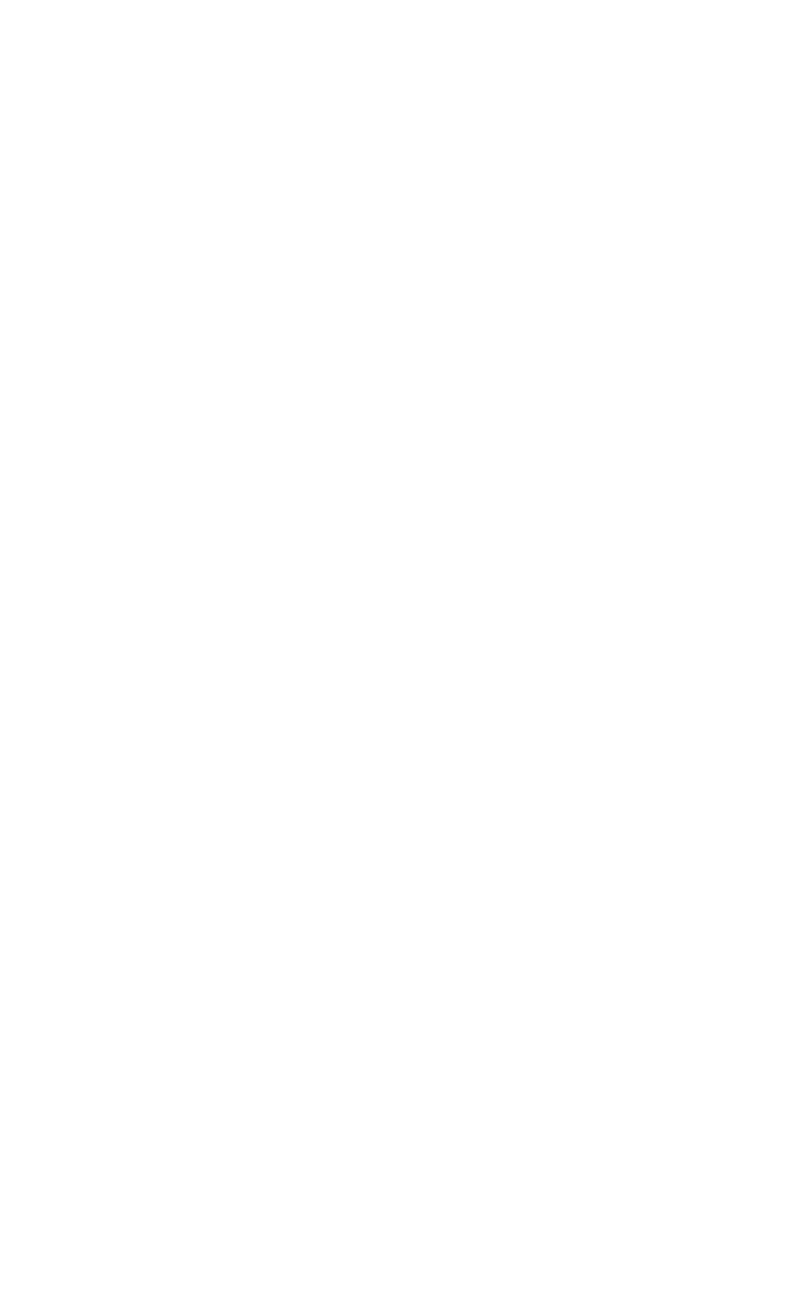
Isothermal and Hot-Die Forging / 259
machines, such as hammers or mechanical, hy-
draulic, or screw presses. Parts with complex ge-
ometries are forged in impression dies that have
the shape of the desired part. This may be done
in one step or a sequence of steps (i.e., preform-
ing and blocking), depending on the part com-
plexity. This process results in very high die
stresses and hence calls for the material to be
forged at elevated temperatures in order to re-
duce the flow stress, increase formability, and
thus reduce die stresses. During hot forging, the
heat transfer from the hot material to the colder
dies can result in die chilling. Dies are thus nor-
mally heated to approximately 600 to 800 ⬚F
(315 to 425 ⬚C) to reduce the heat transfer. Con-
ventional die materials do not allow the use of
temperatures higher than 800 ⬚F (425 ⬚C), since
they lose their strength and hardness above this
temperature range [Semiatin et al., 1983]. Alu-
minum alloys are generally isothermally forged,
since the dies are readily heated to the same tem-
perature range as the material (approximately
800 ⬚F, or 425 ⬚C). Since isothermal forging of
aluminum alloys is a well-established state-of-
the-art process, it is more appropriate to concen-
trate on high-temperature alloys such as titanium
and nickel.
Forging of steels and high-temperature alloys
can be an expensive process due to the preform-
ing and blocking operations needed to achieve
the desired part geometry, especially in aero-
space forging. This industry produces a rela-
tively small number of parts, which does not jus-
tify the high die costs. Thus, it is considered
economical to forge a part with high machining
allowances to reduce die costs while simulta-
neously increasing machining costs and material
losses. This approach is, however, not suitable
for titanium and nickel alloys that are more ex-
pensive in comparison to steel and aluminum.
This cost ratio has been a driving factor for the
development of isothermal (dies and workpiece
at the same temperature) and hot-die (die tem-
perature close to that of the workpiece) forging
methods.
Isothermal and hot-die forging offer the fol-
lowing advantages [Semiatin et al., 1983]:
●
Closer tolerances than conventional forging
due to elimination of die chilling. Reduction
of machining costs and material losses.
These forging processes allow for smaller
corner and fillet radii, smaller draft angles,
and smaller forging envelope, consequently
leading to materials savings and a reduced
forging weight (Fig. 20.1 and 20.2).
●
Elimination of die chilling also results in re-
duction of preforming and blocking steps,
thus reducing die costs.
●
Since die chilling is not a problem, slow de-
formation speeds can be used (e.g., a hy-
draulic press). This reduces the strain rate
and flow stress of the forged material. Due
to reduction of forging pressures, larger parts
can be forged using existing equipment.
Figure 20.3 shows a comparison between iso-
thermal forging and other conventional methods
of producing a typical rib-web-type aircraft
structural component.
20.5 High-Temperature Materials for
Isothermal and Hot-Die Forging
An in-depth understanding of the plastic prop-
erties of the forging material is extremely crucial
for the design of an isothermal forging process,
since the selection of the other elements, such as
equipment, die material, and lubricants, is based
on this knowledge.
At hot forging temperatures (Tⱖ
T
m
, where
T
m
is the melting point or solidus temperature
of the material), the flow stress is usually a func-
tion of strain rate, except at very low strains.
Consequently, the deformation behavior of a
material is best understood by examining the
flow stress dependence on strain rate [Chen et
al., 1980, and Greenwood et al., 1978]. The de-
pendence of the flow stress on temperature is
minimal at very low (creep) as well as high (con-
ventional hot forging) strain rates. At interme-
diate strain rates, however, the flow stress de-
pendence on is often large, and it is in this¯e
region that superplastic behavior is predominant
(Fig. 20.4). The high strain-rate sensitivity of su-
perplastic materials promotes die filling and re-
sists localized plastic deformation, making these
materials extremely suitable for isothermal and
hot-die forging. Also, the reduction of flow
stress with decreasing strain rate lowers the forg-
ing loads, thus making it possible to form a part
isothermally with a smaller press than in con-
ventional hot forging. Isothermal forging also
reduces the number of forging steps and ancil-
lary operations that are necessary in conven-
tional forging.
20.5.1 Titanium Alloys
Titanium alloys are among the most com-
monly used materials for isothermal and hot-die
0.6