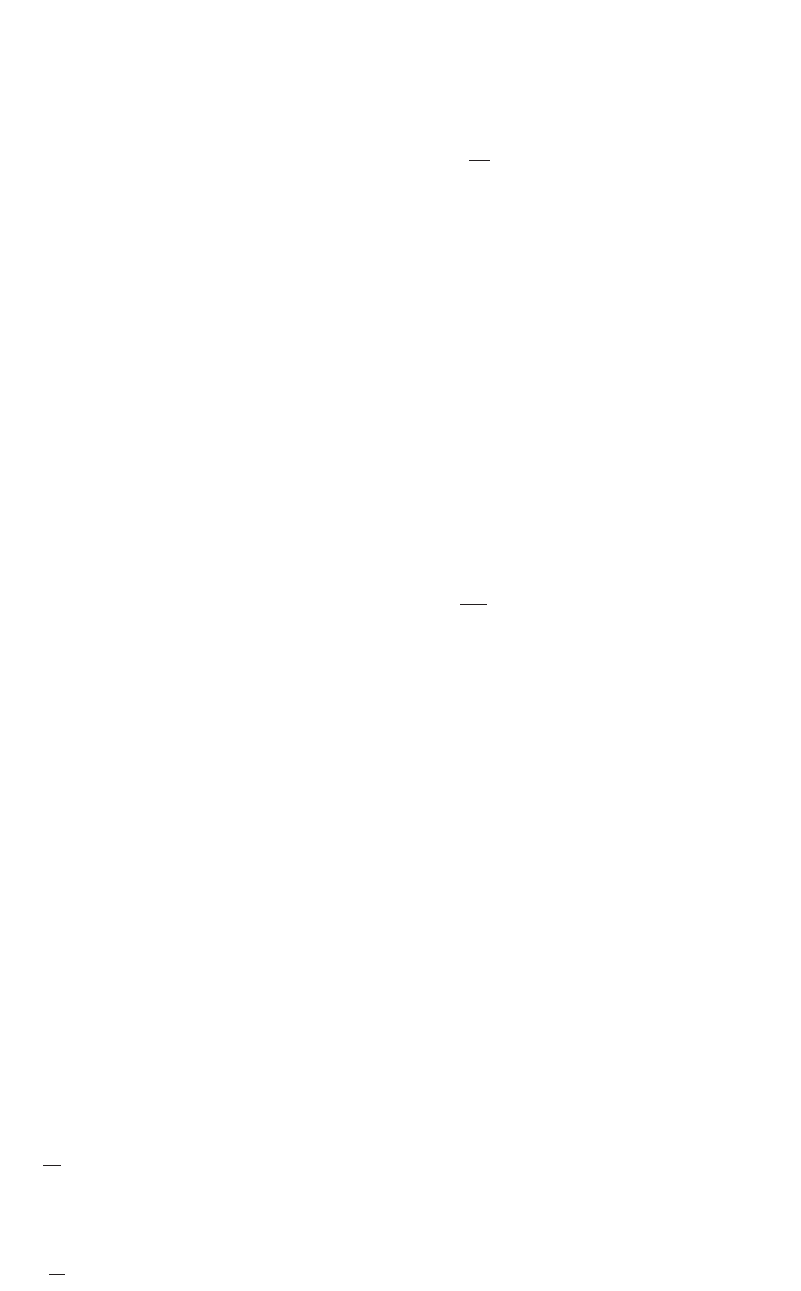
Process Design in Impression-Die Forging / 165
between the surface-to-volume ratio of a forging
and the difficulty of producing the forging.
The ease of forging more complex shapes de-
pends on the relative proportions of vertical and
horizontal projections on the part. Figure 14.7 is
a schematic representation of the effects of
shape on forging difficulties. Parts “C” and “D”
would require not only higher forging loads but
also at least one more forging operation than
parts “A” and “B” to ensure die filling.
As shown in Fig. 14.8, the majority of forg-
ings can be classified into three main groups
[Spies, 1959]:
●
Compact shape, spherical and cubical shape
(class 1)
●
Disc shape (class 2)
●
Oblong shape (class 3)
The first group of compact shapes has the
three major dimensions, namely, the length (l),
width (w), and height (h) approximately equal.
The number of parts that fall into this group is
rather small.
The second group consists of disk shapes, for
which two of the three dimensions (length and
width) are approximately equal and are larger
than the height (h). All the round forgings be-
long to this group, which includes approxi-
mately 30% of all the commonly used forgings.
The third group of forgings consists of long
shapes, which have one dimension significantly
larger than the other two (l b ⱖ h).
These three basic groups are further subdi-
vided into subgroups depending on the presence
and type of elements subsidiary to the basic
shape. This “shape classification” is useful for
practical purposes, such as for estimating costs
and for predicting preforming steps. This
method is, however, not entirely quantitative and
requires some subjective evaluation based on
past experience.
A quantitative value called the “shape diffi-
culty factor” has been suggested by Teterin et
al., 1968, for expressing the geometrical com-
plexity of round forgings (having one axis of
rotational symmetry). A “longitudinal shape fac-
tor,” ␣, is defined as:
X
f
␣ ⳱ (Eq 14.1)
X
c
with
2
P
X ⳱ (Eq 14.2)
f
F
and
2
P
c
X ⳱ (Eq 14.3)
c
F
c
where P is the perimeter of the axial cross sec-
tion of the forging, F is the surface area of the
axial cross section of the forging (surface that
includes the entire axis of symmetry), P
c
is the
perimeter of the axial cross section of the cyl-
inder that circumscribes the forging, and F
c
is
the surface area of the axial cross section of the
cylinder that circumscribes the forging. Because
the circumscribing cylinder has the maximum
diameter and the maximum height of the forg-
ing, the factor ␣ represents a comparison of the
shape of the forging with that of the cylinder.
On round forgings, bosses and rims placed
farther from the center are increasingly more dif-
ficult to forge. Therefore, a “lateral shape fac-
tor,” b, is defined as:
2R
g
b ⳱ (Eq 14.4)
R
c
where R
g
is the radial distance from the sym-
metry axis to the center of gravity of half of the
cross section, and R
c
is the maximum radius of
the forged piece, which is equal to the radius of
the circumscribing cylinder.
A “shape difficulty factor,” S, incorporating
both the longitudinal and lateral factors is de-
fined as:
S ⳱ ␣b (Eq 14.5)
The factor S expresses the complexity of a
half cross section of a round forging with respect
to that of the circumscribing cylinder. In round
forgings, during the forging operation, the ma-
terial is moved laterally down (toward the ends
of the cylinder) from the center, which is con-
sidered to be at the “neutral axis.” In a nonsym-
metric forging the material is still moved out
laterally from the “neutral surface.” Thus, once
this neutral surface is defined, a “shape difficulty
factor” can also be calculated in nonsymmetric
forgings.
14.4 Design of Finisher Dies
Using the shape complexity and the forging
material as guidelines, the forging process en-