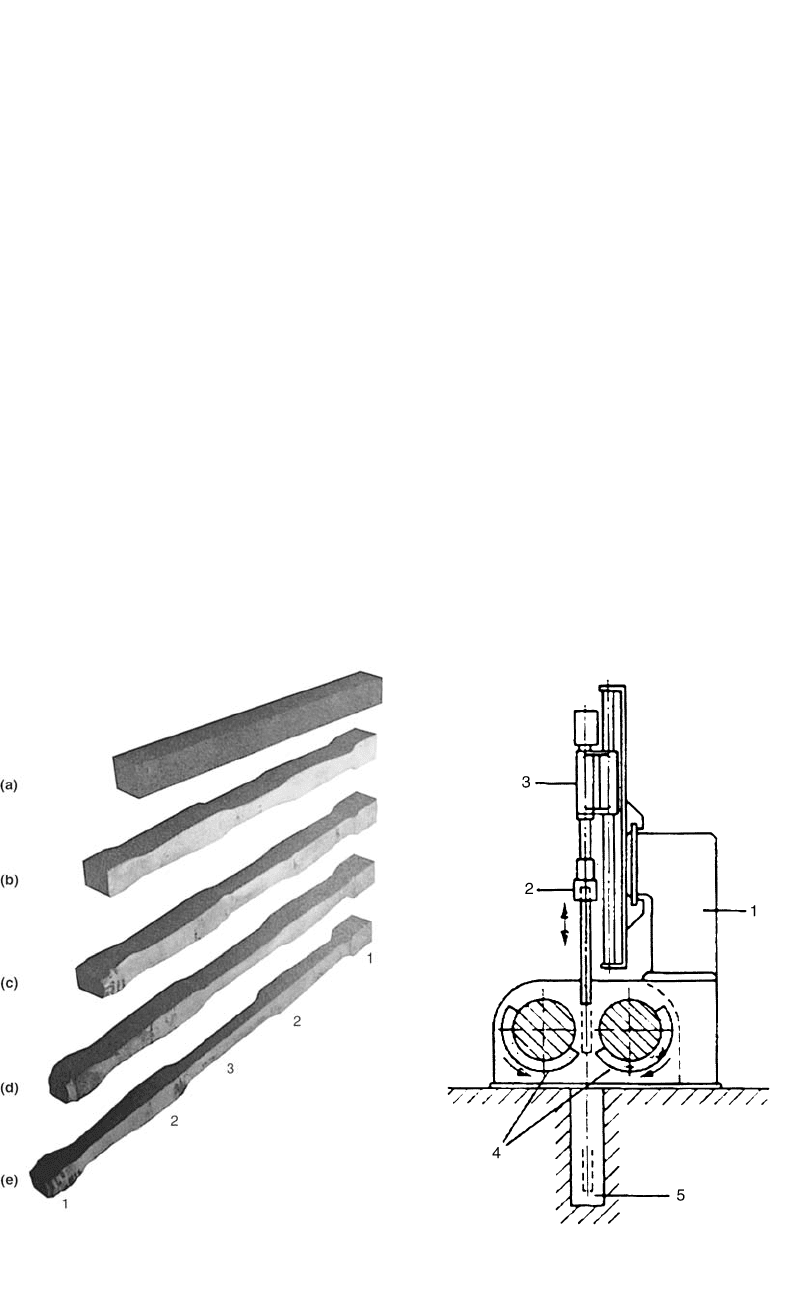
Special Machines for Forging / 143
tinuously fed between the gripping electrodes
(b), thus the metal accumulates continuously in
the head. The anvil electrode is gradually re-
tracted to give enough space for the formation
of the head. As soon as sufficient quantity of
metal is gathered, the machine switches off and
the product can be removed by its cold end. Nor-
mally, the head is formed to final shape in a me-
chanical or screw-type press in the same heat.
Thus, the process is suitable for manufacturing
components such as automotive exhaust valves,
or steam turbine blades [Altan et al., 1973].
The flat anvil electrode can be replaced by a
water-cooled copper mold into which material is
gathered and formed to close shape and dimen-
sions. Material can be gathered at any point on
the length of the bar by placing a sheath around
one end. The only limitation on size is the avail-
ability of electric current. Commercially avail-
able equipment is capable of upsetting 0.5 to 5
in. (12.5 to 125 mm) diameter bars. As time for
upsetting a head of average size is 2 to 5 min,
several units are required for achieving high vol-
ume production.
12.4 Ring-Rolling Mills
The principle of operation of a horizontal
ring-rolling mill is illustrated in Fig. 12.11. The
vertical mills operate essentially in the same
way. The doughnut-shaped blank is placed over
a mandrel with a diameter smaller than the in-
side diameter of the blank. The mandrel, in mov-
ing laterally toward the main roll, applies pres-
sure on the blank. The main roll, which is driven,
rotates the blank and the mandrel as the cross
section of the blank is reduced. The axial rolls
provide support to the deforming ring and con-
trol its width and its squareness. As seen in Fig.
12.12, by modifying the configurations of the
mandrel and the main roll, it is possible to roll
rings with internal and external profiles [Beseler,
1969].
For components required in large quantities,
such as bearing races, completely automated
ring-rolling installations are available. Such an
installation may consist of a billet shear, a heat-
ing furnace, a forging press, and a ring-rolling
mill. The principles of an automatic horizontal
ring-rolling mill for manufacturing bearing races
Fig. 12.5
Schematic of a vertical reducer roller. 1, roll stand;
2, holder on manipulator; 3, slide; 4, rolls; 5, part
transfer conveyor. [Haller, 1982]
Fig. 12.4
Deformation stages in reducer rolling of a forging
to produce a truck axle. (a) Starting billet. (b)–(e)
Several reducer roll passes. (1)–(3) Locations where more mate-
rial needed in the final forging. [Haller, 1982]