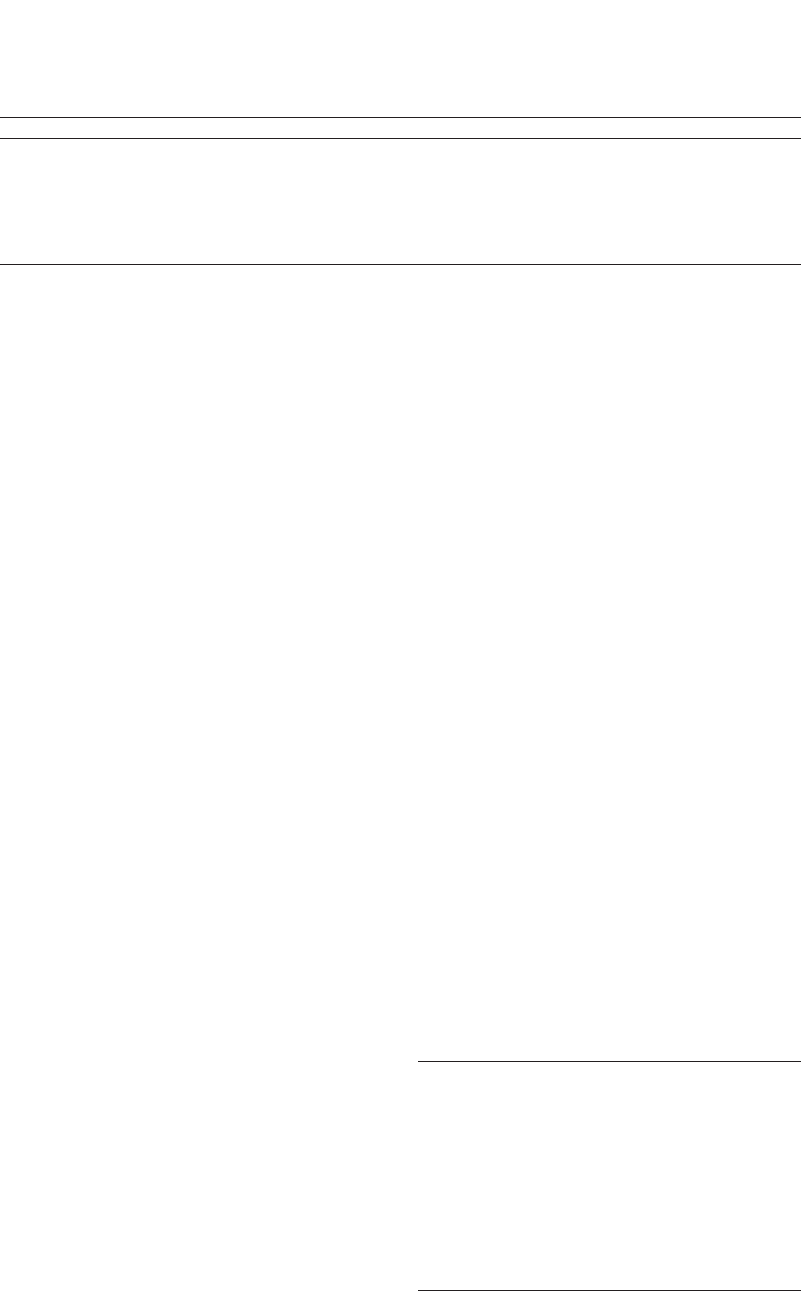
214 / Cold and Hot Forging: Fundamentals and Applications
Table 17.2 Typical procedure for phosphating
and lubricating billets of carbon and low-alloy
steels for cold extrusion
1. Degrease and clean slugs in a hot alkaline solution for 1 to 5
min at 151 to 203 F (66 to 95 C).
2. Rinse in cold water.
3. Remove scale, usually by pickling.
4. Rinse in cold water.
5. Rinse in neutralizing solution if a pickling process was used.
6. Dip in a zinc phosphate solution (usually of a proprietary type)
for approximately 5 min at 180 to 203 F (82 to 95 C) to
develop a uniform coating of appropriate thickness.
7. Rinse in cold water; neutralize if necessary.
8. Lubricate the slugs, usually with stearate soap but sometimes
with other types of lubricants.
9. Air dry the slugs to obtain a thin, adherent coating of lubricant
adsorbed on the zinc phosphate coating.
Table 17.1 Properties of aluminum alloys suitable for cold forging [ICFG, 2002]
Aluminum alloy Heat treatable Strength Elongation Corrosion resistance Machinability Weldability
1050 No * **** **** * ****
3103 No ** * **** * ****
5056 No *** ** **** ** **
2014 Yes *** ** * *** *
6061 Yes *** *** *** ** ****
7075 Yes **** ** ** *** *
Note: * ⳱ poor; **** ⳱ best
Materials for cold forging are supplied as
rolled or drawn rod or wire as well as in the form
of sheared or sawed-off billets. The dimensions,
weight, and surface finish of the sheared (or
sawed) billet or preform must be closely con-
trolled in order to maintain dimensional toler-
ances in the cold forged part and to avoid ex-
cessive loading of the forging press and tooling.
17.4 Billet Preparation and
Lubrication in Cold
Forging of Steel and Aluminum
By far, the largest area of application for cold
forging is the production of steel parts. Cold
forging plants usually receive small-diameter
material in coils and large-diameter stock in
bars. In very large-volume production, horizon-
tal mechanical presses, called headers or upset-
ters, are used. The coil, coated with lubricant, is
fed into the machine, where it is sheared and
forged in several steps. In forging of relatively
small production lots, vertical presses are used,
and individual billets (after being lubricated) are
fed into the first die station. Billet volume or
weight is closely controlled, and it is desirable
to obtain square billet faces during shearing or
sawing [Herbst, 1967].
In cold forging, the lubricant is required to
withstand high pressures, on the order of 280 ksi
(1930 Mpa) in extrusion of steel, so as to avoid
metal-to-metal contact between the tool and the
extruded material. In cold forging of low-carbon
and low-alloy steels, it is accepted practice to
coat the surface of the billet or coil with a lu-
bricant carrier. This zinc phosphate coating pro-
vides a good substrate for lubricants that with-
stand high forming pressures. The phosphating
and lubricating steps given in Table 17.2 are al-
most universally employed for cold extrusion of
steels. The success of the zinc phosphatizing
treatment is influenced by the composition of the
steel, especially the chromium content. Conse-
quently, special procedures and other conversion
coatings, such as oxalates, are preferred for aus-
tenitic stainless steels. Stearate-type soaps,
which adhere tenaciously to the phosphate coat-
ings, are commonly used as lubricants for forg-
ing and extrusion of steel at room temperature.
Solid lubricants such as MoS
2
and graphite have
proved to be beneficial under severe forging
conditions, where surface generation and form-
ing pressures are large [Doehring, 1972].
Lubrication for cold forging of aluminum
may be divided into two categories:
●
Lubrication without conversion coatings
●
Lubrication with a conversion coating
The lubricants applied without conversion
coatings are oil, grease, or alkali stearates (es-
pecially zinc stearate). The most common con-
version coatings are calcium aluminate and alu-
minum fluoride coatings. In both cases, the
conversion coating is combined with a lubricant,
normally zinc stearate. It is essential that the slug
surfaces are completely clean when applying the
conversion coating. This requires careful de-
greasing and pickling of the surface before coat-
ing [Bay, 1997, and Bay, 1994].
The types of alloys and the surface expansion
have a major influence on the choice of the lu-