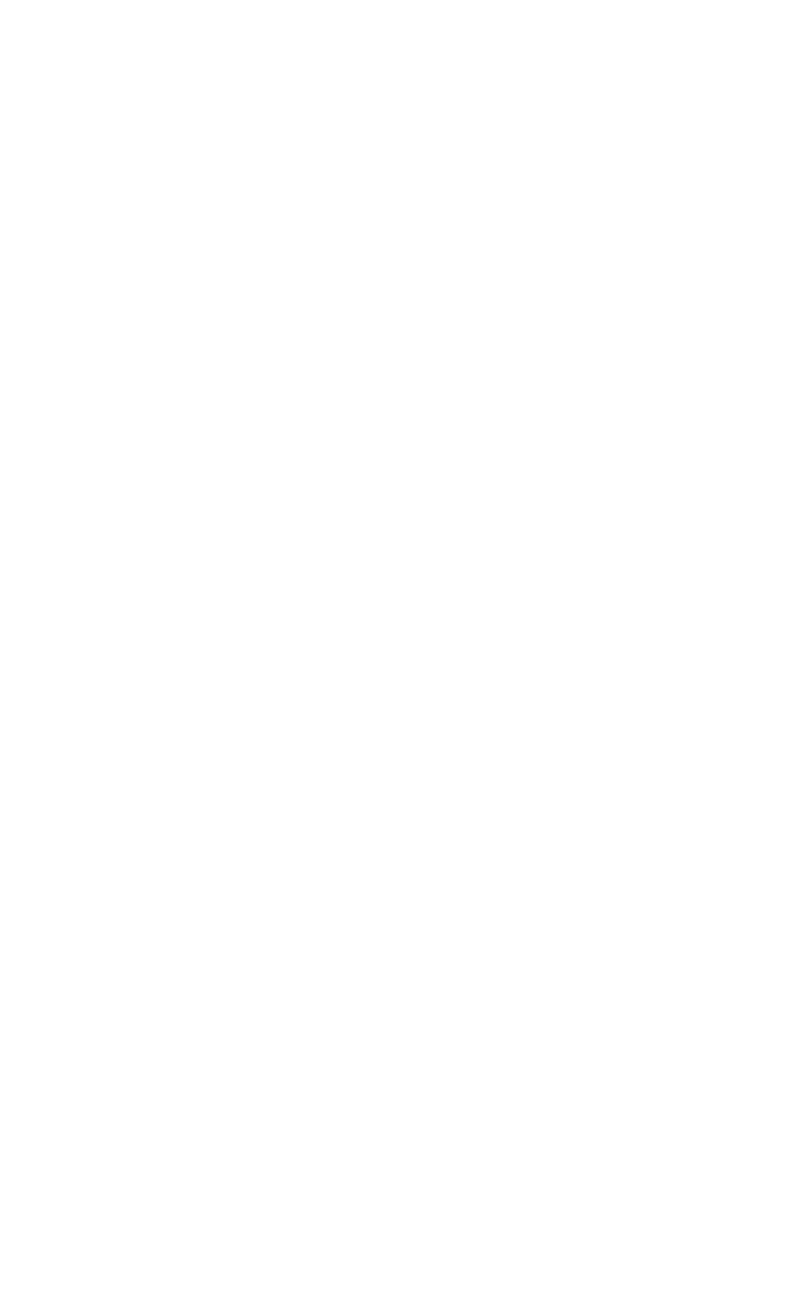
2 / Cold and Hot Forging: Fundamentals and Applications
the workpiece. Forming processes are frequently
used together with other manufacturing pro-
cesses, such as machining, grinding, and heat
treating, in order to complete the transformation
from the raw material to the finished and
assembly-ready part. Desirable material prop-
erties for forming include low yield strength and
high ductility. These properties are affected by
temperature and rate of deformation (strain rate).
When the work temperature is raised, ductility
is increased and yield strength is decreased. The
effect of temperature gives rise to distinctions
among cold forming (workpiece initially at
room temperature), warm forming (workpiece
heated above room temperature, but below the
recrystallization temperature of the workpiece
material), and hot forming (workpiece heated
above the recrystallization temperature). For ex-
ample, the yield stress of a metal increases with
increasing strain (deformation) during cold
forming. In hot forming, however, the yield
stress, in general, increases with strain (defor-
mation) rate.
Forming processes are especially attractive in
cases where:
●
The part geometry is of moderate complexity
and the production volumes are large, so that
tooling costs per unit product can be kept
low (e.g., automotive applications).
●
The part properties and metallurgical in-
tegrity are extremely important (e.g., load-
carrying aircraft, jet engine, and turbine
components).
The design, analysis, and optimization of form-
ing processes require:
●
Engineering knowledge regarding metal
flow, stresses, and heat transfer
●
Technological information related to lubri-
cation, heating and cooling techniques, ma-
terial handling, die design, and forming
equipment [Altan et al., 1983]
The development in forming technology has
increased the range of shapes, sizes, and prop-
erties of the formed products enabling them to
have various design and performance require-
ments. Formed parts are required specifically
when strength, reliability, economy, and resis-
tance to shock and fatigue are essential. The
products can be determined from materials with
the required temperature performance, ductility,
hardness, and machinability [ASM Handbook].
1.2 Characteristics of
Manufacturing Processes
There are four main characteristics of any
manufacturing process—namely, geometry, tol-
erances, production rates, and human and envi-
ronmental factors.
1.2.1 Geometry
Each manufacturing process is capable of pro-
ducing a family of geometries. Within this fam-
ily there are geometries, which can be produced
only with extraordinary cost and effort. For ex-
ample, the forging process allows production of
parts, which can be easily removed from a die
set, that is, upper and lower die. By use of a
“split die” design, it is possible to manufacture
forgings with undercuts and with more complex
shapes.
1.2.2 Tolerances
No variable, especially no dimensional vari-
able, can be produced exactly as specified by the
designer. Therefore, each dimension is associ-
ated with a tolerance. Each manufacturing pro-
cess allows certain dimensional tolerances and
surface finishes to be obtained. The quality of
these variables can always be improved by use
of more sophisticated variations of the process
and by means of new developments. For ex-
ample, through use of the lost-wax vacuum cast-
ing process, it is possible to obtain much more
complex parts with tighter tolerances than are
possible with ordinary sand casting methods. Di-
mensional tolerances serve a dual purpose. First,
they allow proper functioning of the manufac-
tured part: for example, an automotive brake
drum must be round, within limits, to avoid vi-
brations and to ensure proper functioning of the
brakes. The second role of dimensional toler-
ances is to provide interchangeability. Without
interchangeability—the ability to replace a de-
fective part or component (a bearing, for ex-
ample) with a new one, manufactured by a dif-
ferent supplier—modern mass production would
be unthinkable. Figure 1.1 shows the dimen-
sional accuracy that is achievable by different
processes. The values given in the figure must
be considered as guidance values only.
Forming tolerances represent a compromise
between the accuracy desired and the accuracy
that can be economically obtained. The accuracy
obtained is determined by several factors such