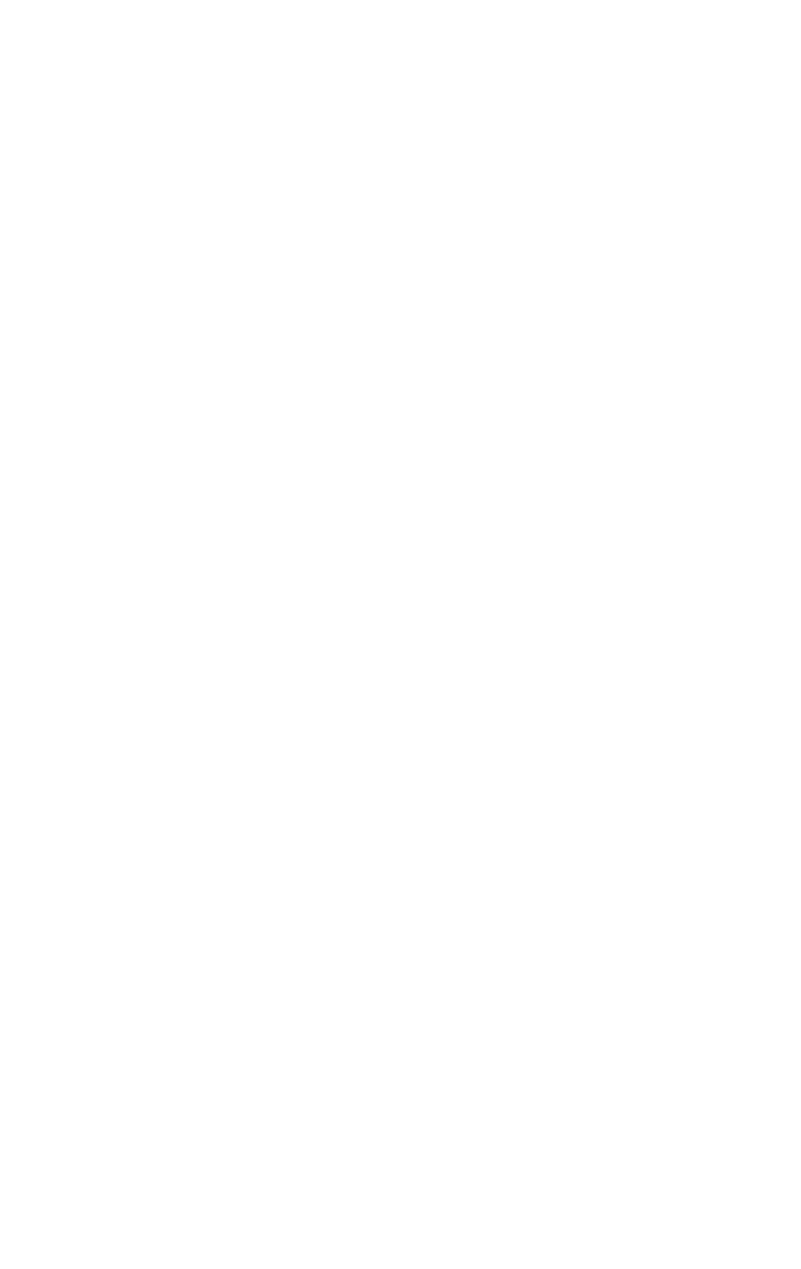
316 / Cold and Hot Forging: Fundamentals and Applications
22.8.3 Hot Precision
Forging—A Case Study
Hot precision forging of complex shapes is
the focus of many manufacturers. The tolerances
on these parts are especially critical. Therefore,
die wear is exceedingly detrimental to these pro-
cesses. Thus, prediction of die wear and en-
hancement of die life is very important to these
manufacturers.
Experimental Wear Measurement. Mea-
surement of die wear for the hot precision forg-
ing process was carried out at the IFUM at the
University of Hannover in Germany, under the
conditions given in Table 22.5 [Bobke, 1991,
and Luig, 1993].
Figure 22.30 shows the precision forging die
used in the experiments. Typical wear profiles
after forging are shown in Fig. 22.31. The ex-
perimental wear depths for three different lubri-
cants are summarized in Fig. 22.32.
Analytical Wear Prediction. It was assumed
that abrasive wear was the dominant wear mech-
anism in hot precision forging. Therefore, the
wear model in Eq 22.5 was used [Dahl et al.,
1999].
Figure 22.33 shows the FEM model of the hot
precision forging process. On completion of
each step, the parameters needed for the die wear
model (Eq 22.5) were extracted from the FEM
simulation, and the wear depth was predicted, as
discussed previously. Based on typical experi-
mental values for two-body abrasion, the wear
coefficient was assumed to be K
abr
⳱ 0.02 [Dahl
et al., 1999].
The maximum predicted die wear and the
maximum measured die wear both occurred at
the corner of the upper die (Fig. 22.31, mea-
surement location 18). In general, the model pre-
dicted that die wear increases with decreasing
corner radius, decreases with increasing friction
factor, and increases with decreasing die hard-
ness (i.e., different materials have different
temperature-hardness curves). This illustrates
the advantage of being able to predict die wear.
It is not intuitive that die wear would decrease
with increasing friction factor. In the case of the
valve extrusion, it was shown that die wear in-
creases with increasing friction factor because
of the increased pressure developed on the die.
In this case, die wear decreases because in-
creased friction acts to decrease the sliding
length [Dahl et al., 1999].
REFERENCES
[Altan et al., 1983]: Altan, T., Oh, S., Gegel,
H., Metal Forming Fundamentals and Appli-
cations, American Society for Metals, 1983.
[Artinger, 1992]: Artinger, I., “Material Science
and Tool-Life,” Budapest, 1992 (in Hungar-
ian).
[Aston et al., 1969]: Aston, J., and Barry, E.,
“A Further Consideration of Factors Affect-
ing the Life of Drop Forging Dies,” J. Iron
Steel Inst., Vol 210 (No. 7), July 1969, p 520–
526.
[Bay, 2002]: Bay, N., class notes, Technical
University of Denmark, 2002.
[Bobke, 1991]: Bobke, T., “Phenomenon of
Edge Layer at Sealing Process of Drop Forge
Tools,” No. 237, IFUM, University of Han-
nover, 1991.
[Dahl et al., 1998]: Dahl, C., Vazquez, V., Al-
tan, T., “Effect of Process Parameters on Die
Life and Die Failure in Precision Forging,”
Report No. PF/ERC/NSM-98-R-15, Engi-
neering Research Center for Net Shape Manu-
facturing, April 1998.
[Dahl et al., 1999]: Dahl, C., Vazquez, V., Al-
tan, T., “Analysis and Prediction of Die Wear
in Precision Forging Operations,” Report No.
PF/ERC/NSM-99-R-21, Engineering Re-
search Center for Net Shape Manufacturing,
May 1999.
[Doege et al., 1996]: Doege, E., Seidel, R., and
Romanowski, C., “Increasing Tool Life
Quantity in Die Forging: Chances and Limits
of Tribological Measures,” NAMRC, 1996.
[Hannan et al., 2001]: Hannan, D., Ngaile, G.,
Altan, T., “Elimination of Defects and Im-
provement of Tool Life in Cold Forging—
Case Studies,” New Developments in Forging
Conference (Stuttgart, Germany), Institute for
Metal Forming Technology (IFU), May 2001.
[Hettig, 1990]: Hettig, A., “Influencing Vari-
ables of Tool Fracture at Impact Extrusion,”
No. 106, Reports from the Institute of Metal
Forming, University of Stuttgart, Springer,
1990.
[Kesavapandian et al., 2001]: Kesavapandian,
G., Ngaile, G., Altan, T., “Die Wear in Pre-
cision Hot Forging—Effect of Process Param-
eters and Predictive Models,” Report No. PF/
ERC/NSM-01-R-42, Engineering Research
Center for Net Shape Manufacturing, Aug
2001.