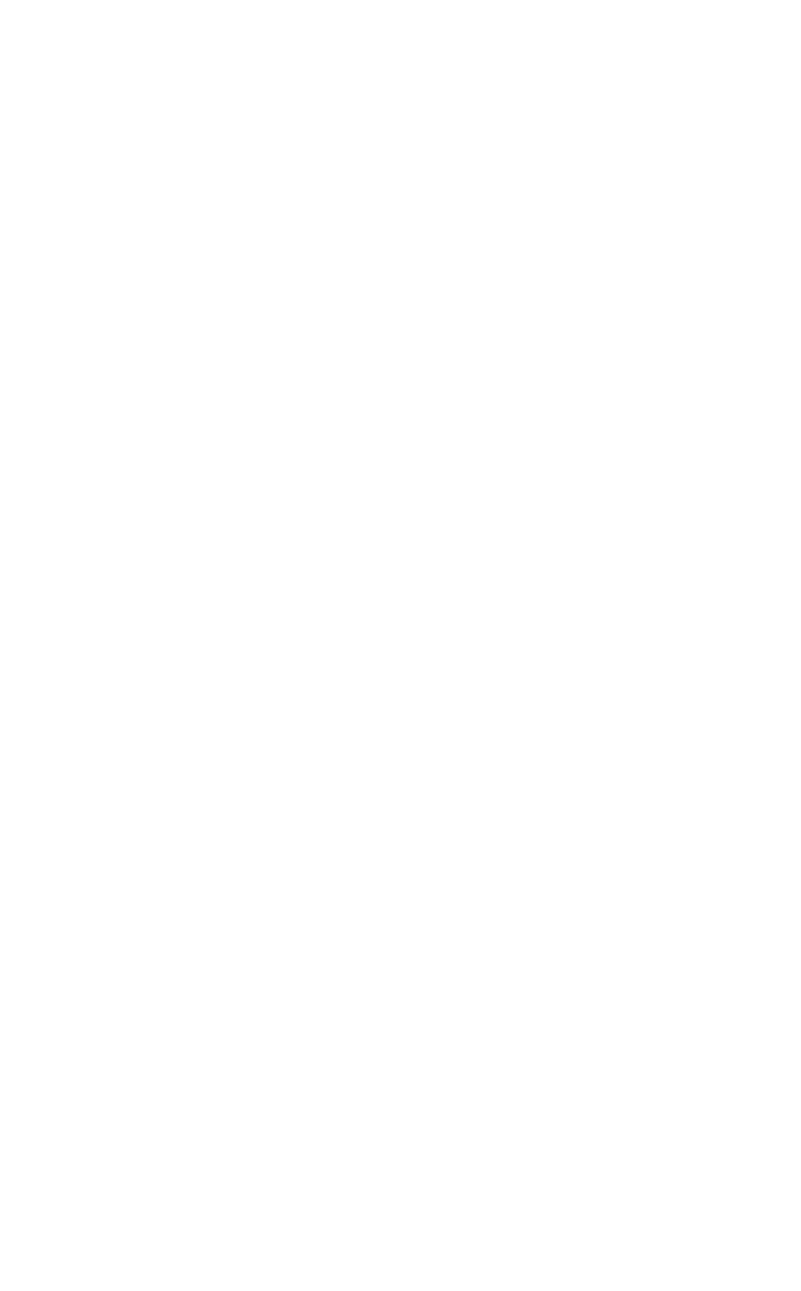
196 / Cold and Hot Forging: Fundamentals and Applications
16.3.3 Tool and Workpiece
Material Properties
In order to accurately predict the metal flow
and forming loads, it is necessary to use reliable
input data. The stress-strain relation or flow
curve is generally obtained from a compression
test. However, the test is limited in achievable
strains. In order to obtain the flow stress at large
strains and strain rates, the torsion test can be
used or, alternatively, the compression data is
extrapolated with care.
In most simulations, the tools are considered
rigid; thus, die deformation and stresses are ne-
glected. However, in precision forging opera-
tions, the relatively small elastic deformations of
the dies may influence the thermal and mechan-
ical loading conditions and the contact stress dis-
tribution at the die/workpiece interface. Thus,
die stress analysis is a crucial part of process
simulation to verify the die design and the forg-
ing process parameters.
16.3.4 Interface Conditions
(Friction and Heat Transfer)
The friction and heat-transfer conditions at
the interface between the die and the billet have
a significant effect on the metal flow and the
loads required to produce the part. In forging
simulations, due to the high contact stresses at
the interface between the workpiece and the die,
the constant shear friction factor gives better re-
sults than the coulomb friction coefficient.
The most common way to determine the shear
friction factor in forging is to perform ring com-
pression tests. From these tests, it is possible to
estimate the heat-transfer coefficient, flow stress
and friction as a function of temperature, strain
rate, strain, and forming pressure, as discussed
in Chapter 6, “Temperatures and Heat Transfer.”
Friction factors measured with the ring com-
pression test, however, are not valid for preci-
sion forging processes (hot, warm, and cold)
where the interface pressure is very high and the
surface generation is large. The friction condi-
tions change during the process due to changes
in the lubricant and the temperature at the die/
workpiece interface. In such applications, the
double cup extrusion test is recommended for
estimation of the friction factor, as discussed in
Chapter 7, “Friction and Lubrication.”
16.3.5 Material Parameters
The closed-die hot forging modeling is a cou-
pled heat-transfer and deformation simulation.
Material parameters that relate to both heat
transfer and deformation need to be defined. The
material parameters commonly used for heat-
transfer modeling are the thermal conductivity,
heat capacity, and emissivity of the workpiece
and die materials. These parameters are usually
defined as a function of temperature, The flow
stress of the workpiece material is very impor-
tant for the correct prediction of metal flow be-
havior. It is usually defined as a function of
strain, strain rate, temperature, and possible
starting microstructures. The Young’s modulus,
the Poisson’s ratio as a function of temperature,
and the thermal expansion of the die materials
are important parameters for die stress analysis.
16.4 Characteristics of
the Simulation Code
16.4.1 Mesh Generation and
Automatic Remeshing
In forging processes, the workpiece generally
undergoes large plastic deformation, and the
relative motion between the deforming material
and the die surface is significant. In the simu-
lation of such processes, the starting mesh is
well defined and can have the desired mesh den-
sity distribution. As the simulation progresses,
the mesh tends to get distorted significantly.
Hence, it is necessary to generate a new mesh
and interpolate the simulation data from the old
mesh to the new one to obtain accurate results.
Automated mesh generation (AMG) schemes
have been incorporated in commercial FE codes
for metal forming simulations. In DEFORM,
there are two tasks in AMG: 1) determination of
optimal mesh density distribution and 2) gen-
eration of the FE mesh based on the given den-
sity. The mesh density should conform to the
geometrical features of the workpiece at each
step of deformation [Wu et al., 1992]. In order
to maximize the geometric conformity, it is nec-
essary to consider mesh densities that take into
account the boundary curvature and local thick-
ness.
In DEFORM, two-dimensional (2-D) simu-
lations use quadrilateral elements, whereas
three-dimensional (3-D) simulations use tetra-
hedral elements for meshing and automatic re-
meshing [Wu et al., 1996]. With this automatic
remeshing capability, it is possible to set up a
simulation model and run it to the end with very
little interaction with the user.