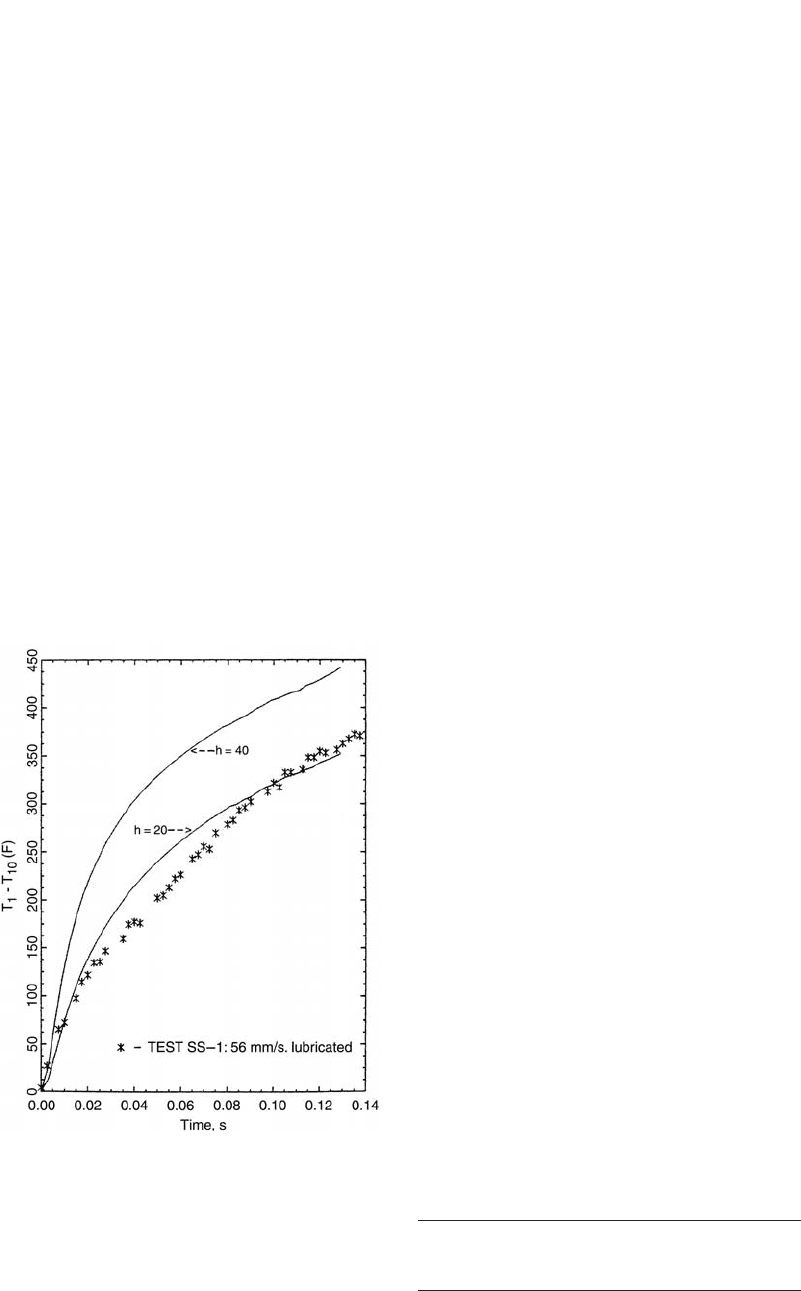
64 / Cold and Hot Forging: Fundamentals and Applications
Table 6.1 Process conditions for nonisothermal
304 stainless steel ring tests
Lubricant Deltaforge
Initial ring temperature, F(C) 2000 (1093)
Initial die temperature, F(C) 600 (316)
Ram speed, in./s (mm/s) 2.2 (56)
Fig. 6.9
The increase of the bottom die temperature (the in-
stantaneous die temperature T
1
minus the initial die
temperature T
10
) versus time obtained from experiments and
FEM generated calibration curves (h ⳱ 0.0068 btu/s/in.
2
/F, o r
20 kW/m
2
• K, and h ⳱ 0.0136 btu/s/in.
2
/F, or 40 kW/m
2
• K)
for the nonisothermal ring tests of 304 stainless steel. Lubricant,
Deltaforge; ram speed, 2.2 in./s (56 mm/s); initial die tempera-
ture, T
10
⳱ 600 F (316 C); initial ring temperature, T
20
⳱ 2000
F (1093 C)
The following conclusions were drawn from
these experiments conducted in references
[Semiatin et al., 1987] and [Burte et al., 1989]:
●
The interface heat transfer coefficient in-
creases with forging pressures. When the
workpiece is free resting on a die, the heat
transfer coefficient is an order of magnitude
smaller than during forging, when there is
pressure at the die/workpiece interface.
●
The value of the interface heat transfer co-
efficient is unchanged above a certain thresh-
old pressure. This threshold value is approx-
imately 2 ksi (14 MPa) in this test.
●
The value of the interface heat transfer co-
efficient under deformation conditions is
about 0.0068 btu/s/in.
2
/F (20 kW/m
2
• K)
for all the combinations of workpiece/die
material pairs used.
●
The value of the interface heat transfer co-
efficient under free resting condition is about
0.00034 btu/s/in.
2
/F (1 kW/m
2
• K).
6.6 Influence of Press Speed and
Contact Time on Heat Transfer
The heat transfer and hence the temperature
history of the workpiece is also influenced by
the forging equipment. Hydraulic press has
lower speed and lower strain rate during defor-
mation. Mechanical press and screw press have
higher speed and higher strain rate during de-
formation. Hydraulic press has a longer dwell
time before the deformation, which results in
longer free resting heat transfer between the
workpiece and the dies. Experimental work on
the determination and comparison of the char-
acteristics of forging presses was carried out on
rings made from selected steel, titanium, and
aluminum alloys [Douglas et al., 1971]. Finite
element modeling was carried out to simulate
the experiments and perform quantitative com-
parison of press speed and contact time on heat
transfer in nonisothermal ring compression tests
[Im et al., 1988a] and [Im et al., 1988b].
Ti-6242 and Al6061 ring compression tests
were simulated using FEM package ALPID (a
parent version of DEFORM娂). The process
conditions used in the computer simulation such
as the dimensions of the rings, the ram speeds
of the forging equipment, and the reduction in
height of the rings were all identical in the ex-
periments [Douglas et al., 1971]. The shear fric-
tion factor used was the factor measured from
the experimental ring tests. The interface heat
transfer coefficient used was based on the ex-
perimental work [Semiatin et al., 1987]. Table
6.2 gives the conditions used in the finite ele-
ment modeling. The hydraulic press used had a
capacity of 700 metric tons. The ram velocity
was assumed constant during deformation. Me-
chanical press used was a high-speed Erie press
with scotch yoke design, rated at 500 metric tons
at 0.25 in. (6.4 mm) above the bottom dead cen-
ter. It had a stroke of 10 in. (250 mm) and a
nominal speed of 90 strokes/min. As for the
screw press, a Weingarten PSS 255 with a nom-
inal rating of 400 metric tons, 2250 mkg (22 ⳯
10
3
J) energy, was used. The starting speed of
the mechanical press and screw press is shown
in Table 6.2.