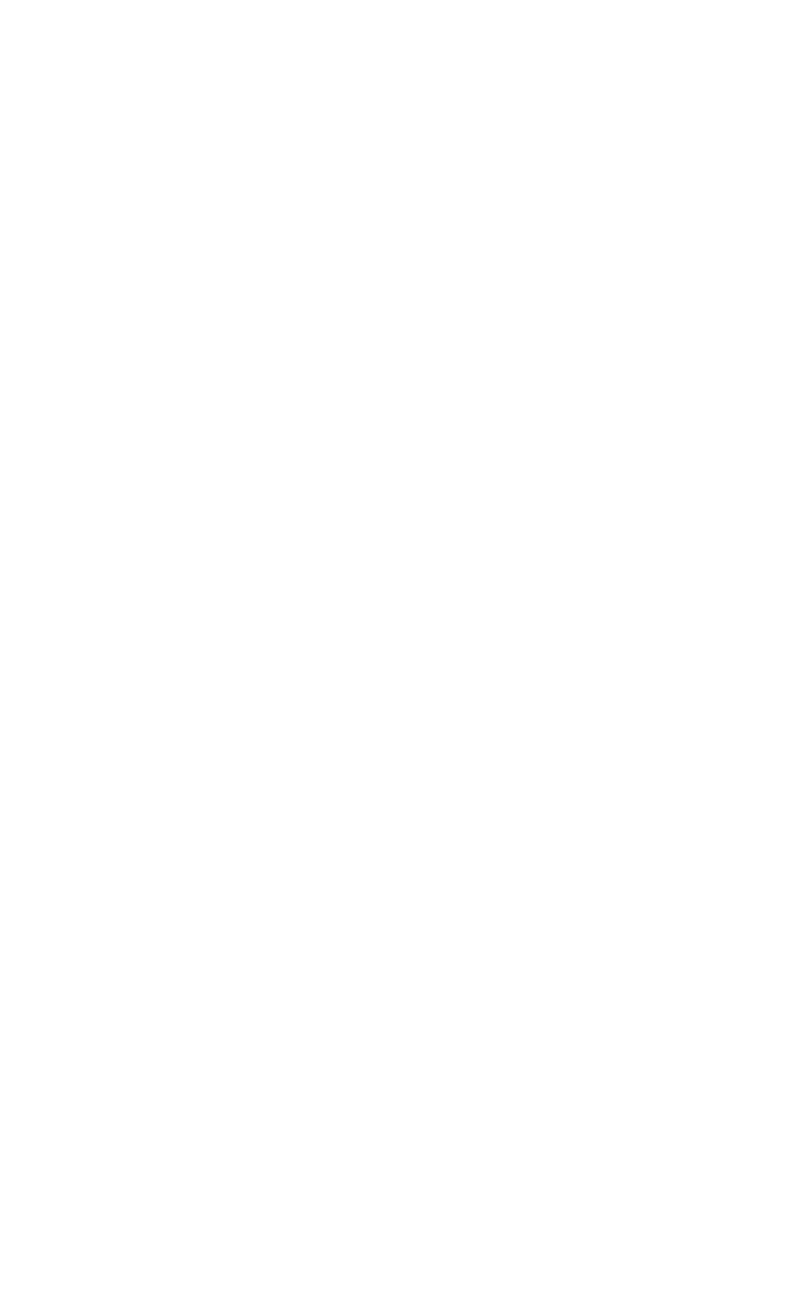
Cold and Warm Forging / 227
In forward rod extrusion, wear of the punch
is normally not a problem. Compressive stresses
range up to 350 ksi (2413 MPa) and sometimes
slightly more. In can extrusion, the punch is sub-
jected to compressive and bending load as well
as heavy wear, which increases the temperature
at the punch nose, especially in high-speed
presses. During stripping, tensile stresses occur.
In ironing, the punch pushes the workpiece
through the die and forms its internal surface.
Depending on size, shape, loading, and wear,
both tool steels and cemented carbides may be
selected as tool materials.
17.11.2 Die, Die Insert, Container, Case
(Combined Case and Die Insert)
The die is the portion of the tool assembly that
contains the workpiece and forms the external
surfaces. The choice of the material depends on
the maximum internal pressure and fatigue as
well as the toughness and wear-resistance re-
quirements.
Normally, dies are reinforced by one or more
stress rings. Depending on the stress state, prin-
cipal designs used in the industry are as follows:
●
Die
●
Die with one-piece insert
●
Die with axially split insert
●
Die with transversely split insert
Depending on size and shape, both tool steels
and cemented carbides may be selected for the
die insert.
17.11.3 Counter Punch
The counter punch forms the base shape and
is usually used to eject the workpiece from the
die. In both can extrusion and coining or sizing,
the counter punch is subjected to compressive
stresses similar to those occurring in punches.
Both tool steels and cemented carbides may be
selected.
17.11.4 Heading Punch/Heading Die
The heading punch upsets the head of the
workpiece. The heading die contains the shank
and forms the underhead surface of the work-
piece. Choice of the tool material and its heat
treatment depends on the compressive stresses
(up to 300 ksi, or 2068 MPa, and more), section
size, and the demand for wear resistance and
toughness. Besides tool steels, for a range of
small and medium section sizes, cemented car-
bides may be used when long runs demand high
wear resistance.
17.11.5 Mandrel (Pilot)
The mandrel or pilot is that part of the punch
assembly that enters a hollow billet and forms
the inside wall. The mandrel is subjected to wear
and high tensile stresses, and therefore, the
choice of material is aimed at properties such as
wear resistance and/or high yield strength. Due
to high tensile stresses, tool steels are normally
used.
17.11.6 Stress Rings
The stress rings form the intermediate and
outer portions of the die assembly to prevent the
die from bursting. The tensile stresses will
amount to 200 ksi (1379 MPa) and more. Nor-
mally, tool steels are used.
17.11.7 Pressure Pads
The pressure pad is the block of material that
supports and spreads the load behind the pad or
die. Sufficient thickness is important in order to
spread the load properly and to avoid bending.
An extreme degree of parallelism and square-
ness is essential. The tool material should pro-
vide high compressive strength up to 220 ksi
(1517 MPa). Normally, tool steels are used.
17.11.8 Ejector
The ejector is the part of the tooling that ejects
the workpiece from the die, usually without tak-
ing part in the forming operation. The choice of
the material depends on the section used and the
ejection pressure. Normally, tool steels are used.
17.12 Punch Design for Cold Forging
Figure 17.15 shows some punches and man-
drels used for solid and hollow forward extru-
sion.
The design process for punches and mandrels
can be divided into the following stages:
●
Determining the forming load
●
Deciding the overall shape and proportions
of the tool. For can extrusion, the detailed
shape of the punch nose is to be determined.
●
Choosing an appropriate tool material, con-
sidering the stresses, manufacturability, tool
life, availability, and costs